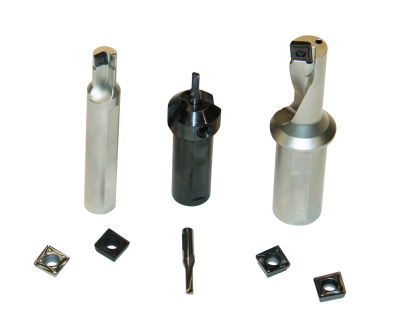
Arno Werkzeuge USA announces the introduction of their new SHARK-Cut multipurpose cutting tool platform for a range of turning applications. SHARK-Cut allows machines shops to use just one tool for four different machining operations including: facing, drilling, boring and turning.
By combining four operations into just one tool, the SHARK-Cut multipurpose cutting tool system offers an immediate cost savings of up to 35 to 50 percent, eliminating the need for purchasing additional cutting tools such as drills, boring bars and inserts. ARNO USA also contends while initial hardware cost savings are significant, it is only a small part of the total reduced costs and return on investment that machine shops will gain from utilizing their SHARK-Cut multipurpose tools and inserts. SHARK-Cut provides machine shops even greater cost savings, efficiencies, and flexibility by reducing tool set-up time costs and tool indexing time between operations. Moreover, it creates more room on the turret for use of other tools so machine shops can better manage and maximize the productivity of their machine tools.
Small to large, high-volume CNC machining operations will realize dramatic cost savings and returns while improving cycle times and profits with SHARK-Cut multipurpose cutting tools from ARNO USA. The SHARK-Cut product range features inserts that are peripheral ground and precision pressed in grades and geometries suited to machining a wide variety of materials. This includes aluminum/nonferrous, steel and high-temperature alloys. Multiple coolant ports ensure excellent cutting-edge emersion and chip evacuation.
SHARK-Cut Technical Specifications
Diameter Ranges:
- Shark-cut Mini 2.25xD Solid Carbide .160” (4mm) – .315” (8mm)
- Shark-cut Mini-ALU (Nonferrous Materials) 2.25xD Solid Carbide .160” (4mm) – .315” (8mm)
- Shark-Cut 1.5xD depth of cuts .315” (8mm) – 1 ¼” (32mm)
- Shark-Cut 2.25xD depth of cuts .315” (8mm) – 1 ¼” (32mm)
- Shark-Cut 3.0xD (Densimet) depth of cuts .315” (8mm) – 1 ¼” (32mm)
Indexable Inserts for Machining
LPET and LPNT:
- Steel
- Stainless Steel
- Cast Iron
- Nonferrous
- High-Temperature Alloys
Wiper Chipbreaker available:
- Faster production times
- Improved surface finishes
ALU Chipbreaker:
- Nonferrous Materials
Four Machining Operations with One Tool:
- Facing
- Drilling
- Boring
- Turning
Contact Details
Related Glossary Terms
- alloys
alloys
Substances having metallic properties and being composed of two or more chemical elements of which at least one is a metal.
- boring
boring
Enlarging a hole that already has been drilled or cored. Generally, it is an operation of truing the previously drilled hole with a single-point, lathe-type tool. Boring is essentially internal turning, in that usually a single-point cutting tool forms the internal shape. Some tools are available with two cutting edges to balance cutting forces.
- chipbreaker
chipbreaker
Groove or other tool geometry that breaks chips into small fragments as they come off the workpiece. Designed to prevent chips from becoming so long that they are difficult to control, catch in turning parts and cause safety problems.
- computer numerical control ( CNC)
computer numerical control ( CNC)
Microprocessor-based controller dedicated to a machine tool that permits the creation or modification of parts. Programmed numerical control activates the machine’s servos and spindle drives and controls the various machining operations. See DNC, direct numerical control; NC, numerical control.
- coolant
coolant
Fluid that reduces temperature buildup at the tool/workpiece interface during machining. Normally takes the form of a liquid such as soluble or chemical mixtures (semisynthetic, synthetic) but can be pressurized air or other gas. Because of water’s ability to absorb great quantities of heat, it is widely used as a coolant and vehicle for various cutting compounds, with the water-to-compound ratio varying with the machining task. See cutting fluid; semisynthetic cutting fluid; soluble-oil cutting fluid; synthetic cutting fluid.
- turning
turning
Workpiece is held in a chuck, mounted on a face plate or secured between centers and rotated while a cutting tool, normally a single-point tool, is fed into it along its periphery or across its end or face. Takes the form of straight turning (cutting along the periphery of the workpiece); taper turning (creating a taper); step turning (turning different-size diameters on the same work); chamfering (beveling an edge or shoulder); facing (cutting on an end); turning threads (usually external but can be internal); roughing (high-volume metal removal); and finishing (final light cuts). Performed on lathes, turning centers, chucking machines, automatic screw machines and similar machines.
- wiper
wiper
Metal-removing edge on the face of a cutter that travels in a plane perpendicular to the axis. It is the edge that sweeps the machined surface. The flat should be as wide as the feed per revolution of the cutter. This allows any given insert to wipe the entire workpiece surface and impart a fine surface finish at a high feed rate.