Contact Details
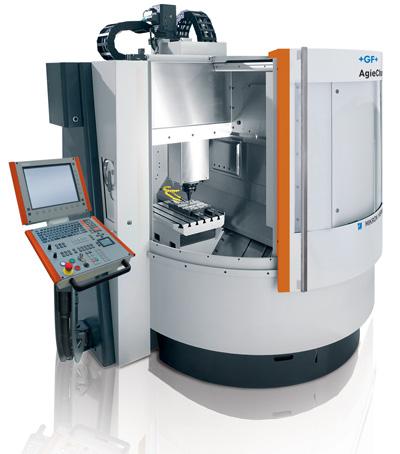
GF Machining Solutions designed its new Mikron HSM 500 MoldMaster (MM) high-speed milling machine with today's mold and die makers in mind. As an all-in-one production system, the machine's specific features and capabilities give shops the versatility to produce a wide scope of mold and die related components, from 58-HRC steel mold cores to hot pressing dies and even sinker-EDM electrodes for intricate mold cavities, all with one machine tool.
For high-speed, the machine is equipped with a 42,000-rpm HSK spindle that uses ceramic hybrid ball bearings with oil-air minimal lubrication, as well as liquid cooled stator jacket and bearings. This vector controlled motor spindle ensures extremely fast acceleration to full speed as well as high torque at low speeds. As a complement to the high-speed spindle, the machine cuts at feedrates up to 784.4 ipm (20 m/min) and rapid traverses as fast as 1,574.8 ipm (42 m/min).
As standard, the HSM 500mm comes equipped with graphite extraction system touch probe capability and absolute optical linear scales with 20-nanometer step resolution on its X, Y, and Z axes for extremely precise machine positioning. Also, the machine minimizes any thermal effects on accuracy through its polymer granite base material and liquid-cooled feed and drive motors, spindle motor and electrical cabinet.
The HSM 500mm's portal construction, which is a pyramid-shaped design, delivers stability and high rigidity yet allows for a compact machine footprint. All machine cross slides are weight optimized and fulfill the requirements for highly dynamic machine motion.
As added stability, the machine's polymer granite base material completely dampens vibration up to six times better than that of standard gray cast iron base material. The polymer concrete is impervious to oils or cooling lubricants, and unlike other base materials, does not require an aging process.
Equipped with SmartMachine functionalities, the HSM 500mm increases tool life through vibration monitoring, boosts productivity by reducing machine warm-up wait time and shortens cycle times with optimized machine motion. The SmartMachine Advanced Process System displays vibrations occurring during the milling process as a G-load, allowing machinists to intervene and adjust for optimized cutting conditions and part surface finishes.
With the Intelligent Thermal Control SmartMachine function, operators will not have to wait long for the HSM 500mm to settle into a thermal steady state before beginning to machine parts. The machine actively compensates for any thermal displacement of the cutting tool's centerline. For optimized cutting paths and better part surface finishes, the SmartMachine Operator Support System on the HSM 500mm makes it possible for operators to access the internal parameters of the machine's CNC. Through a simple and understandable interface, operators set specific target data, and the system automatically adjusts the machine's dynamic behavior accordingly.
In addition to its high-speed spindle, as well as fast and precise machine motion, the HSM 500mm is equipped with other features tailored specifically to graphite machining, as for the production of sinker EDM electrodes to burn mold cavities. A hood protects the machine, and its axes are fully covered, while an automatic central lubrication system ensures all linear guides and ballscrews are lubricated without having to remove any protective machine covering. And to quickly evacuate graphite dust, the machine has two powerful suction units and two separate dust bins.
Related Glossary Terms
- computer numerical control ( CNC)
computer numerical control ( CNC)
Microprocessor-based controller dedicated to a machine tool that permits the creation or modification of parts. Programmed numerical control activates the machine’s servos and spindle drives and controls the various machining operations. See DNC, direct numerical control; NC, numerical control.
- electrical-discharge machining ( EDM)
electrical-discharge machining ( EDM)
Process that vaporizes conductive materials by controlled application of pulsed electrical current that flows between a workpiece and electrode (tool) in a dielectric fluid. Permits machining shapes to tight accuracies without the internal stresses conventional machining often generates. Useful in diemaking.
- feed
feed
Rate of change of position of the tool as a whole, relative to the workpiece while cutting.
- gang cutting ( milling)
gang cutting ( milling)
Machining with several cutters mounted on a single arbor, generally for simultaneous cutting.
- inches per minute ( ipm)
inches per minute ( ipm)
Value that refers to how far the workpiece or cutter advances linearly in 1 minute, defined as: ipm = ipt 5 number of effective teeth 5 rpm. Also known as the table feed or machine feed.
- milling
milling
Machining operation in which metal or other material is removed by applying power to a rotating cutter. In vertical milling, the cutting tool is mounted vertically on the spindle. In horizontal milling, the cutting tool is mounted horizontally, either directly on the spindle or on an arbor. Horizontal milling is further broken down into conventional milling, where the cutter rotates opposite the direction of feed, or “up” into the workpiece; and climb milling, where the cutter rotates in the direction of feed, or “down” into the workpiece. Milling operations include plane or surface milling, endmilling, facemilling, angle milling, form milling and profiling.
- milling machine ( mill)
milling machine ( mill)
Runs endmills and arbor-mounted milling cutters. Features include a head with a spindle that drives the cutters; a column, knee and table that provide motion in the three Cartesian axes; and a base that supports the components and houses the cutting-fluid pump and reservoir. The work is mounted on the table and fed into the rotating cutter or endmill to accomplish the milling steps; vertical milling machines also feed endmills into the work by means of a spindle-mounted quill. Models range from small manual machines to big bed-type and duplex mills. All take one of three basic forms: vertical, horizontal or convertible horizontal/vertical. Vertical machines may be knee-type (the table is mounted on a knee that can be elevated) or bed-type (the table is securely supported and only moves horizontally). In general, horizontal machines are bigger and more powerful, while vertical machines are lighter but more versatile and easier to set up and operate.