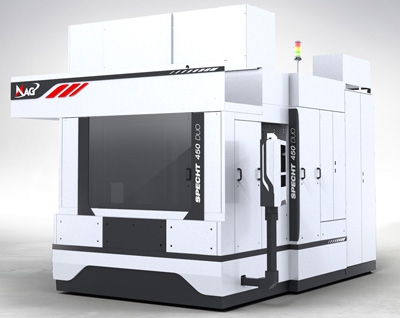
MAG introduces the new twin-spindle SPECHT 450 DUO with numerous technical innovations, outstanding technical data and market leading tool change times to maximize productity in the small engine and parts production market.
The high-performance system machines of the SPECHT series are used as CNC modules in agile or hybrid manufacturing systems. Their modular design offers single and twin-spindle versions for passenger car and commercial vehicle powertrain applications. The twin-spindle machining centers from MAG reportedly provide maximum productivity in large-scale manufacturing, virtually replacing two entire machines while providing the highest reliability and quality levels. The new twin-spindle SPECHT 450 DUO, with only 11.2 sq. m2; of floor space and a comfortable spindle distance of 540mm, is the smallest twin-spindle machine of the SPECHT family and is designed for the machining of mid-sized workpieces such as cylinder heads or gear housings and more. MAG thereby fulfills the increased demand for highly-productive systems for smaller engines of up to approximately 1.4 liters. The first manufacturing line for high volume cylinder head machining is already being delivered.
The need to meet the demand for reduced emissions and improved fuel economy is driving the growth of small engine production and increased component accuracies. The SPECHT DUO meets this need with compensation in all linear axes, precise glass scales, integrated tool monitoring and cone cleaning as well as the use of a zero-point clamping system contribute further to the highest processing quality and process safety.
The machine has a chip-to-chip time of less than 2.5 seconds and a tool change time of less than 1 second. The new, patented tool magazine allows for these record times thanks to the intelligent interplay of innovative components for tool change: it combines a chain magazine and two disc magazines. The use of a specially developed, intelligent management tool system without space coding optimizes the provision of tools.
MAG's proprietary tool management software reduces idle times to a minimum. The magazine has a capcity for 112 tools and allows in-cycle tool loading at ground level without an operator platform, saving additional time.
The smallest machine of the series shows its strengths with its features: the SPECHT's high performance components enable substantial improvements when it comes to dynamics and productivity. Generously dimensioned ball screws allow high axial acceleration of 9 m/s2;. Modern HSK-A63 motor spindles from MAG's own component manufacturing with up to 18,000 1/min, 42 kW and 180 Nm are available for high-performance machining. In addition to the powerful drives, spindles and large tool capacities, large axis paths and the comfortable spindle distance of 540mm make for high workpiece flexibility. The compact design creates the foundation for the creation of systems with a very high output and minimal use of space.
The automation interfaces allow for automatic top loading or front loading as well as manual loading. Energy efficiency: SPECHT already the leading standard The standard version of the SPECHT series features a best in class environmental and energy management system which lowers consumption in many ways, reduces polluting effects and providing a clean, safe workplace. Even in the standard configuration, the machines are among the most efficient in their class. In addition, MAG provides manufacturers an energy efficiency package upon request, providing energy consumption up to 30 percent less than comparable CNC machines. This consists of modular options, such as a start-stop hydraulic unit, a high-pressure cooling system with variable-speed pump or a cooling unit with controlled compressor.
Like all machines of the SPECHT series, the new SPECHT 450 DUO can also be operated with minimum quantity lubrication. Chip management work piece cleaning, work space design and various measures for safely machining with a "dry" process have been developed for this purpose. MAG was a pioneer in the development of MQL technology 25 years ago. Through continuous development, the reliable application of various materials was also implemented in large-scale production and made the benefits in terms of machining process, ecology and environment available at all times.
Contact Details
Related Glossary Terms
- centers
centers
Cone-shaped pins that support a workpiece by one or two ends during machining. The centers fit into holes drilled in the workpiece ends. Centers that turn with the workpiece are called “live” centers; those that do not are called “dead” centers.
- computer numerical control ( CNC)
computer numerical control ( CNC)
Microprocessor-based controller dedicated to a machine tool that permits the creation or modification of parts. Programmed numerical control activates the machine’s servos and spindle drives and controls the various machining operations. See DNC, direct numerical control; NC, numerical control.
- modular design ( modular construction)
modular design ( modular construction)
Manufacturing of a product in subassemblies that permits fast and simple replacement of defective assemblies and tailoring of the product for different purposes. See interchangeable parts.