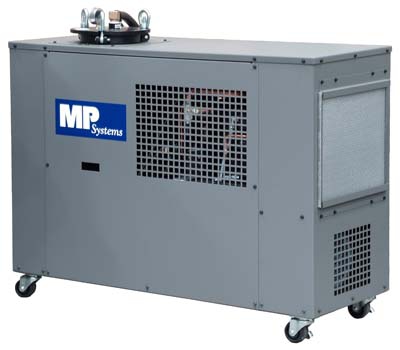
MP Systems Inc. has launched its first integrated chiller and high pressure coolant system. The all-in-one system, named the "S2," was developed specifically for the metal cutting industry, accommodating the growing need for high pressure, stabilized coolant to help maintain the tight tolerances of many parts.
"We dedicated a substantial amount of time developing the S2," says Mike Sayers, General Manager of MP Systems. "We believe we have solved all of the problems associated with other coolant chiller products currently available, including a space-saving design, optimal flow, real-time monitoring, and tidy hose routing."
The S2 can be integrated with most types of CNC machine tools, including machining centers, turning centers, and Swiss-style lathes. Either water or oil-based coolants may be used.
Real-time monitoring is managed by the S2's PLC (Programmable Logic Controller). The PLC directs the S2 to respond to changing conditions, such as air and tank temperatures and the outgoing coolant temperatures from the machine tool. The compact system stabilizes coolant to +/- 1 degree of ambient temperature. The controller also provides average temperature readings, eliminating random spikes or drops in temperatures.
A 7-day timer clock, an exclusive S2 feature, allows users to circulate and establish the coolant temperature in the machine tool tank up to one hour before starting the machine. This functionality decreases the wait time for the fluid to reach the desired temperature prior to cutting operations. The timer clock has two options, a Monday to Friday setting and a Saturday to Sunday setting to accommodate all shifts, including those that are "lights-out."
To help keep the shop floor neat and orderly, the S2 has a remote valve block. The manifold block may be mounted neatly on the machine with just one high pressure hose leading to the S2. This single-hose, remote manifold option addresses the clutter and safety risk of having multiple lines laying on the floor for multi-port and Swiss-type applications.
A built-in feed pump supplies the chiller and high pressure pump with optimum flow. It also accommodates aerated fluid exceptionally well, according to Mr. Sayers. When used with water-based coolant, the S2 pumps up to 1000 psi at 8 gallons per minute. With oils, it reaches up to 2000 psi at 5 gallons per minute.
Contact Details
Related Glossary Terms
- centers
centers
Cone-shaped pins that support a workpiece by one or two ends during machining. The centers fit into holes drilled in the workpiece ends. Centers that turn with the workpiece are called “live” centers; those that do not are called “dead” centers.
- computer numerical control ( CNC)
computer numerical control ( CNC)
Microprocessor-based controller dedicated to a machine tool that permits the creation or modification of parts. Programmed numerical control activates the machine’s servos and spindle drives and controls the various machining operations. See DNC, direct numerical control; NC, numerical control.
- coolant
coolant
Fluid that reduces temperature buildup at the tool/workpiece interface during machining. Normally takes the form of a liquid such as soluble or chemical mixtures (semisynthetic, synthetic) but can be pressurized air or other gas. Because of water’s ability to absorb great quantities of heat, it is widely used as a coolant and vehicle for various cutting compounds, with the water-to-compound ratio varying with the machining task. See cutting fluid; semisynthetic cutting fluid; soluble-oil cutting fluid; synthetic cutting fluid.
- feed
feed
Rate of change of position of the tool as a whole, relative to the workpiece while cutting.
- turning
turning
Workpiece is held in a chuck, mounted on a face plate or secured between centers and rotated while a cutting tool, normally a single-point tool, is fed into it along its periphery or across its end or face. Takes the form of straight turning (cutting along the periphery of the workpiece); taper turning (creating a taper); step turning (turning different-size diameters on the same work); chamfering (beveling an edge or shoulder); facing (cutting on an end); turning threads (usually external but can be internal); roughing (high-volume metal removal); and finishing (final light cuts). Performed on lathes, turning centers, chucking machines, automatic screw machines and similar machines.