Contact Details
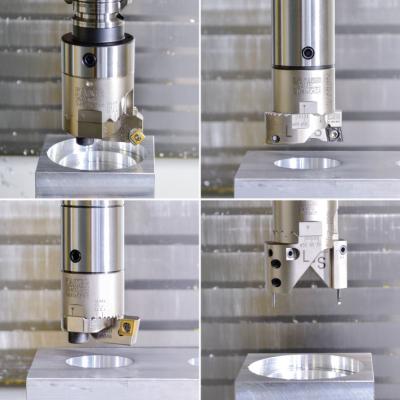
Limitations of using milling tools to prepare holes for finishing become apparent as hole depth and volume increase. This is where BIG KAISER’s Series 319SW Twin Cutter boring head showcases its capabilities and can solve the issue along with virtually any other holemaking problem for the range of 0.787" to 8.000”.
The Twin Cutter’s ability to take on heavier cuts allows shops to be more efficient. Whether it's eliminating multiple passes on the same bore or possibly allowing the use of existing smaller tools to create a starting hole, the Twin Cutter boring heads get the job done. Sometimes cast parts have more material to remove than was initially expected. Being able to balance- or step-cut with the same boring head helps minimize tooling and cycle times.
Also offered for the Twin Cutter boring heads are accessory insert holders to perform auxiliary operations not normally associated with this type of tooling.
Some parts have several bores in line with a blended angle in between. Insert holders with an adjustable insert cartridge allow the bore to be completed while producing the blend angle in one-pass, thus eliminating the need for follow-up tooling, such as an angled milling cutter. Back boring holders often eliminate the need for expensive dedicated special tools, and face grooving holders allow plunge cutting versus milling, so the process is much faster and imparts a finer surface finish.
Any industry using castings or forgings can generally benefit from twin cutting. It is designed for heavy-duty rough boring and semifinishing operations.
Related Glossary Terms
- boring
boring
Enlarging a hole that already has been drilled or cored. Generally, it is an operation of truing the previously drilled hole with a single-point, lathe-type tool. Boring is essentially internal turning, in that usually a single-point cutting tool forms the internal shape. Some tools are available with two cutting edges to balance cutting forces.
- boring head
boring head
Single- or multiple-point precision tool used to bring an existing hole within dimensional tolerance. The head attaches to a standard toolholder and a mechanism permits fine adjustments to be made to the head within a diameter range.
- gang cutting ( milling)
gang cutting ( milling)
Machining with several cutters mounted on a single arbor, generally for simultaneous cutting.
- grooving
grooving
Machining grooves and shallow channels. Example: grooving ball-bearing raceways. Typically performed by tools that are capable of light cuts at high feed rates. Imparts high-quality finish.
- milling
milling
Machining operation in which metal or other material is removed by applying power to a rotating cutter. In vertical milling, the cutting tool is mounted vertically on the spindle. In horizontal milling, the cutting tool is mounted horizontally, either directly on the spindle or on an arbor. Horizontal milling is further broken down into conventional milling, where the cutter rotates opposite the direction of feed, or “up” into the workpiece; and climb milling, where the cutter rotates in the direction of feed, or “down” into the workpiece. Milling operations include plane or surface milling, endmilling, facemilling, angle milling, form milling and profiling.
- milling cutter
milling cutter
Loosely, any milling tool. Horizontal cutters take the form of plain milling cutters, plain spiral-tooth cutters, helical cutters, side-milling cutters, staggered-tooth side-milling cutters, facemilling cutters, angular cutters, double-angle cutters, convex and concave form-milling cutters, straddle-sprocket cutters, spur-gear cutters, corner-rounding cutters and slitting saws. Vertical cutters use shank-mounted cutting tools, including endmills, T-slot cutters, Woodruff keyseat cutters and dovetail cutters; these may also be used on horizontal mills. See milling.