Contact Details
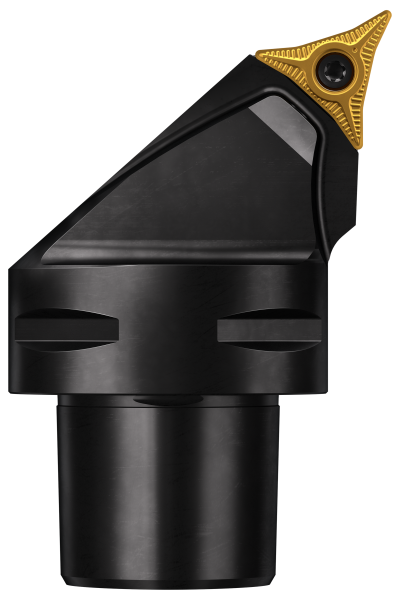
Sandvik Coromant says it has unveiled a new turning concept that offers improved machining flexibility and the potential for significant productivity gains. The company’s PrimeTurning methodology and supporting tools provide manufacturers, particularly in aerospace and automotive sectors, with a true "all directional turning" solution.
Unlike conventional turning operations, which have remained largely unchanged for decades, PrimeTurning allows machine shops to complete longitudinal (forward and back), facing and profiling operations with a single tool. The methodology is based on the tool entering the component at the chuck and removing material as it travels towards the end of the component. This allows for the application of a small entering angle, higher lead angle and the possibility of machining with higher cutting parameters. Furthermore, conventional turning (from part-end to chuck) can be performed using the same tools.
Sandvik Coromant believes that some applications could see productivity increases in excess of 50 percent through the deployment of PrimeTurning rather than conventional techniques. Some of these improvements are due to the small entering angle and higher lead angle, which creates thinner, wider chips that spread the load and heat away from the nose radius. The result is both increased cutting data and extended tool life. In addition, as cutting is performed in the direction moving away from the shoulder, there is no danger of chip jamming (a common and unwanted effect of conventional longitudinal turning). Higher machine utilization due to reduced setup time and fewer production stops for tool changes also enhances overall productivity.
PrimeTurning will be particularly beneficial to manufacturing industries such as aerospace and automotive where there is a need to perform external turning operations in big batch productions or where multiple set-ups and tool changes are often required.
“Experienced operators know that a small entering angle allows for increased feed rates,” said Håkan Ericksson, Global Product Specialist at Sandvik Coromant. “However, in conventional turning they are restricted to using entering angles of around 90° to reach the shoulder and avoid the long, curved chips that a small entering angle characteristically delivers. PrimeTurning solves these problems by combining a perfect reach at the shoulder and the application of 25° to 30° entering angles with excellent chip control and maintained tolerances. This innovation presents countless possibilities to perform turning operations in much more efficient and productive ways. It’s not just a new tool, but a totally new way of turning.”
PrimeTurning is initially supported by the introduction of two dedicated CoroTurn Prime turning tools and the PrimeTurning code generator, which supplies optimized programming codes and techniques. CoroTurn Prime inserts have three edges/corners; one for longitudinal turning, one for facing and one for profiling, thus delivering efficient edge utilisation and longer tool life.
Two unique and dedicated inserts are offered: CoroTurn Prime A-type features three 35° corners and is for light roughing, finishing and profiling, while CoroTurn Prime B-type with its ultrastrong corners is specifically for rough machining. Suitable for ISO P (steel), S (heat-resistant superalloys and titanium) and M (stainless steel) category materials, nine CoroTurn Prime A-type and six CoroTurn Prime B-type inserts are currently available, with expansion to other materials envisioned for the future. The inserts are supported by 52 variants of toolholder, including Coromant Capto, CoroTurn QS and shanks.
The PrimeTurning code generator not only ensures maximum output but also process security with suitably adjusted feed rate and entry radius parameters. It creates ISO codes that are compatible with various CNC systems.
Related Glossary Terms
- chuck
chuck
Workholding device that affixes to a mill, lathe or drill-press spindle. It holds a tool or workpiece by one end, allowing it to be rotated. May also be fitted to the machine table to hold a workpiece. Two or more adjustable jaws actually hold the tool or part. May be actuated manually, pneumatically, hydraulically or electrically. See collet.
- computer numerical control ( CNC)
computer numerical control ( CNC)
Microprocessor-based controller dedicated to a machine tool that permits the creation or modification of parts. Programmed numerical control activates the machine’s servos and spindle drives and controls the various machining operations. See DNC, direct numerical control; NC, numerical control.
- feed
feed
Rate of change of position of the tool as a whole, relative to the workpiece while cutting.
- lead angle
lead angle
Angle between the side-cutting edge and the projected side of the tool shank or holder, which leads the cutting tool into the workpiece.
- profiling
profiling
Machining vertical edges of workpieces having irregular contours; normally performed with an endmill in a vertical spindle on a milling machine or with a profiler, following a pattern. See mill, milling machine.
- superalloys
superalloys
Tough, difficult-to-machine alloys; includes Hastelloy, Inconel and Monel. Many are nickel-base metals.
- toolholder
toolholder
Secures a cutting tool during a machining operation. Basic types include block, cartridge, chuck, collet, fixed, modular, quick-change and rotating.
- turning
turning
Workpiece is held in a chuck, mounted on a face plate or secured between centers and rotated while a cutting tool, normally a single-point tool, is fed into it along its periphery or across its end or face. Takes the form of straight turning (cutting along the periphery of the workpiece); taper turning (creating a taper); step turning (turning different-size diameters on the same work); chamfering (beveling an edge or shoulder); facing (cutting on an end); turning threads (usually external but can be internal); roughing (high-volume metal removal); and finishing (final light cuts). Performed on lathes, turning centers, chucking machines, automatic screw machines and similar machines.