Contact Details
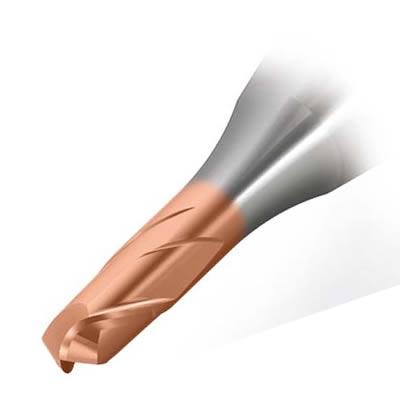
Walter USA LLC has introduced the Walter Prototyp Proto-max Ultra ball-nose end mill, specially engineered for efficient machining of hard materials. The latest generation of the company's Proto-max solid-carbide milling tools offers enhanced machining performance and tool life, even when machining hard ISO-H materials.
The new end mills come in two different diameter ranges: the standard versions from 3-12mm diameter and the mini versions for small to extremely small contours, ranging from 0.1-2.5mm. For the smaller diameter range, the Proto-max Ultra's reduced neck and its reach of up to 10xD are beneficial for the machining of deep cavities. This results in excellent concentricity properties, which are essential at the high speeds achieved by small tool diameters.
Primary applications for this new line of solid carbide end mills are hardened materials up to 70 HRC in die and moldmaking, as well as similar operations in general machining and heavy construction applications. Key features include a new TiAlSiN-based coating, known as TAS for short. This coating is highly heat-resistant, leading to longer tool life when machining hard materials. Added to this is an optimized geometry for stabilizing the cutting edges.
All diameters, even those in the mini versions, have two cutting edges and a helix angle of 30 degrees. When combined, these features enable the Proto-max Ultra to be utilized for semiroughing and roughing, as well as for semifinishing and fine finishing.
Related Glossary Terms
- gang cutting ( milling)
gang cutting ( milling)
Machining with several cutters mounted on a single arbor, generally for simultaneous cutting.
- helix angle
helix angle
Angle that the tool’s leading edge makes with the plane of its centerline.
- milling
milling
Machining operation in which metal or other material is removed by applying power to a rotating cutter. In vertical milling, the cutting tool is mounted vertically on the spindle. In horizontal milling, the cutting tool is mounted horizontally, either directly on the spindle or on an arbor. Horizontal milling is further broken down into conventional milling, where the cutter rotates opposite the direction of feed, or “up” into the workpiece; and climb milling, where the cutter rotates in the direction of feed, or “down” into the workpiece. Milling operations include plane or surface milling, endmilling, facemilling, angle milling, form milling and profiling.
- milling machine ( mill)
milling machine ( mill)
Runs endmills and arbor-mounted milling cutters. Features include a head with a spindle that drives the cutters; a column, knee and table that provide motion in the three Cartesian axes; and a base that supports the components and houses the cutting-fluid pump and reservoir. The work is mounted on the table and fed into the rotating cutter or endmill to accomplish the milling steps; vertical milling machines also feed endmills into the work by means of a spindle-mounted quill. Models range from small manual machines to big bed-type and duplex mills. All take one of three basic forms: vertical, horizontal or convertible horizontal/vertical. Vertical machines may be knee-type (the table is mounted on a knee that can be elevated) or bed-type (the table is securely supported and only moves horizontally). In general, horizontal machines are bigger and more powerful, while vertical machines are lighter but more versatile and easier to set up and operate.