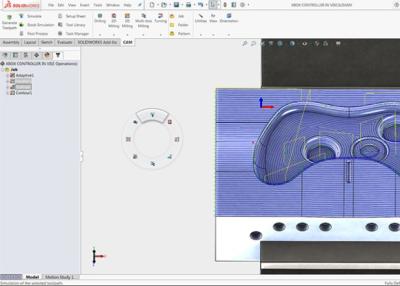
With the world of manufacturing undergoing major disruptions brought on by new market forces and technologies, Autodesk offers its portfolio of solutions for additive and subtractive manufacturing. The portfolio lets manufacturers take advantage of technology disruptions and improve competitiveness by creating higher quality products in less time with lower costs, according to the company.
The new solution brings together industry-leading products historically offered from Autodesk, Delcam, Netfabb, Pan Computing and Magestic Systems—including HSMWorks (pictured), Inventor HSM, Fusion 360, FeatureCAM, PowerMill, PartMaker (now included in FeatureCAM), PowerShape, PowerInspect and Netfabb—into one complete set of hybrid manufacturing solutions.
“Autodesk has long been a leader and innovator in 3D design, engineering and the technologies that expand the applications of industrial 3D printing, but we appreciate that no product is really complete until it’s realized through physical manufacture,” said Amar Hanspal, senior vice president of products at Autodesk. “We’ve also become a leader in technologies that expand the applications of industrial 3D printing. Now, we’re truly integrating the design, make and use phases of product development. This new set of solutions goes big on the ‘make’ component—equipping manufacturers with all the software they need to go from digital design to real-world product.”
The portfolio spans CAM, additive manufacturing, composites, robotics fabrication, factory layout, inspection and modeling. It enables customers to solve complex manufacturing challenges and seamlessly connect design to machining.
Within the portfolio offerings are cloud-connected capabilities designed to help users experience the benefits of a more cohesive manufacturing workflow and invest more time in product development. Cloud-capabilities give customers improved support for global manufacturing operations with universal access to software and data, and the cloud also enables fast and frequent software upgrades.
- Autodesk HSMWorks: A fully integrated CAM solution for SOLIDWORKS, allowing users to get up to speed and become productive within minutes using familiar tools and workflows.
- Autodesk Inventor HSM: Helps CNC programmers, designers and engineers rapidly produce machined parts designed in virtually any CAD system.
- Autodesk 2017 CAM Products: With offerings for a multitude of advanced manufacturing applications, these new products combine the heritage of industry leadership in CAM software from Delcam with Autodesk’s 3D design and manufacturing prowess. Solutions include FeatureCAM for automating CNC programming; PartMaker for precision part manufacturing with Swiss-type lathes; PowerMill for programming the most complex molds, dies and other components; PowerShape for preparing complex models for manufacture; and PowerInspect for inspection in every environment.
- Autodesk Netfabb: All the software you need to reduce costs, increase efficiency and improve part performance in additive manufacturing and 3D printing.
- Fusion 360: The centerpiece of Autodesk’s cloud-based product innovation platform, Fusion 360 combines CAD, CAM and CAE in a single package. It allows users to take their designs all the way to production with included 3D printing capabilities as well as HSM powered toolpath technology for 2 through 5 axis milling machines, turning centers and waterjets.
“Not only is the Netfabb bundle easy to use, it also does much of the heavy lifting in preparing models for 3D printing,” said Dan Ko, strategic initiatives lead at Shapeways. “The software streamlines the process of fixing common 3D print file problems and if we didn’t have it to automate a large portion of file preparation process, each build would be substantially more time consuming and labor intensive.”
“This new integrated portfolio from Autodesk brings together technology Autodesk has been growing and investing in across the full manufacturing spectrum,” said Hanspal. “This combination of solutions makes modular and scalable manufacturing solutions available to manufacturers of all sizes.”
Contact Details
Related Glossary Terms
- centers
centers
Cone-shaped pins that support a workpiece by one or two ends during machining. The centers fit into holes drilled in the workpiece ends. Centers that turn with the workpiece are called “live” centers; those that do not are called “dead” centers.
- composites
composites
Materials composed of different elements, with one element normally embedded in another, held together by a compatible binder.
- computer numerical control ( CNC)
computer numerical control ( CNC)
Microprocessor-based controller dedicated to a machine tool that permits the creation or modification of parts. Programmed numerical control activates the machine’s servos and spindle drives and controls the various machining operations. See DNC, direct numerical control; NC, numerical control.
- computer-aided design ( CAD)
computer-aided design ( CAD)
Product-design functions performed with the help of computers and special software.
- computer-aided engineering ( CAE)
computer-aided engineering ( CAE)
Engineering functions performed with the help of computers and special software. Includes functions such as determining a material’s ability to withstand stresses.
- computer-aided manufacturing ( CAM)
computer-aided manufacturing ( CAM)
Use of computers to control machining and manufacturing processes.
- gang cutting ( milling)
gang cutting ( milling)
Machining with several cutters mounted on a single arbor, generally for simultaneous cutting.
- milling
milling
Machining operation in which metal or other material is removed by applying power to a rotating cutter. In vertical milling, the cutting tool is mounted vertically on the spindle. In horizontal milling, the cutting tool is mounted horizontally, either directly on the spindle or on an arbor. Horizontal milling is further broken down into conventional milling, where the cutter rotates opposite the direction of feed, or “up” into the workpiece; and climb milling, where the cutter rotates in the direction of feed, or “down” into the workpiece. Milling operations include plane or surface milling, endmilling, facemilling, angle milling, form milling and profiling.
- robotics
robotics
Discipline involving self-actuating and self-operating devices. Robots frequently imitate human capabilities, including the ability to manipulate physical objects while evaluating and reacting appropriately to various stimuli. See industrial robot; robot.
- toolpath( cutter path)
toolpath( cutter path)
2-D or 3-D path generated by program code or a CAM system and followed by tool when machining a part.
- turning
turning
Workpiece is held in a chuck, mounted on a face plate or secured between centers and rotated while a cutting tool, normally a single-point tool, is fed into it along its periphery or across its end or face. Takes the form of straight turning (cutting along the periphery of the workpiece); taper turning (creating a taper); step turning (turning different-size diameters on the same work); chamfering (beveling an edge or shoulder); facing (cutting on an end); turning threads (usually external but can be internal); roughing (high-volume metal removal); and finishing (final light cuts). Performed on lathes, turning centers, chucking machines, automatic screw machines and similar machines.