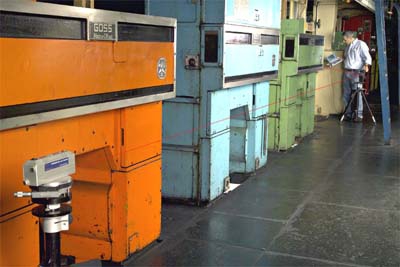
Pinpoint Laser Systems is introducing a revolutionary new 2-dimensional Microgage for precision measuring, machine alignment, calibration, and other demanding industrial applications. Roll and web lines, CNC cutting and milling equipment, lathes, stamping presses, injection molding machines, extrusion systems and other production equipment are easily checked and aligned for improved operating efficiency and reduced downtime with this new Microgage. The new Microgage 2D is compact, easy to set-up and use right on the factory floor. The attached photograph shows the new Microgage 2D checking roller parallelism on a long multi-color printing press. The Microgage 2D is easy to use with instructions that show up on the display guiding the operator through their alignment project. This product combines a compact laser transmitter with a receiver and digital display. As the laser moves across the receiver in a vertical or horizontal direction the display provides a reading of the motion, accurate to 0.0001 inch. This new Microgage will operate over a distance of 100 feet with a bright red beam that is quickly adaptable to many industrial applications. Several simple accessories allow for alignment of straightness, runout, parallelism, squareness, roll and web alignment, shaft and bore alignment, flatness measuring and much more. The 2 Axis Laser Microgage operates on batteries for added convenience and all components are machined of solid aluminum with a hard anodized coating for wear resistance. A sealed push button keypad and large LCD display make the Microgage 2D easy and convenient to use in demanding industrial environments. A serial and USB interface connect to a laptop or PC and link to popular spreadsheets for plotting and analyzing data for maintenance records, customer compliance and other uses. This Microgage system includes a compact carrying case to store the components and is easily carried onto the manufacturing floor.
Contact Details
Related Glossary Terms
- calibration
calibration
Checking measuring instruments and devices against a master set to ensure that, over time, they have remained dimensionally stable and nominally accurate.
- computer numerical control ( CNC)
computer numerical control ( CNC)
Microprocessor-based controller dedicated to a machine tool that permits the creation or modification of parts. Programmed numerical control activates the machine’s servos and spindle drives and controls the various machining operations. See DNC, direct numerical control; NC, numerical control.
- extrusion
extrusion
Conversion of an ingot or billet into lengths of uniform cross section by forcing metal to flow plastically through a die orifice.
- gang cutting ( milling)
gang cutting ( milling)
Machining with several cutters mounted on a single arbor, generally for simultaneous cutting.
- milling
milling
Machining operation in which metal or other material is removed by applying power to a rotating cutter. In vertical milling, the cutting tool is mounted vertically on the spindle. In horizontal milling, the cutting tool is mounted horizontally, either directly on the spindle or on an arbor. Horizontal milling is further broken down into conventional milling, where the cutter rotates opposite the direction of feed, or “up” into the workpiece; and climb milling, where the cutter rotates in the direction of feed, or “down” into the workpiece. Milling operations include plane or surface milling, endmilling, facemilling, angle milling, form milling and profiling.
- wear resistance
wear resistance
Ability of the tool to withstand stresses that cause it to wear during cutting; an attribute linked to alloy composition, base material, thermal conditions, type of tooling and operation and other variables.
- web
web
On a rotating tool, the portion of the tool body that joins the lands. Web is thicker at the shank end, relative to the point end, providing maximum torsional strength.