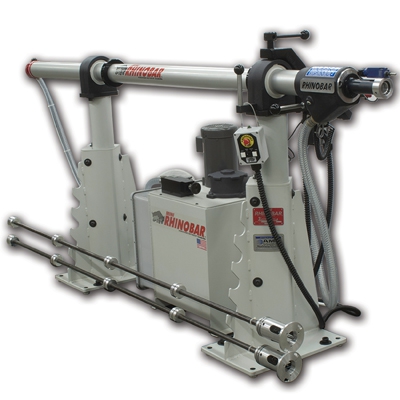
Lexair's Mini Rhinobar bar feeder automatically centers and feeds small-diameter bar stock to maximize the productivity of Swiss-style CNC screw machines and small fixed- or sliding-head lathes. The precision engineered single-tube bar feeder uses the hydrodynamic principle to quickly center 6- (1.8 m) or 12-foot (3.6 m) bars as small as 0.04 inches (1mm) diameter. The bar stock is supported in an oil bath in the feed tube, and as the bar's rotational speed increases hydrodynamic forces move it toward the center of the tube and stabilize it, delivering shorter cycle times and superior workpiece finishes. Feed tubes ranging from 0.125 to 1.625 inches (3.2 to 41mm) diameter are available in 0.125-inch (3.2mm) increments to minimize the bar-to-feed tube clearance and achieve maximum throughput on automotive components, medical devices, motor shafts and other small-diameter, high-production-run parts.
The bar feeder's ergonomic design features an upgraded safety interlock system, and includes a front swing-out mechanism for easy reloading and sub 3-minute feed tube changes. Lexair's single-valve design controls oil flow and pressure for increased bar control, accuracy and vibration-free operation. A completely enclosed fluid recuperator keeps oil off the floor and contaminants out of the hydraulic system.
The outer barrel is a precision-extruded aluminum tube, held in place with a single clamp to further minimize barrel vibration and control Z-axis motion. A removable pendant allows the operator to control the bar feeder remotely, while a positive pusher retention system ensures high efficiency operation with minimal labor.
With overall machine lengths of 11 feet (3.35 m) for the 6-foot bar model and 17 feet (5.18 m) for the 12-foot bar model, the Mini Rhinobar's compact size makes it suitable for small or large shops. The U.S.-built bar feeder is available for immediate delivery, and comes with three feed tube diameters of the buyer's selection.
Contact Details
Related Glossary Terms
- centers
centers
Cone-shaped pins that support a workpiece by one or two ends during machining. The centers fit into holes drilled in the workpiece ends. Centers that turn with the workpiece are called “live” centers; those that do not are called “dead” centers.
- clearance
clearance
Space provided behind a tool’s land or relief to prevent rubbing and subsequent premature deterioration of the tool. See land; relief.
- computer numerical control ( CNC)
computer numerical control ( CNC)
Microprocessor-based controller dedicated to a machine tool that permits the creation or modification of parts. Programmed numerical control activates the machine’s servos and spindle drives and controls the various machining operations. See DNC, direct numerical control; NC, numerical control.
- feed
feed
Rate of change of position of the tool as a whole, relative to the workpiece while cutting.