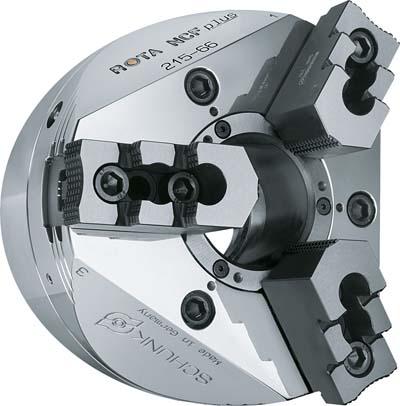
SCHUNK introduces a new line of power chucks, the ROTA NCK-plus. In addition to features like a large through hole, an improved lubrication system, and high clamping repeatability, the ROTA NCK-plus is a direct replacement of nearly all OEM chucks. With tapered clearance designed into the chuck body, additional tooling clearance as well as increased spindle bearing life due to lighter weight can be realized. The long precision piston guide and support guarantee less wear, a high level of continuous clamping accuracy, and long life. Combined a warranty of 2 years, this power chuck represents an alternative as a replacement lathe chuck. The jaw interfaces are 1.5mm x 60 degrees and 1⁄16 x 90 degrees offering the user a high flexibility with regards to the use of existing top jaws. The ROTA NCK-plus is available for all CNC lathes in the sizes 165 (6"), 210 (8"), 250 (10"), and 315 (12"), with clamping forces from 57 kN (12.814 lbf) to 144 kN (32.392 lbf). It is suitable for maximum speeds of 6,000 rpm and combines jaw strokes ranging from 2.75 (0.108") to 5.30mm (0.208") per jaw.
Contact Details
Related Glossary Terms
- chuck
chuck
Workholding device that affixes to a mill, lathe or drill-press spindle. It holds a tool or workpiece by one end, allowing it to be rotated. May also be fitted to the machine table to hold a workpiece. Two or more adjustable jaws actually hold the tool or part. May be actuated manually, pneumatically, hydraulically or electrically. See collet.
- clearance
clearance
Space provided behind a tool’s land or relief to prevent rubbing and subsequent premature deterioration of the tool. See land; relief.
- computer numerical control ( CNC)
computer numerical control ( CNC)
Microprocessor-based controller dedicated to a machine tool that permits the creation or modification of parts. Programmed numerical control activates the machine’s servos and spindle drives and controls the various machining operations. See DNC, direct numerical control; NC, numerical control.
- lathe
lathe
Turning machine capable of sawing, milling, grinding, gear-cutting, drilling, reaming, boring, threading, facing, chamfering, grooving, knurling, spinning, parting, necking, taper-cutting, and cam- and eccentric-cutting, as well as step- and straight-turning. Comes in a variety of forms, ranging from manual to semiautomatic to fully automatic, with major types being engine lathes, turning and contouring lathes, turret lathes and numerical-control lathes. The engine lathe consists of a headstock and spindle, tailstock, bed, carriage (complete with apron) and cross slides. Features include gear- (speed) and feed-selector levers, toolpost, compound rest, lead screw and reversing lead screw, threading dial and rapid-traverse lever. Special lathe types include through-the-spindle, camshaft and crankshaft, brake drum and rotor, spinning and gun-barrel machines. Toolroom and bench lathes are used for precision work; the former for tool-and-die work and similar tasks, the latter for small workpieces (instruments, watches), normally without a power feed. Models are typically designated according to their “swing,” or the largest-diameter workpiece that can be rotated; bed length, or the distance between centers; and horsepower generated. See turning machine.