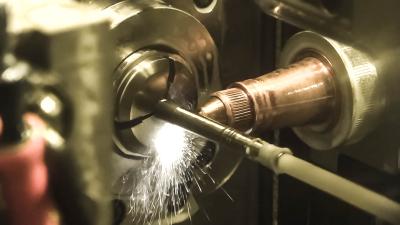
Tsugami LaserSwiss offers a new LaserSwiss CNC machine tool. The new LaserSwiss is a next-generation Precision Tsugami B0125-III. The 12 mm, 5-axis Swiss-style CNC lathe features a fully integrated SPI laser cutting system.
“We don’t know of anyone else offering a 12 mm machine that combines Swiss turning and laser cutting within a fully integrated operating platform,” Tsugami LaserSwiss Business Development Director Dan Walker said.
All laser operations are programmed and driven from the machine’s FANUC 0i-TF control and the laser’s power, pulse width, frequency, lens focus and nozzle standoff are on-the-fly adjustable. The machine is equipped with a gas box capable of switching between two assist gases, which are typically nitrogen, oxygen and argon.
The machine has 10 tool positions in addition to the laser and it is convertible, meaning it can be run as a traditional Swiss style lathe using a guide bushing or operated with an optional chucker kit, which can be installed in minutes.
“This machine offers tremendous flexibility,” Walker said, “but it’s not overly complicated. It’s a straightforward, simple machine that’s very easy to program and use.” Of the nine Tsugami LaserSwiss machines on the market, the B0125 is the most affordable, he added, and its small footprint of roughly 20 square feet makes it suitable for shops with limited floor space.
Customers can order Tsugami LaserSwiss machines with laser watts ranging from 200W to 500W, depending on their preference and model selection. The SPI laser units are rated to last 500,000 hours without service. “It’s like having a very fast, very precise cutting tool that never gets dull,” Walker said.
Contact Details
Related Glossary Terms
- bushing
bushing
Cylindrical sleeve, typically made from high-grade tool steel, inserted into a jig fixture to guide cutting tools. There are three main types: renewable, used in liners that in turn are installed in the jig; press-fit, installed directly in the jig for short production runs; and liner (or master), installed permanently in a jig to receive renewable bushing.
- computer numerical control ( CNC)
computer numerical control ( CNC)
Microprocessor-based controller dedicated to a machine tool that permits the creation or modification of parts. Programmed numerical control activates the machine’s servos and spindle drives and controls the various machining operations. See DNC, direct numerical control; NC, numerical control.
- lathe
lathe
Turning machine capable of sawing, milling, grinding, gear-cutting, drilling, reaming, boring, threading, facing, chamfering, grooving, knurling, spinning, parting, necking, taper-cutting, and cam- and eccentric-cutting, as well as step- and straight-turning. Comes in a variety of forms, ranging from manual to semiautomatic to fully automatic, with major types being engine lathes, turning and contouring lathes, turret lathes and numerical-control lathes. The engine lathe consists of a headstock and spindle, tailstock, bed, carriage (complete with apron) and cross slides. Features include gear- (speed) and feed-selector levers, toolpost, compound rest, lead screw and reversing lead screw, threading dial and rapid-traverse lever. Special lathe types include through-the-spindle, camshaft and crankshaft, brake drum and rotor, spinning and gun-barrel machines. Toolroom and bench lathes are used for precision work; the former for tool-and-die work and similar tasks, the latter for small workpieces (instruments, watches), normally without a power feed. Models are typically designated according to their “swing,” or the largest-diameter workpiece that can be rotated; bed length, or the distance between centers; and horsepower generated. See turning machine.
- turning
turning
Workpiece is held in a chuck, mounted on a face plate or secured between centers and rotated while a cutting tool, normally a single-point tool, is fed into it along its periphery or across its end or face. Takes the form of straight turning (cutting along the periphery of the workpiece); taper turning (creating a taper); step turning (turning different-size diameters on the same work); chamfering (beveling an edge or shoulder); facing (cutting on an end); turning threads (usually external but can be internal); roughing (high-volume metal removal); and finishing (final light cuts). Performed on lathes, turning centers, chucking machines, automatic screw machines and similar machines.