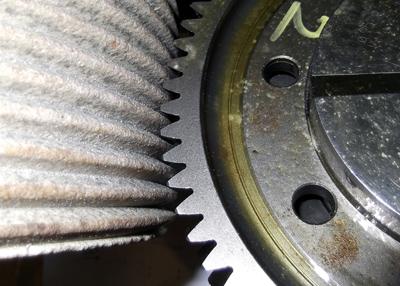
NUM has announced a high performance CNC solution for gear production machines that fully automates threaded wheel grinding. Incorporating unique high speed gear alignment technology that is believed to be an order of magnitude faster than comparable control schemes, the new CNC system dramatically reduces grinding machine threading-in times to accelerate throughput significantly. The comprehensive new solution is ideal for machine tool manufacturers seeking to improve the performance of their gear production machines, or to help companies expand their gear manufacturing range with threaded wheel grinders.
Based on NUM's new-generation Flexium+ CNC platform, the threaded wheel grinding solution joins the company's NUMgear suite of gear production software. Originally developed for gear hobbing applications, the capability of NUMgear has been continually extended and now includes solutions for a broad range of gear manufacturing processes, including shaping, grinding and honing, and is used by many of the world's foremost manufacturers of gear production machines.
NUM developed the latest addition to its NUMgear portfolio while helping an Asian gear manufacturing machine company to improve the performance of a prototype threaded wheel grinder. To improve grinding speed compared with current levels, NUM decided it needed to develop custom technology software. The principal aims were to reduce the time overhead of learning the teeth positions of the hardened gear prior to grinding, and improve the accuracy of the gear grinding process.
NUM's new product offers a comprehensive CNC solution for gear manufacturing machines. At the heart of the system is a high performance electronic gearbox that allows all master axes, such as the grinding, X, Y and Z axes, and the spindle (C axis) to be fully synchronized. As part of the development work on the new threaded wheel grinder, NUM has added a major new capability to the gearbox, which is now able to predict the acceleration of axes as well as their speed, in order to minimize synchronization time. Together with the Fast Gear Alignment, it forms part of the new NUMgear threaded wheel grinding application.
During gear production, "threading-in," the process of bringing the grinding wheel into contact with the gear blank, involves continuously adjusting the position of the grinding wheel relative to the work piece. A similar process is employed when bringing the machine's dressing wheel into contact with the grinding wheel. Using acoustic emission sensors to learn the sound signatures of a master gear and then using them to control positioning during production runs is a common technique for automating processes like this. However, the speed and accuracy of NUM's newly-developed Fast Gear Alignment Function eliminates the need for this entirely. As an example, aligning the grinding wheel with a 180mm diameter gear with 71 helical teeth takes just 0.5 of a second, without any need to acquire acoustic signatures or make manual adjustments.
A second aim of NUM's development required that the gear grinder CNC control should generate gears as accurately as possible. The latest machine from NUM's Asian customer produced gears with a tooth profile quality of DIN class 7. During the development process, NUM found that the diamond plated dressing wheel did not come up to specification. To overcome this problem without incurring major tooling costs, NUM decided to support their customer by helping to modify the technology programs. The positive results of this action far exceeded expectations, and NUM's solution can help a machine to consistently grind gear teeth profiles to within 3.5µm, comfortably achieving DIN class 3, an improvement of four class levels.
The latest gear grinding development is an example of one of the major principles underpinning NUM's business philosophy: a willingness to customize its CNC technology for machine makers. NUM supports this with a decentralized R&D structure which locates engineering staff around the world to allow it to work closely with machine builders. In this case, the new gear grinding solution was jointly developed by NUM's HQ in Switzerland and the company's technology centre in Chanzhou, China, which is close to many major gear manufacturing machine builders and is currently undergoing major expansion.
Contact Details
Related Glossary Terms
- computer numerical control ( CNC)
computer numerical control ( CNC)
Microprocessor-based controller dedicated to a machine tool that permits the creation or modification of parts. Programmed numerical control activates the machine’s servos and spindle drives and controls the various machining operations. See DNC, direct numerical control; NC, numerical control.
- dressing
dressing
Removal of undesirable materials from “loaded” grinding wheels using a single- or multi-point diamond or other tool. The process also exposes unused, sharp abrasive points. See loading; truing.
- grinding
grinding
Machining operation in which material is removed from the workpiece by a powered abrasive wheel, stone, belt, paste, sheet, compound, slurry, etc. Takes various forms: surface grinding (creates flat and/or squared surfaces); cylindrical grinding (for external cylindrical and tapered shapes, fillets, undercuts, etc.); centerless grinding; chamfering; thread and form grinding; tool and cutter grinding; offhand grinding; lapping and polishing (grinding with extremely fine grits to create ultrasmooth surfaces); honing; and disc grinding.
- grinding machine
grinding machine
Powers a grinding wheel or other abrasive tool for the purpose of removing metal and finishing workpieces to close tolerances. Provides smooth, square, parallel and accurate workpiece surfaces. When ultrasmooth surfaces and finishes on the order of microns are required, lapping and honing machines (precision grinders that run abrasives with extremely fine, uniform grits) are used. In its “finishing” role, the grinder is perhaps the most widely used machine tool. Various styles are available: bench and pedestal grinders for sharpening lathe bits and drills; surface grinders for producing square, parallel, smooth and accurate parts; cylindrical and centerless grinders; center-hole grinders; form grinders; facemill and endmill grinders; gear-cutting grinders; jig grinders; abrasive belt (backstand, swing-frame, belt-roll) grinders; tool and cutter grinders for sharpening and resharpening cutting tools; carbide grinders; hand-held die grinders; and abrasive cutoff saws.
- grinding wheel
grinding wheel
Wheel formed from abrasive material mixed in a suitable matrix. Takes a variety of shapes but falls into two basic categories: one that cuts on its periphery, as in reciprocating grinding, and one that cuts on its side or face, as in tool and cutter grinding.
- shaping
shaping
Using a shaper primarily to produce flat surfaces in horizontal, vertical or angular planes. It can also include the machining of curved surfaces, helixes, serrations and special work involving odd and irregular shapes. Often used for prototype or short-run manufacturing to eliminate the need for expensive special tooling or processes.