Contact Details
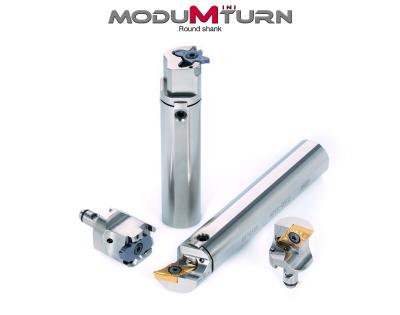
Tungaloy has updated its ModuMiniTurn modular turning tool system for Swiss machines by adding 30 new round shank toolholders that are suitable for machining the back side of the parts in the sub spindle.
The ModuMiniTurn modular turning tool system incorporates an advanced coupling mechanism between the modular head and tool shank, providing exceptional repeating accuracy for the cutting point. This system achieves repeatability accuracy within the 5 μm range, minimizing downtime during tooling changeovers. The system offers standard modular heads for a range of applications, including forward turning, back turning, grooving, thread turning, parting, and productive Y-axis turning.
The new round shank toolholders are designed to fit the cylindrical shank tool holders in most Swiss type lathes. Just as with the existing ModuMiniTurn square shank toolholders, the new round shank toolholders also features extremely high repeatability accuracy, which significantly reduces downtime.
The modular heads for the round shank toolholders have a QR12 coupling connection and are available for forward turning, grooving, and thread turning applications. The forward turning modular heads come in three standard cutting angle styles of L for 95°, U for 93°, and Q for 107.5°, allowing operators to select optimal cutting angles for operations simply by swapping the modular cutting heads for the inserts.
The shank diameters are available in 16 mm (.630″), 19.05 mm (¾″), and 20 mm (.787″).
Related Glossary Terms
- grooving
grooving
Machining grooves and shallow channels. Example: grooving ball-bearing raceways. Typically performed by tools that are capable of light cuts at high feed rates. Imparts high-quality finish.
- parting
parting
When used in lathe or screw-machine operations, this process separates a completed part from chuck-held or collet-fed stock by means of a very narrow, flat-end cutting, or parting, tool.
- shank
shank
Main body of a tool; the portion of a drill or similar end-held tool that fits into a collet, chuck or similar mounting device.
- turning
turning
Workpiece is held in a chuck, mounted on a face plate or secured between centers and rotated while a cutting tool, normally a single-point tool, is fed into it along its periphery or across its end or face. Takes the form of straight turning (cutting along the periphery of the workpiece); taper turning (creating a taper); step turning (turning different-size diameters on the same work); chamfering (beveling an edge or shoulder); facing (cutting on an end); turning threads (usually external but can be internal); roughing (high-volume metal removal); and finishing (final light cuts). Performed on lathes, turning centers, chucking machines, automatic screw machines and similar machines.