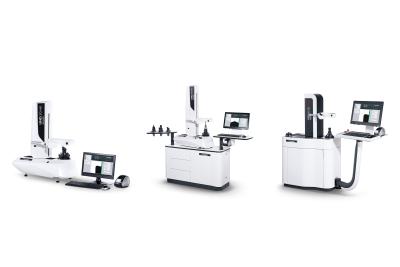
Successful machining requires powerful machines and highly-precise tool holding technology, which ensures that the precision is transferred from the spindle right to the cutting tool edge. Within the last couple of years, HAIMER says it has become the complete system provider for tool management. Managing Director and President of the Haimer Group Andreas Haimer summarizes the development as follows: "After the recent acquisition of Microset GmbH from DMG MORI and the expansion of our product portfolio we are now able to offer the entire process chain from one single source."
For him it was especially important that the Microset presetting devices meet the high-quality standards of HAIMER. Haimer explains that there is absolutely no doubt that the quality is met because "all Microset machines - starting with the entry-level models up to the fully automated measuring machines - distinguish themselves through first-class hardware, ideal ergonomics, as well as easy handling. They are supported by a stable cast iron base construction which reduces the need for frequent calibration and helps subsequent problems in the production environment.
One highlight from the comprehensive product portfolio is the VIO linear series. A linear drive provides for efficient and highly precise presetting of drilling, milling and turning tools. The direct drive within the X- and Z-axis offers the user a dynamic positioning precision and reliability of even the largest tooling. The repeatability of +/- 2μm indicates the high degree of quality inherent in these machines. The increased speed of linear drive can guarantee a productivity increase of up to 25 percent during the measuring process – all of that at a good price-performance ratio.
All machines of the HAIMER Microset VIO series have a modular design to cover a wide spectrum of needs. Tools that weigh up to 160kg and have a diameter and measuring length of up to 1,000mm can be measured. Depending on your needs, the devices can be upgraded to fully automated CNC measuring machines with integrated HAIMER shrinking technology. The unique design ensures ergonomic functionality for ideal ease of use for the operator. This applies both to the spindle access as well as the central control panel.
The innovative one-hand-operation makes it possible to manually or automatically measure the axes and guarantees a μm-precise fine positioning. Finally, maximum quality during the manufacturing process is achievable through fast and exact measuring with the image editing software Microvision VIO. The tool measurement is even easier with the help of the large high-resolution flat screen monitor.
With the HAIMER Microset UNO series the focus lies on precise tool presetting as well as consistent performance. Due to the many different options the UNO series offers, price-performance ratio is very good. Next to a Touch-Display, RFID-Chip-System and post-processors for all conventional control systems, the equipment options also include upgrades such as autofocus or automatic drive. The difference between the UNO autofocus and the manual version is the ability to automatically focus on the cutting edge with a CNC system in the c-axis. For tools with many cutting edges, this option is a proven time saver.
Furthermore, the automatic drive version independently positions the different planes in the Z-axis and automatically approaches the X-axis. The user does not need any special skills, because with the push of a button the machine independently measures complex tools with multiple cutting edges and levels. If required both versions can also be operated manually like the standard model.
The UNO series machines are available in two different sizes. The series starts with the UNO 20/40 with a maximum tool length of 400mm on the Z-axis; the UNO 20/70 has a maximum tool length of 700mm. Both versions are available as table devices with a 19" flat screen. A 22" or 23" touch display and the comfort system cabinet is also available as an option. By using the snap gauge method even the standard models offer the possibility to measure tools with a diameter of up to 100mm. With use of spindle adaptors that configure to the base SK50 taper interface, it is possible to also use most popular interfaces such as HSK, Capto, VDI, KM or BMT.
The FEM optimized and thermostable cast iron construction is the solid foundation of the Mircoset tool presetting machines. The rigid base unit with a three-point-support system provides stable and safe positioning of the machine and ensures an overall easy set-up for the highest possible flexibility in production. Additional features such as visual inspection camera mode and optional "infinite fine adjustment" further enhance the functionality of the machines.
With its release-by-touch, function (an intelligent sensor control to measure the X- and Z-axis) the UNO series is reportedly setting new standards for entry-level tool presetting machines by making them easier than ever to use.
Microvision UNO offers the operators intuitive functionality that produces very precise measuring results. A precise focus window enhances the accuracy and even provides accurate measurement values for the most complex tools. The UNO series is rounded off with options like a thermo-label printer, a vacuum clamping system, a second camera for presetting stationary turning tooling and a highly precise ISS spindle with direct clamping adapter (2μm accuracy).
Andreas Haimer summarizes: "Microset offers a high-performance alternative and solution to every customer who wants to purchase something new in the area of presetting technology. Even if your presetting room is currently equipped with other technology it definitely pays off to purchase new presetting devices whenever you invest in new machines. This way you can prevent long waiting periods and also avoid machine breakdown. The easy and intuitive operation of the machines guarantees that even in a three-shift-operation the devices can be operated by every single employee. In short, in order to use the Microset devices you don't need to be trained for weeks in advance and you don't need to place them in an air-conditioned measuring room to get repeatable results."
Contact Details
Related Glossary Terms
- calibration
calibration
Checking measuring instruments and devices against a master set to ensure that, over time, they have remained dimensionally stable and nominally accurate.
- computer numerical control ( CNC)
computer numerical control ( CNC)
Microprocessor-based controller dedicated to a machine tool that permits the creation or modification of parts. Programmed numerical control activates the machine’s servos and spindle drives and controls the various machining operations. See DNC, direct numerical control; NC, numerical control.
- flat ( screw flat)
flat ( screw flat)
Flat surface machined into the shank of a cutting tool for enhanced holding of the tool.
- gang cutting ( milling)
gang cutting ( milling)
Machining with several cutters mounted on a single arbor, generally for simultaneous cutting.
- milling
milling
Machining operation in which metal or other material is removed by applying power to a rotating cutter. In vertical milling, the cutting tool is mounted vertically on the spindle. In horizontal milling, the cutting tool is mounted horizontally, either directly on the spindle or on an arbor. Horizontal milling is further broken down into conventional milling, where the cutter rotates opposite the direction of feed, or “up” into the workpiece; and climb milling, where the cutter rotates in the direction of feed, or “down” into the workpiece. Milling operations include plane or surface milling, endmilling, facemilling, angle milling, form milling and profiling.
- modular design ( modular construction)
modular design ( modular construction)
Manufacturing of a product in subassemblies that permits fast and simple replacement of defective assemblies and tailoring of the product for different purposes. See interchangeable parts.
- turning
turning
Workpiece is held in a chuck, mounted on a face plate or secured between centers and rotated while a cutting tool, normally a single-point tool, is fed into it along its periphery or across its end or face. Takes the form of straight turning (cutting along the periphery of the workpiece); taper turning (creating a taper); step turning (turning different-size diameters on the same work); chamfering (beveling an edge or shoulder); facing (cutting on an end); turning threads (usually external but can be internal); roughing (high-volume metal removal); and finishing (final light cuts). Performed on lathes, turning centers, chucking machines, automatic screw machines and similar machines.