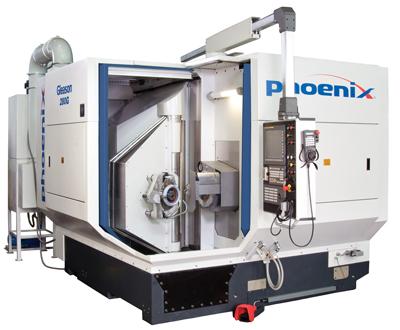
The new Phoenix 280G bevel gear grinding machine from Gleason Corp. reportedly establishes a new benchmark for bevel gear grinding for gears up to 280mm in diameter with a design that's reliable, highly productive and easy to operate and maintain. The new Phoenix 280G has a clean work chamber. There are no rails, wires, or pipes in the work chamber to collect swarf, keeping the chamber clean for low preventative maintenance.
In addition, the machine offers rapid set-up and all major set-up items can be completed without tools (toolless), including the grinding wheel, coolant header and workholding. The coolant header has small blocks that can easily be swapped out by hand, while the grinding wheel can be released hydraulically.
A well-designed work chamber ensures optimal swarf evacuation. The wheel dresser, for example,"telescopes" completely out of the work chamber to reduce the wiring/piping typically found there. The toolless, quick-change coolant header design features a laser guidance device that makes part-to-pipe alignment more efficient and repeatable.
High-speed direct-drive spindles combine with quick-change wheel, arbor and coolant header designs and automatic stock dividing (simultaneously with wheel dressing) to deliver fast floor-to-floor times.
The machine features the enhanced rigidity of the Phoenix Monolithic column, cast from advanced polymer composite material to achieve very high thermal stability and damping characteristics.
Equipped with powerful Fanuc 30i or Siemens 840D CNC and Gleason's user-friendly software empowers even less experienced operators; Phoenix design simplifies installation, integration with robots and gantry-type automation, and maintenance. The 280G's automatic stock divider, mounted in close proximity to the workspindle, helps ensure consistently high gear quality. The unit automatically determines the tooth slot position of the pre-finished gear to provide accurate and reliable stock division, helping eliminate operator errors.
Contact Details
Related Glossary Terms
- arbor
arbor
Shaft used for rotary support in machining applications. In grinding, the spindle for mounting the wheel; in milling and other cutting operations, the shaft for mounting the cutter.
- computer numerical control ( CNC)
computer numerical control ( CNC)
Microprocessor-based controller dedicated to a machine tool that permits the creation or modification of parts. Programmed numerical control activates the machine’s servos and spindle drives and controls the various machining operations. See DNC, direct numerical control; NC, numerical control.
- coolant
coolant
Fluid that reduces temperature buildup at the tool/workpiece interface during machining. Normally takes the form of a liquid such as soluble or chemical mixtures (semisynthetic, synthetic) but can be pressurized air or other gas. Because of water’s ability to absorb great quantities of heat, it is widely used as a coolant and vehicle for various cutting compounds, with the water-to-compound ratio varying with the machining task. See cutting fluid; semisynthetic cutting fluid; soluble-oil cutting fluid; synthetic cutting fluid.
- grinding
grinding
Machining operation in which material is removed from the workpiece by a powered abrasive wheel, stone, belt, paste, sheet, compound, slurry, etc. Takes various forms: surface grinding (creates flat and/or squared surfaces); cylindrical grinding (for external cylindrical and tapered shapes, fillets, undercuts, etc.); centerless grinding; chamfering; thread and form grinding; tool and cutter grinding; offhand grinding; lapping and polishing (grinding with extremely fine grits to create ultrasmooth surfaces); honing; and disc grinding.
- grinding machine
grinding machine
Powers a grinding wheel or other abrasive tool for the purpose of removing metal and finishing workpieces to close tolerances. Provides smooth, square, parallel and accurate workpiece surfaces. When ultrasmooth surfaces and finishes on the order of microns are required, lapping and honing machines (precision grinders that run abrasives with extremely fine, uniform grits) are used. In its “finishing” role, the grinder is perhaps the most widely used machine tool. Various styles are available: bench and pedestal grinders for sharpening lathe bits and drills; surface grinders for producing square, parallel, smooth and accurate parts; cylindrical and centerless grinders; center-hole grinders; form grinders; facemill and endmill grinders; gear-cutting grinders; jig grinders; abrasive belt (backstand, swing-frame, belt-roll) grinders; tool and cutter grinders for sharpening and resharpening cutting tools; carbide grinders; hand-held die grinders; and abrasive cutoff saws.
- grinding wheel
grinding wheel
Wheel formed from abrasive material mixed in a suitable matrix. Takes a variety of shapes but falls into two basic categories: one that cuts on its periphery, as in reciprocating grinding, and one that cuts on its side or face, as in tool and cutter grinding.
- swarf
swarf
Metal fines and grinding wheel particles generated during grinding.