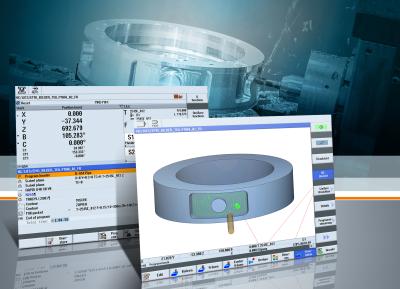
With version 4.7 of the Sinumerik Operate graphical user interface software, Siemens Industry Inc. reportedly improved multi-tasking with machine tools, according to a company announcement release today.
Sinumerik Operate and the Sinumerik 840D sl CNC combine several machining technologies such as turning, milling and drilling, as well as workpiece and tool measurement on one machine, which is said to guarantee the complete machining of highly complex workpieces such as those found in the aerospace industry. Version 4.7 of the software features extended setup and manual modes (JOG), which now interactively support the user when setting up mill-turn machines. Also new is a measurement function for turning tools where the setting screen automatically changes depending on the tool type to be measured.
In addition, the new software version improves workpiece measurement—now enabling the user to easily check and specify the workpiece zero—and simplifies the approach of turning tools in tool setup mode (TSM). When a user selects a turning tool, the machine automatically switches to turning mode.
Highlights of the latest Sinumerik Operate software version include:
- Cross-technology, standardized look-and-feel for milling, turning, drilling and measurement functions.
- Complete machining in one clamping.
- Flexible NC programming using programGuide and ShopMill/ShopTurn.
Contact Details
Related Glossary Terms
- computer numerical control ( CNC)
computer numerical control ( CNC)
Microprocessor-based controller dedicated to a machine tool that permits the creation or modification of parts. Programmed numerical control activates the machine’s servos and spindle drives and controls the various machining operations. See DNC, direct numerical control; NC, numerical control.
- gang cutting ( milling)
gang cutting ( milling)
Machining with several cutters mounted on a single arbor, generally for simultaneous cutting.
- milling
milling
Machining operation in which metal or other material is removed by applying power to a rotating cutter. In vertical milling, the cutting tool is mounted vertically on the spindle. In horizontal milling, the cutting tool is mounted horizontally, either directly on the spindle or on an arbor. Horizontal milling is further broken down into conventional milling, where the cutter rotates opposite the direction of feed, or “up” into the workpiece; and climb milling, where the cutter rotates in the direction of feed, or “down” into the workpiece. Milling operations include plane or surface milling, endmilling, facemilling, angle milling, form milling and profiling.
- numerical control ( NC)
numerical control ( NC)
Any controlled equipment that allows an operator to program its movement by entering a series of coded numbers and symbols. See CNC, computer numerical control; DNC, direct numerical control.
- turning
turning
Workpiece is held in a chuck, mounted on a face plate or secured between centers and rotated while a cutting tool, normally a single-point tool, is fed into it along its periphery or across its end or face. Takes the form of straight turning (cutting along the periphery of the workpiece); taper turning (creating a taper); step turning (turning different-size diameters on the same work); chamfering (beveling an edge or shoulder); facing (cutting on an end); turning threads (usually external but can be internal); roughing (high-volume metal removal); and finishing (final light cuts). Performed on lathes, turning centers, chucking machines, automatic screw machines and similar machines.