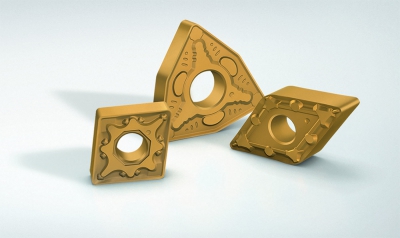
Walter has introduced two new insert grades in its Perform Line of turning tools, the WPV10 and WPV20. These versatile, cost-effective inserts are suitable for users whose machines are limited in cutting parameters due to their stability and performance, and who need a versatile insert that can handle different materials, as well as for those who machine small or medium batch sizes.
The lower price-point inserts are also beneficial to users who have difficulties measuring the tool life of an insert and who change inserts at set intervals, for example at the beginning of each shift.
Both grades WPV10 and WPV20, have CVD coating and gold color for easy wear detection. These grades are available in three new geometries: FV5 (finishing), MV5 (medium machining), and RV5 (roughing). Primary application for these new Walter Perform turning inserts is steels (ISO P), with secondary applications in stainless steels (ISO M) and cast iron (ISO K). In field testing, the Walter Perform turning inserts demonstrated superior process reliability with good chip control, and tool-life increases of up to 100 percent when compared to other similar inserts.
Contact Details
Related Glossary Terms
- chemical vapor deposition ( CVD)
chemical vapor deposition ( CVD)
High-temperature (1,000° C or higher), atmosphere-controlled process in which a chemical reaction is induced for the purpose of depositing a coating 2µm to 12µm thick on a tool’s surface. See coated tools; PVD, physical vapor deposition.
- stainless steels
stainless steels
Stainless steels possess high strength, heat resistance, excellent workability and erosion resistance. Four general classes have been developed to cover a range of mechanical and physical properties for particular applications. The four classes are: the austenitic types of the chromium-nickel-manganese 200 series and the chromium-nickel 300 series; the martensitic types of the chromium, hardenable 400 series; the chromium, nonhardenable 400-series ferritic types; and the precipitation-hardening type of chromium-nickel alloys with additional elements that are hardenable by solution treating and aging.
- turning
turning
Workpiece is held in a chuck, mounted on a face plate or secured between centers and rotated while a cutting tool, normally a single-point tool, is fed into it along its periphery or across its end or face. Takes the form of straight turning (cutting along the periphery of the workpiece); taper turning (creating a taper); step turning (turning different-size diameters on the same work); chamfering (beveling an edge or shoulder); facing (cutting on an end); turning threads (usually external but can be internal); roughing (high-volume metal removal); and finishing (final light cuts). Performed on lathes, turning centers, chucking machines, automatic screw machines and similar machines.