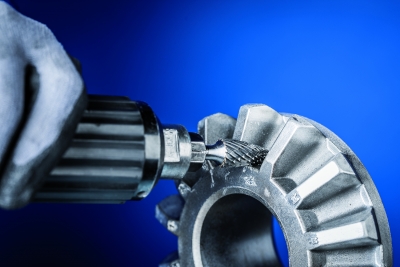
PFERD INC has introduced the OMNI cut, a versatile new carbide bur for high productivity on steel, cast steel, stainless steel (INOX) and cast iron, as well as nonferrous metals.
Offering increased removal rates over standard double-cut burs, including up to 30% greater removal on steel, the new OMNI cut range offers time savings and overall cost reductions, as well as less vibration and noise for improved operator safety and comfort.
Along with deburring, applications for the new PFERD OMNI cut bur include leveling, milling, work on weld seams and general surface work. It is compatible with straight grinders, flexible shaft drives, robots and CNC machines. Available in diameters of ¼-in. to 5/8-in., the new PFERD OMNI cut carbide burs perform best at peripheral speeds of 850-3,000 SFPM.
For convenience, the PFERD OMNI cut burs are available in either an eight-piece kit or five-piece kit in the most common shapes and dimensions.
Protected in a sturdy plastic box, the burs are secured at the shanks, facilitating the selection and withdrawal of the burs.
Contact Details
Related Glossary Terms
- bur
bur
Tool-condition problem characterized by the adhesion of small particles of workpiece material to the cutting edge during chip removal.
- computer numerical control ( CNC)
computer numerical control ( CNC)
Microprocessor-based controller dedicated to a machine tool that permits the creation or modification of parts. Programmed numerical control activates the machine’s servos and spindle drives and controls the various machining operations. See DNC, direct numerical control; NC, numerical control.
- gang cutting ( milling)
gang cutting ( milling)
Machining with several cutters mounted on a single arbor, generally for simultaneous cutting.
- milling
milling
Machining operation in which metal or other material is removed by applying power to a rotating cutter. In vertical milling, the cutting tool is mounted vertically on the spindle. In horizontal milling, the cutting tool is mounted horizontally, either directly on the spindle or on an arbor. Horizontal milling is further broken down into conventional milling, where the cutter rotates opposite the direction of feed, or “up” into the workpiece; and climb milling, where the cutter rotates in the direction of feed, or “down” into the workpiece. Milling operations include plane or surface milling, endmilling, facemilling, angle milling, form milling and profiling.