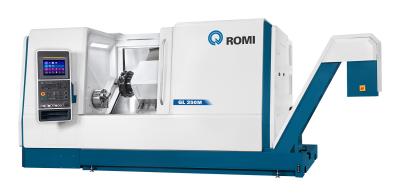
Romi has introduced the New Generation GL Series 2-Axis horizontal turning centers. The new machines are available in four models with maximum cutting diameters ranging from 11” (282 mm) to 19.3” (490 mm) and Z travel ranging from 23.6” (600 mm) to 47.2” (1,200 mm). Designed for medium to high production environments, the GL Series features notably high power, torque and feed force, in addition to Romi’s trademark rigidity and precision attributed to the robust “Romi-made” monoblock base.
Models include the GL250, GL300, GL350, and GL450. Each is constructed with durable roller ways on all axis to produce high rigidity. A built-in spindle motor with a chiller incorporated and direct drive servo-motors results in high response speed, accuracy, less vibration, and lower maintenance requirements. Chilling the motor increases life expectancy, and produces less thermal expansion.
The all new GL Series come standard with active thermal compensation to maintain consistent accuracy even as the machine temperature increases over the course of extended use. The tailstock is programmable and servo-driven. Position, speed, and force are determined directly via the Fanuc controller that reduces setup time.
Each model comes with a 12-station turret with a choice of fixed tools with a Romi disk, driven tools with a VDI or BMT disk, driven tools with Y-axis, or dual spindle with driven tools and Y-axis.
The CNC control features a Fanuc Oi-TF with 15” LCD touchscreen and Fanuc 32iB with 19” LCD touchscreen for dual spindle version machines and is the newest generation of Fanuc’s Series iHMI. It is designed to produce faster, more accurate performance for turning applications with separate areas on the main screen for planning, machining, improvements, and utilities. Functions are accessible with just two clicks. It comes standard with an ethernet interface, as well as a compact flash card and USB ports
Romi’s GL Series turning centers are all produced in Romi’s state-of-the-art facilities that maintain various safety and quality certifications including ISO 9001, ISO 14001, IATF 16949, and CE.
Contact Details
Related Glossary Terms
- centers
centers
Cone-shaped pins that support a workpiece by one or two ends during machining. The centers fit into holes drilled in the workpiece ends. Centers that turn with the workpiece are called “live” centers; those that do not are called “dead” centers.
- computer numerical control ( CNC)
computer numerical control ( CNC)
Microprocessor-based controller dedicated to a machine tool that permits the creation or modification of parts. Programmed numerical control activates the machine’s servos and spindle drives and controls the various machining operations. See DNC, direct numerical control; NC, numerical control.
- feed
feed
Rate of change of position of the tool as a whole, relative to the workpiece while cutting.
- flash
flash
Thin web or film of metal on a casting that occurs at die partings and around air vents and movable cores. This excess metal is due to necessary working and operating clearances in a die. Flash also is the excess material squeezed out of the cavity as a compression mold closes or as pressure is applied to the cavity.
- turning
turning
Workpiece is held in a chuck, mounted on a face plate or secured between centers and rotated while a cutting tool, normally a single-point tool, is fed into it along its periphery or across its end or face. Takes the form of straight turning (cutting along the periphery of the workpiece); taper turning (creating a taper); step turning (turning different-size diameters on the same work); chamfering (beveling an edge or shoulder); facing (cutting on an end); turning threads (usually external but can be internal); roughing (high-volume metal removal); and finishing (final light cuts). Performed on lathes, turning centers, chucking machines, automatic screw machines and similar machines.