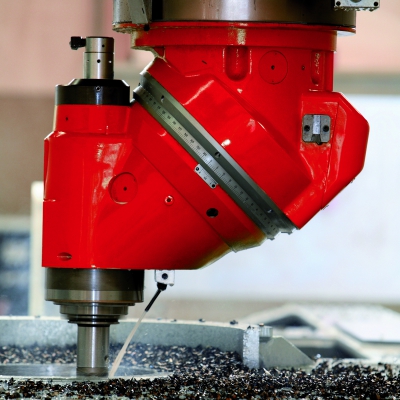
The large Powermill machining center from Mecof, part of EMCO Group, provides users precision, high dynamics, operational flexibility, and cost-effectiveness in a massive travelling gantry 5-axis milling center. Powermill with its moving bridge structure, permits loading of large, heavy workpieces on the stationary work table from overhead or from either end of the machine, making it ideal for handling aerospace components. Simple overall design makes possible easy positioning, set up, and clamping of huge workpieces of practically unlimited weight.
Users may specify travel in X/Y/Z: basically unlimited longitudinal, X-axis travel, and from 4,5,-6 and even 7 meters of Y- axis stroke with vertical ram stroke from 1.5 to 2.5 m plus several milling head options, automatic head exchange systems are available to create a suitable solution for a wide range of large parts. Double CNC platforms on each column with vertical adjustment, 120 pocket or more tool changer, laser checking of tool and workpiece to assure precise setup, high pressure tool cooling system, volumetric compensation and more are available. Axes feed rate is 30 m/min.
The mechanical universal milling head provides 6000 rpm, 38 kW (S1), 1000 Nm (S1), or users can choose a milling head with a straight head or with high-Speed motorized spindles, or indexed or full 5-axis contouring milling heads, to suite the material being machined and the geometric shape.
The Mecof machines are popular for aerospace machining as they are designed for the accurate production of assembly and lay-up tooling, long structural parts such as stringers, larger bulkheads and aircraft engine components such as discs and casings (through the application of rotary turning tables in front of or under the machine axes. Along with the EMCO turning machines, the company can offer a range of aerospace machining solutions from hydraulic components, actuators and even landing gear.
The box-in-box structure of Mecof machines assures machine structure rigidity, supporting high precision work over long axis travels. The massive structure combined with agility allows flexible, productive machining of many different types of parts.
Contact Details
Related Glossary Terms
- computer numerical control ( CNC)
computer numerical control ( CNC)
Microprocessor-based controller dedicated to a machine tool that permits the creation or modification of parts. Programmed numerical control activates the machine’s servos and spindle drives and controls the various machining operations. See DNC, direct numerical control; NC, numerical control.
- feed
feed
Rate of change of position of the tool as a whole, relative to the workpiece while cutting.
- gang cutting ( milling)
gang cutting ( milling)
Machining with several cutters mounted on a single arbor, generally for simultaneous cutting.
- machining center
machining center
CNC machine tool capable of drilling, reaming, tapping, milling and boring. Normally comes with an automatic toolchanger. See automatic toolchanger.
- milling
milling
Machining operation in which metal or other material is removed by applying power to a rotating cutter. In vertical milling, the cutting tool is mounted vertically on the spindle. In horizontal milling, the cutting tool is mounted horizontally, either directly on the spindle or on an arbor. Horizontal milling is further broken down into conventional milling, where the cutter rotates opposite the direction of feed, or “up” into the workpiece; and climb milling, where the cutter rotates in the direction of feed, or “down” into the workpiece. Milling operations include plane or surface milling, endmilling, facemilling, angle milling, form milling and profiling.
- turning
turning
Workpiece is held in a chuck, mounted on a face plate or secured between centers and rotated while a cutting tool, normally a single-point tool, is fed into it along its periphery or across its end or face. Takes the form of straight turning (cutting along the periphery of the workpiece); taper turning (creating a taper); step turning (turning different-size diameters on the same work); chamfering (beveling an edge or shoulder); facing (cutting on an end); turning threads (usually external but can be internal); roughing (high-volume metal removal); and finishing (final light cuts). Performed on lathes, turning centers, chucking machines, automatic screw machines and similar machines.