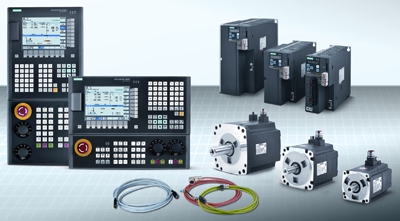
Siemens Industry Inc. announced its new Sinumerik 808D Advanced CNC, designed for basic milling and turning machines. Affordably priced for the machine builder (OEM), this new addition from Siemens offers a suite of design features to reportedly improve the accuracy, surface finish, safety and communication of the control. This new CNC is available now to the North American machine tool market.
The Sinumerik 808D Advanced offers up to five axes/spindle motion control on a single machine channel, with drive bus communication between the CNC and drive for better position control, data transfer over standard Ethernet protocol, plus Auto Servo Tuning (AST) for superior surface quality and repeatable part accuracy in mold and die applications. These include incremental encoder with 2,500 parts per revolution (ppr) or absolute encoder with 20-bit resolution.
Motor speeds up to 4,000 rpm are offered with Safe Torque Off (STO) and IP65 enclosure protection. Vertical and horizontal configurations of the Sinumerik 808D are available to suit all standard control panels.
The Sinumerik 808D Advanced T is a choice for basic turning machines or turning centers without a Y-axis, with the option of driven tools, while the Sinumerik 808D Advanced M offers advanced surface finish and the SINAMICS V70 drive platform from Siemens, all with an attractive price-to-performance ratio.
Additional features of the Sinumerik 808D Advanced CNC include an RJ45 Ethernet port, 7.5" LCD color display with 640 x 480 resolution for easy viewing, machine technology-specific keyboards with hard keys shielded with protective membrane, a robust enclosure with no fan or hard disk, maintenance-friendly power with no battery, continuous data buffering with NV-RAM technology, LED tool number display and a master control panel with rotary switch for feed and spindle override. The rated torque is 1.9-40 Nm with drive line input of 400V and overload rating of 300 percent.
Part programs can be managed on an external PC, then fed to the control over an Ethernet cable or input via the USB port. Simple program sub-folders can be stored on the control, just like on the PC. Other standard features of the Siemens CNC for machine operators and programmers include intelligent jog, precise tool data handling with easy-to-recognize on-screen icons, tool wear data logging to ensure consistent high workpiece quality and startGUIDE engineering support, complete with the graphical user interface wizard for easier machine commissioning and startup and troubleshooting.
Contact Details
Related Glossary Terms
- centers
centers
Cone-shaped pins that support a workpiece by one or two ends during machining. The centers fit into holes drilled in the workpiece ends. Centers that turn with the workpiece are called “live” centers; those that do not are called “dead” centers.
- computer numerical control ( CNC)
computer numerical control ( CNC)
Microprocessor-based controller dedicated to a machine tool that permits the creation or modification of parts. Programmed numerical control activates the machine’s servos and spindle drives and controls the various machining operations. See DNC, direct numerical control; NC, numerical control.
- feed
feed
Rate of change of position of the tool as a whole, relative to the workpiece while cutting.
- gang cutting ( milling)
gang cutting ( milling)
Machining with several cutters mounted on a single arbor, generally for simultaneous cutting.
- milling
milling
Machining operation in which metal or other material is removed by applying power to a rotating cutter. In vertical milling, the cutting tool is mounted vertically on the spindle. In horizontal milling, the cutting tool is mounted horizontally, either directly on the spindle or on an arbor. Horizontal milling is further broken down into conventional milling, where the cutter rotates opposite the direction of feed, or “up” into the workpiece; and climb milling, where the cutter rotates in the direction of feed, or “down” into the workpiece. Milling operations include plane or surface milling, endmilling, facemilling, angle milling, form milling and profiling.
- turning
turning
Workpiece is held in a chuck, mounted on a face plate or secured between centers and rotated while a cutting tool, normally a single-point tool, is fed into it along its periphery or across its end or face. Takes the form of straight turning (cutting along the periphery of the workpiece); taper turning (creating a taper); step turning (turning different-size diameters on the same work); chamfering (beveling an edge or shoulder); facing (cutting on an end); turning threads (usually external but can be internal); roughing (high-volume metal removal); and finishing (final light cuts). Performed on lathes, turning centers, chucking machines, automatic screw machines and similar machines.