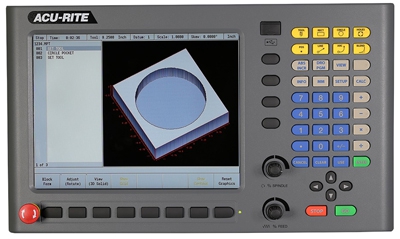
The ACU-RITE MILLPWRG2 control is an easy-to-operate CNC for vertical knee and bed mills, and is available with an optional AMIG2 console offering users the ability to use common interfaces as well as control its host machine tool's spindle.
This compact AMIG2 electrical cabinet is available in two configurations:
- The AMIG2 Standard has I/O that can be used for various purposes. For example: Machine guards, Limit switches, Automatic oiler, AMI Program Step. The AMI Program Step allows the programmer to specify the outputs to be turned ON or OFF, or PULSED for a certain duration. This can be used to control external devices such as an indexer. The AMIG2 Standard can also be used with an inverter-controlled spindle. The spindle control console is required for inverter-controlled spindle. The console provides the standard +10 Vdc and a spindle override knob.
- The AMIG2 Deluxe includes everything in the Standard configuration plus the ability to control spindle and coolant pump using M-Functions for controlling direction (forward or reverse) and turning the spindle off.
The ACU-RITE MILLPWRG2 control is equipped with full 3-D contouring capabilities and is available as a complete retrofit package for two- or three-axis knee or bed mills or on a new mill from a machine builder. It continues to provide machinists the convenience of straightforward 2-½-axis conversational shop floor programming as well as powerful calculators, eliminating the need for time-consuming manual calculations and to learn complicated programs.
ACU-RITE maintains its operator-friendly design concept by offering a sturdy operator console on the MILLPWRG2 that features a 12.1-inch flat panel, color LCD display; a color-coded well-organized keypad; USB and remote stop/go pendant which are all standard equipment.
Contact Details
Related Glossary Terms
- 3-D
3-D
Way of displaying real-world objects in a natural way by showing depth, height and width. This system uses the X, Y and Z axes.
- computer numerical control ( CNC)
computer numerical control ( CNC)
Microprocessor-based controller dedicated to a machine tool that permits the creation or modification of parts. Programmed numerical control activates the machine’s servos and spindle drives and controls the various machining operations. See DNC, direct numerical control; NC, numerical control.
- coolant
coolant
Fluid that reduces temperature buildup at the tool/workpiece interface during machining. Normally takes the form of a liquid such as soluble or chemical mixtures (semisynthetic, synthetic) but can be pressurized air or other gas. Because of water’s ability to absorb great quantities of heat, it is widely used as a coolant and vehicle for various cutting compounds, with the water-to-compound ratio varying with the machining task. See cutting fluid; semisynthetic cutting fluid; soluble-oil cutting fluid; synthetic cutting fluid.
- flat ( screw flat)
flat ( screw flat)
Flat surface machined into the shank of a cutting tool for enhanced holding of the tool.
- milling machine ( mill)
milling machine ( mill)
Runs endmills and arbor-mounted milling cutters. Features include a head with a spindle that drives the cutters; a column, knee and table that provide motion in the three Cartesian axes; and a base that supports the components and houses the cutting-fluid pump and reservoir. The work is mounted on the table and fed into the rotating cutter or endmill to accomplish the milling steps; vertical milling machines also feed endmills into the work by means of a spindle-mounted quill. Models range from small manual machines to big bed-type and duplex mills. All take one of three basic forms: vertical, horizontal or convertible horizontal/vertical. Vertical machines may be knee-type (the table is mounted on a knee that can be elevated) or bed-type (the table is securely supported and only moves horizontally). In general, horizontal machines are bigger and more powerful, while vertical machines are lighter but more versatile and easier to set up and operate.
- turning
turning
Workpiece is held in a chuck, mounted on a face plate or secured between centers and rotated while a cutting tool, normally a single-point tool, is fed into it along its periphery or across its end or face. Takes the form of straight turning (cutting along the periphery of the workpiece); taper turning (creating a taper); step turning (turning different-size diameters on the same work); chamfering (beveling an edge or shoulder); facing (cutting on an end); turning threads (usually external but can be internal); roughing (high-volume metal removal); and finishing (final light cuts). Performed on lathes, turning centers, chucking machines, automatic screw machines and similar machines.