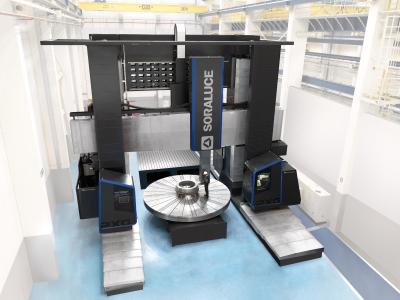
The new SORALUCE PXG-W was presented at the company's production plant from Jan. 30 to 3 Feb. 3. In the course of the week, numerous customers were able to visit the assembly and testing facilities and technology center to see at first hand the technical characteristics of the machine and the advantages and benefits that it can bring them.
Machining large components calls for specific skills and machines capable of guaranteeing the maximum precision, productivity and reliability required to be competitive on the market.
Nowadays, machines for components of this type need to be capable of handling extremely complex machining operations. The machine needs to meet multitasking and versatility requirements so as to maximise productive time and minimise set-up time. In that context the new SORALUCE PXG-W gantry-type multitasking milling machine reduces the number of clamps required and minimizes cycle times and potential errors. It can also work with centesimal tolerances on large workpieces, even those that weigh hundreds of tons.
The new PXG-W model is the culmination of SORALUCE's strategy in the large-sized machine-tool segment. It marks the next step in the path begun in 2009, when SORALUCE joined the Hiperion project, promoted by various manufacturers in the Basque Country and funded via the Basque Government's Etorgai programme.
The SORALUCE PXG-W is characterised by its high capabilities. It has a working volume of 1000 m3 and weighs 500 tons. The dimensions of the model presented are as follows: 19m in length, 7.25m clearance between columns and 7.3m in height. Height is also configurable thanks to the 5m vertical travel of the crossbeam. The SORALUCE PXG-W belongs to the range of large-sized gantry milling machines and completes the top end of the company's PM, PMG and PRG gantry-type machine range.
This highly versatile model is designed to meet the machining requirements for a range of highly demanding parts used in the construction of machinery for the energy industry, the machining of marine and CHP motors and general machining of large workpieces.
The SORALUCE PXG-W is a completely versatile multitasking solution designed to maximise productivity through its ability to handle milling and turning operations on the same machine. It provides the highest possible return in machining large workpieces with a high degree of technical complexity, and makes it possible to machine a range of shapes and sizes. Its distinguishing feature is its ability to handle different machining processes including turning, milling, boring, drilling and threading with efficiency and precision. To that end, it has several milling and turning heads with automatic tool changing.
The work area is split into two sub-areas. The surface of the main sub-area is for machining prismatic parts. It is equipped with 12x6m floor plates, and has a load capacity of 25 t/m2. The second sub-area comprises a turning table with a hydrostatic mounting, featuring a 6m diameter table with a load capacity of 150 tons. The turning head has a power rating of 200 kW and a maximum speed of 50 rpm. This enables it to handle large-scale roughing out operations on large-sized parts from various sectors.
The SORALUCE PXG is fitted with a latest-generation Siemens 840D SL CNC, which enables both milling and turning operations to be handled on the same machine, thus reducing the number of setups and avoiding difficult transportation and relocation operations when large components are to be machined. It has two operator’s platforms, each with its own control panel, thus enabling the operator to take up the best position for each operation.
The core goal in the design of the SORALUCE PXG-W was to ensure that customers can obtain the maximum precision. The machine therefore features the latest technologies and solutions which are innovative in the large machine segment.
It has been provided with linear guides on the X, Y and Z axes, which provide certain advantages over conventional solutions such as hydrostatic guides. Linear guiding system avoids the thermal gradients caused by the flow of oil through the structure of the machine, ensuring better geometrical stability and substantially reducing the maintenance required.
The general performance of the machine has been analysed carefully by SORALUCE's innovation & design teams, which have run multiple simulations to correctly characterise the different deformations caused by the displacement of the moving parts of the system. In the light of the results of these analyses, SORALUCE has created and applied a number of devices that largely offset the deformations caused by the weight of those moving parts. One of these devices is the innovative Vertical Ram Balance system (VRB), patent pending. The system, which consists of a CNC controlled electromechanical system, patent pending, offsets the rolling caused by the torsion of the cross beam and the differential bending of the columns when the ram travels along the cross (Y) axis of the machine. The system ensures maximum precision in terms of the perpendicularity of the X and Y axes, whatever the working position.
The machine also has a new thermal monitoring system that checks for changes over time in all its structural components via a function built into the CNC. It also has the latest thermal compensation algorithms developed by SORALUCE.
The turning table is fitted with sensors so that a function built into the CNC can be used to help the operator to rebalance the weight of parts with asymmetric geometries.
The structure of the machine is built entirely of cast iron, a material that is much appreciated for its good intrinsic qualities as regards stability and internal damping capability. Of course, the machine also has all the technology developed by SORALUCE to improve its dynamic performance and help increase stability during machining, according to the company.
This includes the DAS (Dynamic Active Stabiliser), developed exclusively by SORALUCE, which has won several international awards and is protected by a European patent. This system enables a damping effect to be actively incorporated into the structure of the machine, thus increasing its cutting capability by up to 300 percent and reducing the risk of chatter or instability during machining.
The SORALUCE PXG-W also has other smart systems to help maximise its productivity, such as adaptive control, which continuously adjusts the machine's feed rate in line with power consumption to adapt it to tool capacity and process circumstances. It also features the SSV system, which helps avoid the regenerative effect caused by certain chatter conditions during the process. This is particularly effective during large-scale boring and turning operations.
The equipment built into the SORALUCE PXG covers a wide range of circumstances. It has seven milling heads for different geometries and power settings, which in some units can be as high as 81 kW. This variety makes the machine highly flexible and enables it to machine a range of different parts however difficult and inaccessible the areas to be machined may be. All heads are manufactured by SORALUCE.
The machine is also fitted with a magazine with 3 turning accessories which enable it to work with automatic or manual Capto C8 and prismatic tool clamping. Tool changes can be made automatically over the whole 5m travel. In this case the capacity of the on-board magazine is 180 tools.
In spite of its complexity, the machine is easy to operate thanks to the kinematics on the heads and accessories integrated into the CNC. This means that the geometries of these elements can be compensated for and the working axes can be oriented automatically, thus facilitating and improving the operator handling experience.
The SORALUCE PXG-W machine also includes technological features that fall within the concept of Industry 4.0: specifically a full monitoring package based on cloud computing.
It incorporates utilities such as a real-time machine status display with relevant information on the status of the ongoing machining program, email messaging in case of problems, the production of reports on sensitive issues for users such as production and processes, such as energy consumption and performance during machining cycles, and diagnostics for key signals for the maintenance of the equipment. This is all done via secure connections routed through a PC or mobile device (smartphone or tablet) by accessing a single website online.
Contact Details
Related Glossary Terms
- boring
boring
Enlarging a hole that already has been drilled or cored. Generally, it is an operation of truing the previously drilled hole with a single-point, lathe-type tool. Boring is essentially internal turning, in that usually a single-point cutting tool forms the internal shape. Some tools are available with two cutting edges to balance cutting forces.
- chatter
chatter
Condition of vibration involving the machine, workpiece and cutting tool. Once this condition arises, it is often self-sustaining until the problem is corrected. Chatter can be identified when lines or grooves appear at regular intervals in the workpiece. These lines or grooves are caused by the teeth of the cutter as they vibrate in and out of the workpiece and their spacing depends on the frequency of vibration.
- clearance
clearance
Space provided behind a tool’s land or relief to prevent rubbing and subsequent premature deterioration of the tool. See land; relief.
- computer numerical control ( CNC)
computer numerical control ( CNC)
Microprocessor-based controller dedicated to a machine tool that permits the creation or modification of parts. Programmed numerical control activates the machine’s servos and spindle drives and controls the various machining operations. See DNC, direct numerical control; NC, numerical control.
- feed
feed
Rate of change of position of the tool as a whole, relative to the workpiece while cutting.
- gang cutting ( milling)
gang cutting ( milling)
Machining with several cutters mounted on a single arbor, generally for simultaneous cutting.
- milling
milling
Machining operation in which metal or other material is removed by applying power to a rotating cutter. In vertical milling, the cutting tool is mounted vertically on the spindle. In horizontal milling, the cutting tool is mounted horizontally, either directly on the spindle or on an arbor. Horizontal milling is further broken down into conventional milling, where the cutter rotates opposite the direction of feed, or “up” into the workpiece; and climb milling, where the cutter rotates in the direction of feed, or “down” into the workpiece. Milling operations include plane or surface milling, endmilling, facemilling, angle milling, form milling and profiling.
- milling machine ( mill)
milling machine ( mill)
Runs endmills and arbor-mounted milling cutters. Features include a head with a spindle that drives the cutters; a column, knee and table that provide motion in the three Cartesian axes; and a base that supports the components and houses the cutting-fluid pump and reservoir. The work is mounted on the table and fed into the rotating cutter or endmill to accomplish the milling steps; vertical milling machines also feed endmills into the work by means of a spindle-mounted quill. Models range from small manual machines to big bed-type and duplex mills. All take one of three basic forms: vertical, horizontal or convertible horizontal/vertical. Vertical machines may be knee-type (the table is mounted on a knee that can be elevated) or bed-type (the table is securely supported and only moves horizontally). In general, horizontal machines are bigger and more powerful, while vertical machines are lighter but more versatile and easier to set up and operate.
- threading
threading
Process of both external (e.g., thread milling) and internal (e.g., tapping, thread milling) cutting, turning and rolling of threads into particular material. Standardized specifications are available to determine the desired results of the threading process. Numerous thread-series designations are written for specific applications. Threading often is performed on a lathe. Specifications such as thread height are critical in determining the strength of the threads. The material used is taken into consideration in determining the expected results of any particular application for that threaded piece. In external threading, a calculated depth is required as well as a particular angle to the cut. To perform internal threading, the exact diameter to bore the hole is critical before threading. The threads are distinguished from one another by the amount of tolerance and/or allowance that is specified. See turning.
- turning
turning
Workpiece is held in a chuck, mounted on a face plate or secured between centers and rotated while a cutting tool, normally a single-point tool, is fed into it along its periphery or across its end or face. Takes the form of straight turning (cutting along the periphery of the workpiece); taper turning (creating a taper); step turning (turning different-size diameters on the same work); chamfering (beveling an edge or shoulder); facing (cutting on an end); turning threads (usually external but can be internal); roughing (high-volume metal removal); and finishing (final light cuts). Performed on lathes, turning centers, chucking machines, automatic screw machines and similar machines.