Contact Details
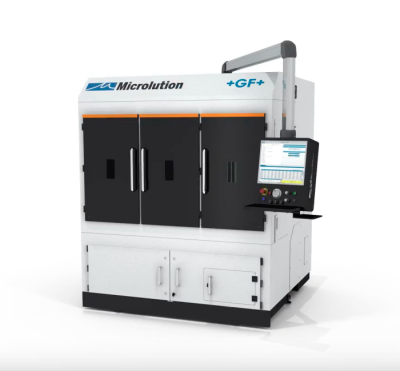
GF Machining Solutions offers the Microlution MLDS, the next generation in femtosecond laser processing systems. The dual-station/dual-part laser machining center provides extremely high laser “on time” via measurement and
loading functions performed as parallel processes alongside machining operations.
Configured as a hybrid platform with high-speed milling spindles, the MLDS further boosts overall productivity while simplifying and expanding a shop’s part-processing potential. As a hybrid configuration, the MLDS removes the bulk of material mechanically and finishes parts with femtosecond laser quality. This dual functionality can significantly reduce total part cycle time.
The MLDS features dual tilt/rotary part tables. On each table, the machine can perform either 5-axis conventional milling or 5-axis femtosecond laser machining. Pick-and-place automation moves workpieces in and out of the
machine and allows for continuous as well as lights-out operations.
Designed as an economical micron-scale machining system, the MLDS is optimized for microscale holemaking and fine cutting without the creation of heat-affected zones in workpieces. The combination of quick axial acceleration,
exceptional stability, precise part handling and motion control with integrated part characterization and measurement delivers ultraprecise machining with high accuracy, speed and quality.
Related Glossary Terms
- conventional milling ( up milling)
conventional milling ( up milling)
Cutter rotation is opposite that of the feed at the point of contact. Chips are cut at minimal thickness at the initial engagement of the cutter’s teeth with the workpiece and increase to a maximum thickness at the end of engagement. See climb milling.
- gang cutting ( milling)
gang cutting ( milling)
Machining with several cutters mounted on a single arbor, generally for simultaneous cutting.
- laser machining
laser machining
Intensified, pulsed beams of light generated by lasers—typically carbon dioxide or neodium-doped yttrium aluminum garnet (Nd:YAG)—that drill, weld, engrave, mark, slit and caseharden. Usually under CNC, often at both high cutting rates (100 linear in./sec.) and high power (5kW or more). Lasers also are used in conjunction with in-process quality-control monitoring systems allowing measuring accuracies of 0.00001".
- machining center
machining center
CNC machine tool capable of drilling, reaming, tapping, milling and boring. Normally comes with an automatic toolchanger. See automatic toolchanger.
- milling
milling
Machining operation in which metal or other material is removed by applying power to a rotating cutter. In vertical milling, the cutting tool is mounted vertically on the spindle. In horizontal milling, the cutting tool is mounted horizontally, either directly on the spindle or on an arbor. Horizontal milling is further broken down into conventional milling, where the cutter rotates opposite the direction of feed, or “up” into the workpiece; and climb milling, where the cutter rotates in the direction of feed, or “down” into the workpiece. Milling operations include plane or surface milling, endmilling, facemilling, angle milling, form milling and profiling.
- parallel
parallel
Strip or block of precision-ground stock used to elevate a workpiece, while keeping it parallel to the worktable, to prevent cutter/table contact.