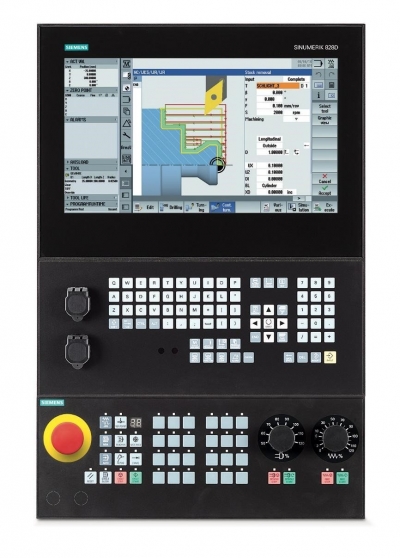
Siemens now offers its popular mid-range CNC, the Sinumerik 828D, with version 4.8 of the operating system. With the release of version 4.8, Siemens offers an array of new hardware and software solutions for its integrated Sinumerik portfolio. The offering comprises integrated industrial software and automation technology designed to enable machine tool manufacturers to leverage the full productivity potential of the digital factory in a mid-range control.
Sinumerik 828D is a compact, panel-based CNC, offered in vertical and horizontal models for highly flexible machine design integration, while the resident Siemens technologies of Advanced Surface and Top Surface ensure the optimal surface finishes with 80-bit nano floating point accuracy. Also standard on the 828D are the popular Siemens Shop-Mill and Shop-Turn graphical programming with interactive input help through animated elements.
Up to 10 axes of motion with two auxiliary axes are possible. Color displays, in sizes 10.4” or 15.4”, and Simatic S7 PLC are also standard. With three steps in the new software version, depending upon the motion control needed, Siemens is bringing the 828D standard models to a competitive price point for the builders of CNC milling, turning and grinding machines.
With its new Sinumerik CNC software release 4.8, Siemens is making a range of new functions available to improve the speed, precision and safety of intermediate milling, turning and grinding machine tools, with simplified ISO code programming. Features of version 4.8 include facility for compensating unwanted axis nodding movements and protection against machine, tool and workpiece collisions. Nodding compensation (NoCo) is used to compensate for dynamic position deviations in one or more linear machine axes caused by acceleration processes.
These position deviations are caused by what is known as mechanical compliance within the machine. NoCo compensates for the dominant position deviation by initiating a corrective movement in the relevant machine axis, enabling improved machining quality simultaneously with higher jerk and acceleration values. Nodding compensation can be used in conjunction with any technology, such as milling, multitasking, tapping, laser machining or water jet machining. NoCo is available in two variants: Eco and Advanced. The Eco variant is designed for dominant acceleration effects in which the compensation axis is combined with one influencing variable. Where there are several influencing variables that require several compensation axes, the Advanced variant is the option of choice.
The Sinumerik software release 4.8 also features a collision protection: Collision Avoidance Eco and Collision Avoidance Advanced. The Eco version enables machine protection by preventing collisions of the machine body with its own components within the work area.
To achieve this effect in real-time, the assemblies which need protection are calculated as simple geometric bodies. This collision monitoring system is available in all three operating modes: JOG, MDA and Automatic. The protected areas can be engineered and visualized as a 3D image at the control interface. The Advanced variant includes full machine, tool and workpiece protection.
The software provided by the Sinumerik product partner ModuleWorks runs via an interface integrated on an external PC and works together with the Sinumerik CNC in real-time to ensure that the machine, tool and workpiece can be continuously monitored and are dynamically protected during the stock removal process. The workpiece and tool data required is made available to the system during setup. Collision Avoidance provides safety during operation.
Contact Details
Related Glossary Terms
- computer numerical control ( CNC)
computer numerical control ( CNC)
Microprocessor-based controller dedicated to a machine tool that permits the creation or modification of parts. Programmed numerical control activates the machine’s servos and spindle drives and controls the various machining operations. See DNC, direct numerical control; NC, numerical control.
- gang cutting ( milling)
gang cutting ( milling)
Machining with several cutters mounted on a single arbor, generally for simultaneous cutting.
- grinding
grinding
Machining operation in which material is removed from the workpiece by a powered abrasive wheel, stone, belt, paste, sheet, compound, slurry, etc. Takes various forms: surface grinding (creates flat and/or squared surfaces); cylindrical grinding (for external cylindrical and tapered shapes, fillets, undercuts, etc.); centerless grinding; chamfering; thread and form grinding; tool and cutter grinding; offhand grinding; lapping and polishing (grinding with extremely fine grits to create ultrasmooth surfaces); honing; and disc grinding.
- grinding machine
grinding machine
Powers a grinding wheel or other abrasive tool for the purpose of removing metal and finishing workpieces to close tolerances. Provides smooth, square, parallel and accurate workpiece surfaces. When ultrasmooth surfaces and finishes on the order of microns are required, lapping and honing machines (precision grinders that run abrasives with extremely fine, uniform grits) are used. In its “finishing” role, the grinder is perhaps the most widely used machine tool. Various styles are available: bench and pedestal grinders for sharpening lathe bits and drills; surface grinders for producing square, parallel, smooth and accurate parts; cylindrical and centerless grinders; center-hole grinders; form grinders; facemill and endmill grinders; gear-cutting grinders; jig grinders; abrasive belt (backstand, swing-frame, belt-roll) grinders; tool and cutter grinders for sharpening and resharpening cutting tools; carbide grinders; hand-held die grinders; and abrasive cutoff saws.
- laser machining
laser machining
Intensified, pulsed beams of light generated by lasers—typically carbon dioxide or neodium-doped yttrium aluminum garnet (Nd:YAG)—that drill, weld, engrave, mark, slit and caseharden. Usually under CNC, often at both high cutting rates (100 linear in./sec.) and high power (5kW or more). Lasers also are used in conjunction with in-process quality-control monitoring systems allowing measuring accuracies of 0.00001".
- milling
milling
Machining operation in which metal or other material is removed by applying power to a rotating cutter. In vertical milling, the cutting tool is mounted vertically on the spindle. In horizontal milling, the cutting tool is mounted horizontally, either directly on the spindle or on an arbor. Horizontal milling is further broken down into conventional milling, where the cutter rotates opposite the direction of feed, or “up” into the workpiece; and climb milling, where the cutter rotates in the direction of feed, or “down” into the workpiece. Milling operations include plane or surface milling, endmilling, facemilling, angle milling, form milling and profiling.
- tapping
tapping
Machining operation in which a tap, with teeth on its periphery, cuts internal threads in a predrilled hole having a smaller diameter than the tap diameter. Threads are formed by a combined rotary and axial-relative motion between tap and workpiece. See tap.
- turning
turning
Workpiece is held in a chuck, mounted on a face plate or secured between centers and rotated while a cutting tool, normally a single-point tool, is fed into it along its periphery or across its end or face. Takes the form of straight turning (cutting along the periphery of the workpiece); taper turning (creating a taper); step turning (turning different-size diameters on the same work); chamfering (beveling an edge or shoulder); facing (cutting on an end); turning threads (usually external but can be internal); roughing (high-volume metal removal); and finishing (final light cuts). Performed on lathes, turning centers, chucking machines, automatic screw machines and similar machines.