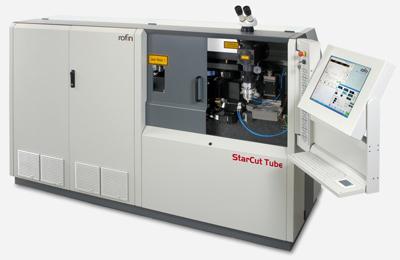
Manufacturing a wide range of miniature thin-walled tube products requires the highest precision from the cutting and drilling processes used to produce them. The delicate tube material has to be machined without inducing distortion or leaving burrs, and this is where laser systems such as ROFIN's StarCut Tube offer significant advantages when compared to chemical and mechanical machining procedures, according to the company.
Manufacturing parts for implants, instruments or endoscopes from round or oval tubes usually requires numerous different machining steps. Techniques such as drilling, milling or ablation, when carried out as separate processes, slow down the overall manufacturing speed. At the same time, in this scenario, the risk of production waste increases with each additional step. The StarCut Tube, 4-axes CNC laser processing system however, allows numerous mechanical machining steps to be encompassed within a single laser processing routine. With CNC-driven rotary-, x-, y- and z-axes and a solid granite machine set-up, even taper-free and offset cuts are as easy as processing simple oval tubes or flat parts.
Streamlining the manufacturing process with a laser system reduces the processing time of parts, with components up to 600mm in length being completed in just a few minutes. With such short cycle times, providing a constant supply of raw material is essential to maintaining production efficiency. To ensure the StarCut Tube always has a readily available supply, ROFIN has developed a new tube loading module with a side-loading magazine for tubes ranging from 3mm to 30mm in diameter and up to 3 m in length. A walking-beam separation system ensures precise and gentle handling of small diameter tubes. Sophisticated grippers provide accurate and reliable tube feeding together with the automated removal of residual material.
The automated tube loading module is also available for wet cutting. Wet laser cutting with its resultant burr-free and oxide-free machined edges dramatically reduces the need for post-processing, offering huge potential savings. The entire water cooling system has been integrated within the main machine housing. Designed with a special focus on ease of operation and maintenance, the water tank is easily accessible and removable for water changes. An integral drawer allows removal of finished parts, without interrupting the cutting process.
The StarCut Tube can be powered with a wide range of ROFIN laser sources including: StarFemto FX, StarPico or StarFiber FC, which can deliver contour accuracies better than +/-5µm. The femtosecond laser source provides pulse lengths down to 300 fs and wavelengths of 1030 nm, 515 nm and 343 nm. Pulses shorter than 1 ps are an essential prerequisite for true, cold material processing and distortion-free cutting and drilling of polymers.
Powerful and high-performance laser systems are just one part of the ROFIN philosophy. Customers expect much more from their partner than just suitable laser systems. ROFIN's specialists take care of the employee's training, help set up the first application, and pro-active application support is provided during the first months. If required, ROFIN can even design the production room according to the relevant laser safety standards.
Related Glossary Terms
- computer numerical control ( CNC)
computer numerical control ( CNC)
Microprocessor-based controller dedicated to a machine tool that permits the creation or modification of parts. Programmed numerical control activates the machine’s servos and spindle drives and controls the various machining operations. See DNC, direct numerical control; NC, numerical control.
- flat ( screw flat)
flat ( screw flat)
Flat surface machined into the shank of a cutting tool for enhanced holding of the tool.
- gang cutting ( milling)
gang cutting ( milling)
Machining with several cutters mounted on a single arbor, generally for simultaneous cutting.
- milling
milling
Machining operation in which metal or other material is removed by applying power to a rotating cutter. In vertical milling, the cutting tool is mounted vertically on the spindle. In horizontal milling, the cutting tool is mounted horizontally, either directly on the spindle or on an arbor. Horizontal milling is further broken down into conventional milling, where the cutter rotates opposite the direction of feed, or “up” into the workpiece; and climb milling, where the cutter rotates in the direction of feed, or “down” into the workpiece. Milling operations include plane or surface milling, endmilling, facemilling, angle milling, form milling and profiling.