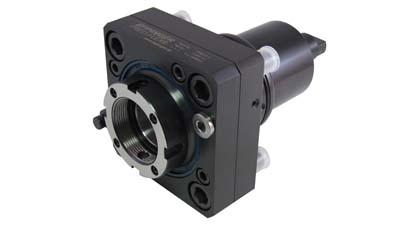
Several machine tool manufacturers, including Nakamura, are transitioning over to bolt-on style turrets for their horizontal lathes because these solutions are more robust and easier to use than VDI designs. In response, EXSYS Tool Inc. is introducing a new bolt-on mounting PRECI-FLEX Modular Tooling System for most Nakamura machines equipped with bolt-on style turrets, including the TW-10, WT-20 II M-MY, WT-150, WT-250, TW-20, WT-300, Super NTX, WTW-150, Super NTJ and many more.
EXSYS/EPPINGER manufactures its tool holders to meet very rigid construction standards for effectively handling deep feeds at high rates of speed. Because these tool holders feature a double tapered roller bearing configuration, they are able to handle much greater loads than tool holders with conventional ball bearings.
According to Scott Leitch, sales manager for EXSYS, the stringent engineering practices the company uses in the development of its tool holders really pays off out in the field. "Our quality construction standards and better bearings enable our customers to achieve longer tool life and a better return on their overall investment."
Able to accommodate most CNC turning centers, EXSYS/EPPINGER PRECI-FLEX is the first tooling system on the market with a single base holder and multiple tooling adapters that utilizes the ER collet pocket, making turning center tooling changeovers quick, accurate and cost-effective. Furthermore, the system's compact design ensures maximum torque transmission and rigidity, resulting in increased machining accuracy and improved productivity.
Available in a range of sizes, PRECI-FLEX provides unsurpassed repeatability, with every toolholder offering repeatability within fiveµm. The system also virtually eliminates machine downtime, and allows tooling adapters to be interchanged between fixed and rotary base holders for fast, economical machining.
Contact Details
Related Glossary Terms
- centers
centers
Cone-shaped pins that support a workpiece by one or two ends during machining. The centers fit into holes drilled in the workpiece ends. Centers that turn with the workpiece are called “live” centers; those that do not are called “dead” centers.
- collet
collet
Flexible-sided device that secures a tool or workpiece. Similar in function to a chuck, but can accommodate only a narrow size range. Typically provides greater gripping force and precision than a chuck. See chuck.
- computer numerical control ( CNC)
computer numerical control ( CNC)
Microprocessor-based controller dedicated to a machine tool that permits the creation or modification of parts. Programmed numerical control activates the machine’s servos and spindle drives and controls the various machining operations. See DNC, direct numerical control; NC, numerical control.
- modular tooling
modular tooling
1. Tooling system comprised of standardized tools and toolholders. 2. Devices that allow rapid mounting and replacement of tools. Commonly used with carousel toolchangers and other computerized machining operations. See toolchanger; toolholder.
- toolholder
toolholder
Secures a cutting tool during a machining operation. Basic types include block, cartridge, chuck, collet, fixed, modular, quick-change and rotating.
- turning
turning
Workpiece is held in a chuck, mounted on a face plate or secured between centers and rotated while a cutting tool, normally a single-point tool, is fed into it along its periphery or across its end or face. Takes the form of straight turning (cutting along the periphery of the workpiece); taper turning (creating a taper); step turning (turning different-size diameters on the same work); chamfering (beveling an edge or shoulder); facing (cutting on an end); turning threads (usually external but can be internal); roughing (high-volume metal removal); and finishing (final light cuts). Performed on lathes, turning centers, chucking machines, automatic screw machines and similar machines.