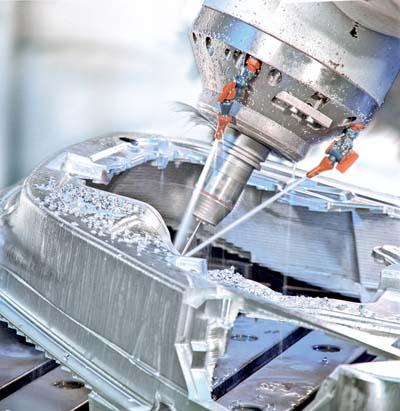
Siemens Industry Inc. announced today that the new Sinumerik MDynamics technology package for milling applications is now available. The technology package combines CNC hardware, intelligent CNC functions and the complete CAD/CAM/CNC process chain for industries with very high requirements regarding surface quality, precision and machining speeds. Sinumerik MDynamics is especially suitable for applications in automotive and aircraft construction, power engineering and medical part manufacturing, as well as in job shop production and tool- and mold-making.
The three-axis technology package for the Sinumerik 840D sl, for example, includes not only a new and improved form of motion control, but also innovative set-up functions, as well as a new tool and program management system. Workpiece programming is facilitated by new programming functions and the ShopMill machining step programming. Innovative technology cycles, automatic measuring cycles, residual material detection, 3D simulation to support programming as well as efficient high-speed cutting (HSC) functions have also been integrated. New HMI functions, easy data and program handling with an additional Compact Flash (CF) card memory, spline interpolation and workpiece simulation for multi-face machining complete the package.
The five-axis package is supplemented by the Cycle996 kinematic measuring cycle, 3D radius compensation and expanded five-axis functions, including integrated kinematic Transformation Tool Center Point programming (TRAORI).
The new integrated High-Speed Setting Cycle832 ensures rapid adaptation to the machining strategy. Innovative technology cycles for trochoidal or plunge milling enable fast, simple and efficient workpiece machining. User-friendly and speedy handling of complex workpieces, in both JOG and automatic mode, is possible with the new Cycle800 swivel cycle for complete machining. The remaining runtime display and the visualization of large mold-making programs support the operator during machining.
Contact Details
Related Glossary Terms
- computer numerical control ( CNC)
computer numerical control ( CNC)
Microprocessor-based controller dedicated to a machine tool that permits the creation or modification of parts. Programmed numerical control activates the machine’s servos and spindle drives and controls the various machining operations. See DNC, direct numerical control; NC, numerical control.
- flash
flash
Thin web or film of metal on a casting that occurs at die partings and around air vents and movable cores. This excess metal is due to necessary working and operating clearances in a die. Flash also is the excess material squeezed out of the cavity as a compression mold closes or as pressure is applied to the cavity.
- gang cutting ( milling)
gang cutting ( milling)
Machining with several cutters mounted on a single arbor, generally for simultaneous cutting.
- interpolation
interpolation
Process of generating a sufficient number of positioning commands for the servomotors driving the machine tool so the path of the tool closely approximates the ideal path. See CNC, computer numerical control; NC, numerical control.
- milling
milling
Machining operation in which metal or other material is removed by applying power to a rotating cutter. In vertical milling, the cutting tool is mounted vertically on the spindle. In horizontal milling, the cutting tool is mounted horizontally, either directly on the spindle or on an arbor. Horizontal milling is further broken down into conventional milling, where the cutter rotates opposite the direction of feed, or “up” into the workpiece; and climb milling, where the cutter rotates in the direction of feed, or “down” into the workpiece. Milling operations include plane or surface milling, endmilling, facemilling, angle milling, form milling and profiling.
- plunge milling
plunge milling
Highly productive method of metal removal in which an axial machining operation is performed in a single tool sequence. The tool makes a series of overlapping, drill-like plunges to remove part of a cylindrical plug of material one after another. Because of the increased rigidity of a Z-axis move, the tool can cover a large cross-section of material.