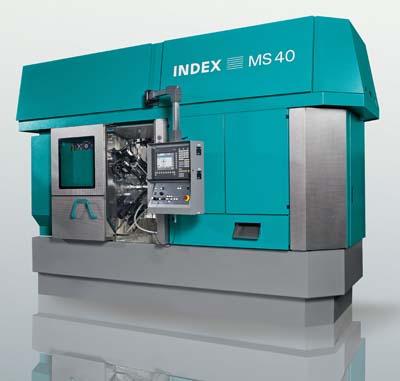
The new INDEX MS40P CNC multi-spindle automatic lathe includes a quillstock with six tool carriers and one counter spindle opposite the main 6-spindle drum, making it possible to machine complex workpieces requiring many tools with highest precision in a single process.
A new concept, the INDEX multispindle affords contract manufacturers the ability to outproduce, by up to 85 percent or more, six or more twin-turret CNC lathes with a single, flexible, high-speed, high precision machine that can work unattended over three shifts.
The flexibility and capability of the machine is well-suited to batch production and for machining families of parts; the front and rear end machining options permit efficient, complete machining of production parts with complex geometry and/or extensive operations on the cutoff end.
The core of the machine is its compact spindle drum. Six fluid-cooled, infinitely variable hollow-shaft motors are able to drive up to 40mm bar stock independently from each other. Other characteristics of the spindle drum are: high torque, small frame size, maintenance-free operation, and an advanced synchronous design. The enhanced machine concept is based on the added A-side (drum side) and an opposite quillstock on the B-side.
Besides the tool carriers in the spindle drum side of the machine, another six tool carriers and a counter spindle are located in the rigid monoblock quillstock. The tool carrier arrangement in the working area without a longitudinal slide block allows the use of more than one tool on each spindle.
The generously dimensioned working area can be easily accessed through sliding doors on both sides of the machine. This is very convenient for the user and greatly reduces setup time. Chips drop directly into the base of the machine. The INDEX modular system allows, on the A-side, customer-specific configuration of up to 12 hydrostatic bearing-supported CNC cross-slides, several Y-axes, and numerous stationary and live tools (for front-end machining) permitting a wide range of machining in a single setup: off-center drilling, deep-hole, drilling, thread cutting, inclined drilling, cross drilling, contour milling, hobbing, and multi-edge turning are only a few of the many possibilities.
The characteristic INDEX V-shaped arrangement of the tool carriers means the optimum machining sequence is the only factor determining the process. For example, external and internal machining operations using stationary or live tools can be performed in every station. During machining, users can program the optimum speed for each independent spindle which can be varied during cutting. The result is excellent surface quality, short production times per piece, and extended tool life. It is also possible to make speed changes during drum indexing, thus avoiding any additional secondary processing times. This capability also makes it possible to machine difficult materials that previously were hardly suitable for multi-spindle machines.
Should the machining options on the A-side (spindle drum) not be sufficient, the extensions on the B-side, the quill version, come into play. The positions 1 to 5 each have a slide that can be used to machine the workpieces on the A-side. In position 6, there is a counter spindle traversing in the Z direction, so users can machine workpieces in positions 6.2 and 6.4. The slide 6.2 can also be used for machining the A-side or for rear end machining on the counter spindle with up to 3 tools. Tool position 6.4 also features a back-boring slide that can be equipped with three boring or turning tools, or with live tools. In total, up to three tools can be used on the A-side simultaneously, and another six tools are available for rear end machining.
Another advantage is the large Z-travel distance of the counter spindle, allowing longitudinal and transverse machining of longer workpieces (shaft parts). A swivel unit places the parts on a conveyor belt that carries them away. The gripper can already move across the part during rear end machining to save time. Instead of placing the finished parts onto the integrated conveyor belt, they can also transferred to a handling system.
The MS40P extends the INDEX multi-spindle machine series by another CNC multi-spindle automatic lathe that in particular, it plays to its strengths with its flexibility and ease of re-tooling.
Contact Details
Related Glossary Terms
- boring
boring
Enlarging a hole that already has been drilled or cored. Generally, it is an operation of truing the previously drilled hole with a single-point, lathe-type tool. Boring is essentially internal turning, in that usually a single-point cutting tool forms the internal shape. Some tools are available with two cutting edges to balance cutting forces.
- computer numerical control ( CNC)
computer numerical control ( CNC)
Microprocessor-based controller dedicated to a machine tool that permits the creation or modification of parts. Programmed numerical control activates the machine’s servos and spindle drives and controls the various machining operations. See DNC, direct numerical control; NC, numerical control.
- cutoff
cutoff
Step that prepares a slug, blank or other workpiece for machining or other processing by separating it from the original stock. Performed on lathes, chucking machines, automatic screw machines and other turning machines. Also performed on milling machines, machining centers with slitting saws and sawing machines with cold (circular) saws, hacksaws, bandsaws or abrasive cutoff saws. See saw, sawing machine; turning.
- gang cutting ( milling)
gang cutting ( milling)
Machining with several cutters mounted on a single arbor, generally for simultaneous cutting.
- lathe
lathe
Turning machine capable of sawing, milling, grinding, gear-cutting, drilling, reaming, boring, threading, facing, chamfering, grooving, knurling, spinning, parting, necking, taper-cutting, and cam- and eccentric-cutting, as well as step- and straight-turning. Comes in a variety of forms, ranging from manual to semiautomatic to fully automatic, with major types being engine lathes, turning and contouring lathes, turret lathes and numerical-control lathes. The engine lathe consists of a headstock and spindle, tailstock, bed, carriage (complete with apron) and cross slides. Features include gear- (speed) and feed-selector levers, toolpost, compound rest, lead screw and reversing lead screw, threading dial and rapid-traverse lever. Special lathe types include through-the-spindle, camshaft and crankshaft, brake drum and rotor, spinning and gun-barrel machines. Toolroom and bench lathes are used for precision work; the former for tool-and-die work and similar tasks, the latter for small workpieces (instruments, watches), normally without a power feed. Models are typically designated according to their “swing,” or the largest-diameter workpiece that can be rotated; bed length, or the distance between centers; and horsepower generated. See turning machine.
- milling
milling
Machining operation in which metal or other material is removed by applying power to a rotating cutter. In vertical milling, the cutting tool is mounted vertically on the spindle. In horizontal milling, the cutting tool is mounted horizontally, either directly on the spindle or on an arbor. Horizontal milling is further broken down into conventional milling, where the cutter rotates opposite the direction of feed, or “up” into the workpiece; and climb milling, where the cutter rotates in the direction of feed, or “down” into the workpiece. Milling operations include plane or surface milling, endmilling, facemilling, angle milling, form milling and profiling.
- turning
turning
Workpiece is held in a chuck, mounted on a face plate or secured between centers and rotated while a cutting tool, normally a single-point tool, is fed into it along its periphery or across its end or face. Takes the form of straight turning (cutting along the periphery of the workpiece); taper turning (creating a taper); step turning (turning different-size diameters on the same work); chamfering (beveling an edge or shoulder); facing (cutting on an end); turning threads (usually external but can be internal); roughing (high-volume metal removal); and finishing (final light cuts). Performed on lathes, turning centers, chucking machines, automatic screw machines and similar machines.