Contact Details
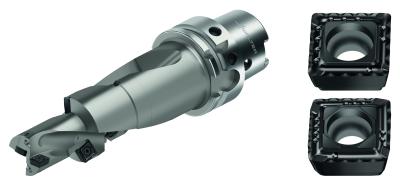
Walter has introduced the PVD drilling WNN15 grade for indexable insert drills. The extremely reliable, low-adhesion grade WNN15 is now included in the range for Walter indexable insert drills. This grade is primarily designed for drilling in tough ISO N materials such as wrought aluminum alloys or cast aluminum alloys. Primary areas of application are in aerospace, automotive and general machining when weight reduction is key.
The grade provides for reliable chip removal thanks to its extremely smooth surface with a reduced tendency towards adhesion and build-up on the cutting edge to increase process reliability and wear resistance.
The WNN15 grade delivers outstanding process reliability and long tool life, even at extremely high cutting speeds. This means that it makes indexable insert drilling more cost-effective than comparable PCD tools with immediate effect. The indexable insert drills offer the advantage of multiple indexing which means that the tool can be used again immediately and with comparably lower costs and less time required. Worn indexable inserts can be replaced quickly and easily.
The Walter drilling grade WNN15 features a hard substrate on the indexable inserts, which promotes high cutting-edge stability. The PVD coating created using the HiPIMS process creates a particularly smooth, dense surface – leading to a rake face surface that performs better that polished carbide surface. Chip removal is smooth and there is hardly any build-up on the cutting edge. Due to its high wear resistance, drilling processes using the Walter grade WNN15 are extremely reliable. An increase in the tool life of up to 200% can be achieved, depending on the application, compared to conventional drilling grades. The WNN15 drilling grades are now available for most of the indexable insert drills in Walter portfolio. These include: D4120 (sizes 1-8), D3120(sizes 1-7), and B3212.DF--B3214-DF (0.394-0.709 in. (10-18 mm).
Related Glossary Terms
- alloys
alloys
Substances having metallic properties and being composed of two or more chemical elements of which at least one is a metal.
- aluminum alloys
aluminum alloys
Aluminum containing specified quantities of alloying elements added to obtain the necessary mechanical and physical properties. Aluminum alloys are divided into two categories: wrought compositions and casting compositions. Some compositions may contain up to 10 alloying elements, but only one or two are the main alloying elements, such as copper, manganese, silicon, magnesium, zinc or tin.
- indexable insert
indexable insert
Replaceable tool that clamps into a tool body, drill, mill or other cutter body designed to accommodate inserts. Most inserts are made of cemented carbide. Often they are coated with a hard material. Other insert materials are ceramic, cermet, polycrystalline cubic boron nitride and polycrystalline diamond. The insert is used until dull, then indexed, or turned, to expose a fresh cutting edge. When the entire insert is dull, it is usually discarded. Some inserts can be resharpened.
- physical vapor deposition ( PVD)
physical vapor deposition ( PVD)
Tool-coating process performed at low temperature (500° C), compared to chemical vapor deposition (1,000° C). Employs electric field to generate necessary heat for depositing coating on a tool’s surface. See CVD, chemical vapor deposition.
- polycrystalline diamond ( PCD)
polycrystalline diamond ( PCD)
Cutting tool material consisting of natural or synthetic diamond crystals bonded together under high pressure at elevated temperatures. PCD is available as a tip brazed to a carbide insert carrier. Used for machining nonferrous alloys and nonmetallic materials at high cutting speeds.
- rake
rake
Angle of inclination between the face of the cutting tool and the workpiece. If the face of the tool lies in a plane through the axis of the workpiece, the tool is said to have a neutral, or zero, rake. If the inclination of the tool face makes the cutting edge more acute than when the rake angle is zero, the rake is positive. If the inclination of the tool face makes the cutting edge less acute or more blunt than when the rake angle is zero, the rake is negative.
- wear resistance
wear resistance
Ability of the tool to withstand stresses that cause it to wear during cutting; an attribute linked to alloy composition, base material, thermal conditions, type of tooling and operation and other variables.