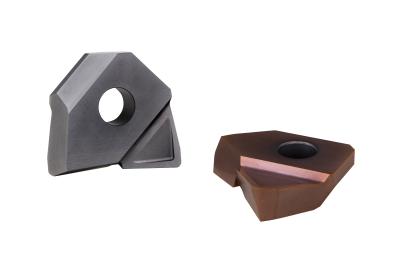
Dapra’s new SBD series inserts help operators finish their back draft jobs faster, with greater accuracy – and fewer insert changes – for maximum performance in long-reach, low-pressure finish cutting.
SBD inserts are the latest addition to Dapra’s EDGE² SBN finishing system and are interchangeable with SBN series twin-edge ballnose inserts. A positive-rake cutting wiper allows for larger stepdowns and faster feed rates than traditional back draft-style inserts. Ultrarobust carbide insert thickness provides optimal rigidity and heat control for superior tool life, and strong insert seating accepts cutting forces with minimal deflection to eliminate insert movement.
These inserts are available in 0.500” to 1.000” diameters. Dapra offers a choice of two new premium coatings for SBD: TS (AlTiN-based) for general-purpose machining in most steels, irons and 400 series stainless steel; and HM (AlCrN-based) for hardened steels, high-temperature alloys and tough 300 series and PH stainless steels.
Contact Details
Related Glossary Terms
- alloys
alloys
Substances having metallic properties and being composed of two or more chemical elements of which at least one is a metal.
- feed
feed
Rate of change of position of the tool as a whole, relative to the workpiece while cutting.
- stainless steels
stainless steels
Stainless steels possess high strength, heat resistance, excellent workability and erosion resistance. Four general classes have been developed to cover a range of mechanical and physical properties for particular applications. The four classes are: the austenitic types of the chromium-nickel-manganese 200 series and the chromium-nickel 300 series; the martensitic types of the chromium, hardenable 400 series; the chromium, nonhardenable 400-series ferritic types; and the precipitation-hardening type of chromium-nickel alloys with additional elements that are hardenable by solution treating and aging.
- wiper
wiper
Metal-removing edge on the face of a cutter that travels in a plane perpendicular to the axis. It is the edge that sweeps the machined surface. The flat should be as wide as the feed per revolution of the cutter. This allows any given insert to wipe the entire workpiece surface and impart a fine surface finish at a high feed rate.