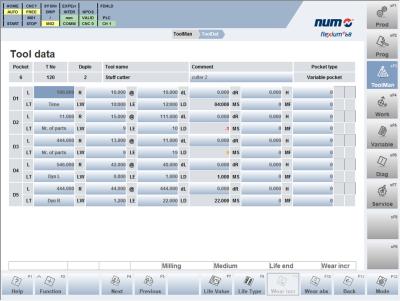
NUM has released a new software facility for its latest-generation Flexium+ CNC platform that places an advanced tool management system at the disposal of manufacturers operating multiple CNC machine tools. It is especially suitable for complex high-end milling applications, as well as HSM applications in the mold and die market.
Forming part of the latest version of NUM’s acclaimed Flexium+ software (V4.1.00.00), the new tool management facility provides a comprehensive and constantly accessible database that can either be installed on a server platform for use with multiple CNC machine tools in a large production plant, or can be used standalone on a single CNC machine tool.
The tool management software includes PLC libraries, as well as dedicated CNC functions and HMI pages. It can handle a very large number of tools of different types – including turning, milling and boring – and standard, medium or large sizes. Duplo tools with identical cutting characteristics are also supported, as are different types of tool magazines such as disk, chain or rack. New tool characteristics are managed at maximum speed and maximum feed rate, and the tool life can be monitored over time, by wear amount or by the number of operations. Pre-emptive warning messages are generated automatically, whenever specified limits are approached.
The software provides an especially comprehensive set of extensions for tool characteristics. In addition to standard items such as the name, type and number of cuts – as many as 18 of which can be specified – extensions are also provided to handle numerous other factors, including magazine size, life management, technological characteristics such as maximum speed and speed rate, and status/warning indicators.
Developed primarily as a high-end system for complex tasks in milling applications, the software offers highly sophisticated NCK features such as a large block look-ahead capability in excess of 1,000, together with very short NCK cycle times. These features also make the system ideal for HSM applications in the mold and die market.
NUM’s new tool management system is very easy to use and requires no special software tools. Users simply employ NUM’s Flexium Tools software to extend the scope of their project to the database server. A full set of API functions is included to implement all necessary tool operations, together with a number of dedicated functions in NCK firmware. The system also includes different logical HMI list pages for spindle and magazine view, tool view and tool data table, enabling users to visualize the complete content of tool information and current status.
According to Werner Heimpel, NUM’s product manager for HMI and software tools, “Manufacturers operating multiple CNC machine tools are often forced to devote significant resources to tool management. NUM’s new system can help them to save considerable engineering costs in the long term.”
Related Glossary Terms
- boring
boring
Enlarging a hole that already has been drilled or cored. Generally, it is an operation of truing the previously drilled hole with a single-point, lathe-type tool. Boring is essentially internal turning, in that usually a single-point cutting tool forms the internal shape. Some tools are available with two cutting edges to balance cutting forces.
- computer numerical control ( CNC)
computer numerical control ( CNC)
Microprocessor-based controller dedicated to a machine tool that permits the creation or modification of parts. Programmed numerical control activates the machine’s servos and spindle drives and controls the various machining operations. See DNC, direct numerical control; NC, numerical control.
- feed
feed
Rate of change of position of the tool as a whole, relative to the workpiece while cutting.
- gang cutting ( milling)
gang cutting ( milling)
Machining with several cutters mounted on a single arbor, generally for simultaneous cutting.
- look-ahead
look-ahead
CNC feature that evaluates many data blocks ahead of the cutting tool’s location to adjust the machining parameters to prevent gouges. This occurs when the feed rate is too high to stop the cutting tool within the required distance, resulting in an overshoot of the tool’s projected path. Ideally, look-ahead should be dynamic, varying the distance and number of program blocks based on the part profile and the desired feed rate.
- milling
milling
Machining operation in which metal or other material is removed by applying power to a rotating cutter. In vertical milling, the cutting tool is mounted vertically on the spindle. In horizontal milling, the cutting tool is mounted horizontally, either directly on the spindle or on an arbor. Horizontal milling is further broken down into conventional milling, where the cutter rotates opposite the direction of feed, or “up” into the workpiece; and climb milling, where the cutter rotates in the direction of feed, or “down” into the workpiece. Milling operations include plane or surface milling, endmilling, facemilling, angle milling, form milling and profiling.
- turning
turning
Workpiece is held in a chuck, mounted on a face plate or secured between centers and rotated while a cutting tool, normally a single-point tool, is fed into it along its periphery or across its end or face. Takes the form of straight turning (cutting along the periphery of the workpiece); taper turning (creating a taper); step turning (turning different-size diameters on the same work); chamfering (beveling an edge or shoulder); facing (cutting on an end); turning threads (usually external but can be internal); roughing (high-volume metal removal); and finishing (final light cuts). Performed on lathes, turning centers, chucking machines, automatic screw machines and similar machines.