Contact Details
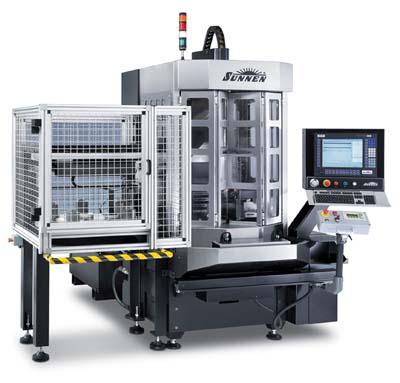
Sunnen says its patented multi-feed honing technology gives gear manufacturers a choice of tool-feed modes to achieve the shortest cycle times, lowest part cost, and longest abrasive life. Multi-feed combines Sunnen's new controlled-force tool-feed with its controlled-rate feed system. The two different tool-feed modes allow the user to select the better option to suit the workpiece geometry, material and tool type/size. Multi-feed technology is available as an option on Sunnen's SV-1000 and SV-500 machines, as well as a retrofit for existing machines in these series.
The new controlled-force tool-feed capability maintains an optimum cutting load on the honing abrasive throughout a cycle, irrespective of the incoming part's hardness, geometry or size variation. It is an ideal choice for applications using segmented diamond or superabrasive honing tools, such as Sunnen'smmT, PH or KRQ tools, or where incoming gear blanks have slight variations in hole diameters, hardness and geometry. Depending on the application, controlled-force honing cuts cycle times by as much as 50 percent, lengthens abrasive life for lower consumable cost, and allows finer control of surface finish parameters. The new technology eliminates glazing of the abrasive, due to too little force, and maintains a steady, free-cutting, self-dressing condition for maximum metal removal in the shortest possible cycle time. Controlled-force honing often allows more-durable abrasives to be used, too, resulting in more parts per set of abrasives and lower cost per part.
Controlled-force honing is an enhancement of Sunnen's controlled-rate system for tool wear compensation, which is already capable of adjusting tool size in increments as fine as 0.1µm (0.000010"). Controlled-rate tool feeding is typically used with plated-diamond CGT honing tools, which use a sleeve of abrasive for full contact with the bore surface. CGT tools are ideal for cast iron and powder metal workpieces, segmented bores, or parts with multiple lands, ports, keyways or crossholes in the bore. Sunnen's machine control provides up to five feed expansion profiles that can be used during a cycle for rapid part touch, cutting, sizing, finishing and spark-out.
Related Glossary Terms
- abrasive
abrasive
Substance used for grinding, honing, lapping, superfinishing and polishing. Examples include garnet, emery, corundum, silicon carbide, cubic boron nitride and diamond in various grit sizes.
- feed
feed
Rate of change of position of the tool as a whole, relative to the workpiece while cutting.
- hardness
hardness
Hardness is a measure of the resistance of a material to surface indentation or abrasion. There is no absolute scale for hardness. In order to express hardness quantitatively, each type of test has its own scale, which defines hardness. Indentation hardness obtained through static methods is measured by Brinell, Rockwell, Vickers and Knoop tests. Hardness without indentation is measured by a dynamic method, known as the Scleroscope test.
- lapping compound( powder)
lapping compound( powder)
Light, abrasive material used for finishing a surface.
- spark-out ( sparking out)
spark-out ( sparking out)
Grinding of a workpiece at the end of a grind cycle without engaging any further down feed. The grinding forces are allowed to subside with time, ensuring a precision surface.