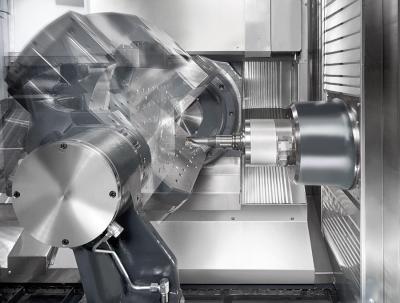
HELLER introduced the new model HF 5500 5-axis horizontal machining center equipped with pallet changer and offering a work envelope of 900mm x 950mm x 900mm and a maximum pallet load of 750kg.
With the 5th axis is provided by the workpiece for dynamic five-sided and simultaneous 5-axis machining, and HELLER's typical horizontal spindle ensuring quick tool changes and short idle times, the HF series offers substantial productivity advantages. In addition, three linear axes in X, Y and Z, are equipped with absolute measuring systems and two direct driven dynamic rotary axes in A and B integrated into a swivel rotary table.
The high speed of the A and B rotary axes is achieved through minimized mass moment of inertia and the use of direct drives. Optionally, the powerful dynamics can be increased further with the “Speed-Dynamics Package.” According to HELLER, it provides 10 percent shorter chip-to-chip times. For an additional reduction in idle times, the HF series provides a high-speed NC tool changer with lift-and-swivel principle.
Contrary to comparable machines on the market, HELLER has equipped the new series with a counter bearing as a unique selling point. The use of the counter bearing in combination with a YRT bearing results in high rigidity for handling high loads.
High flexibility was another priority for HELLER in the development of the machine: the machine is either available in table design or equipped with pallet changer.
The HF provides a wide choice of spindles to suit different applications.
While the standard version is equipped with the powerful SC63 SpeedCutting motor spindle with HSK-A63 (18,000rpm, 100Nm), making it ideal for the machining of light metals, the optional PC63 PowerCutting spindle unit (12,000rpm, 201Nm) provides the necessary torque for high-performance cutting of cast iron and steel.
As further options, HELLER offers motor spindles with HSK-A100. The SC 100 spindle unit (12,000rpm, 201Nm) provides increased stability of tools and high speeds for universal application, whereas the PC 100 spindle unit (10,000rpm, 354Nm) offers high torque for use with large and heavy tools.
The HF series provides large workpiece interference contours. Contrary to conventional 5-axis machining centers, HELLER's concept is not only based on single-part clamping, but provides the possibility of multiple clamping or the clamping of very large components (e.g. transmission cases using 'window-type' fixtures).
To provide sufficient space in the work area, the workpiece interference contour of model HF 5500 was increased by 800mm in height and 900mm in diameter compared to model HF 3500. Despite the large interference contour there are hardly any limitations as far as the degrees of freedom are concerned. The machine enables swivel movements of the rotary table through 150° (30° to -120°) and with certain restrictions even through 225°. The HELLER HF machining centers leave nothing to be desired when it comes to the disposal of short- or long-chipping materials. This is guaranteed through free chip fall during horizontal machining, steep side walls and stainless steel slat coverings as well as the centrally arranged open chip conveyor.
With the HF series, HELLER is presenting its new HELLER Operation Interface, the new operating panel with 24" screen technology and touch controls, quick access technology in the control and XTENDS optional expansion applications to support the user. The optional work area camera, for example, optimally supports setting and monitoring functions during the CNC process.
For decades, HELLER has been synonymous with efficient production processes and high machining quality. This also applies to the well-conceived connection to all current automation systems. Target users will be particularly interested in flexible integration into existing production systems. The new machine series is also flexible and customer-oriented in terms of tooling. The new machining centers enable continued use of existing tools from other HELLER machines and the use of manual clamping fixtures. Adaptation of hydraulically operated clamping fixtures is also possible.
Contact Details
Related Glossary Terms
- centers
centers
Cone-shaped pins that support a workpiece by one or two ends during machining. The centers fit into holes drilled in the workpiece ends. Centers that turn with the workpiece are called “live” centers; those that do not are called “dead” centers.
- computer numerical control ( CNC)
computer numerical control ( CNC)
Microprocessor-based controller dedicated to a machine tool that permits the creation or modification of parts. Programmed numerical control activates the machine’s servos and spindle drives and controls the various machining operations. See DNC, direct numerical control; NC, numerical control.
- degrees of freedom
degrees of freedom
Number of axes along which a robot, and thus the object it is holding, can be manipulated. Most robots are capable of maneuvering along the three basic Cartesian axes (X, Y, Z). More sophisticated models may move in six or more axes. See axis.
- machining center
machining center
CNC machine tool capable of drilling, reaming, tapping, milling and boring. Normally comes with an automatic toolchanger. See automatic toolchanger.
- numerical control ( NC)
numerical control ( NC)
Any controlled equipment that allows an operator to program its movement by entering a series of coded numbers and symbols. See CNC, computer numerical control; DNC, direct numerical control.
- work envelope
work envelope
Cube, sphere, cylinder or other physical space within which the cutting tool is capable of reaching.