Contact Details
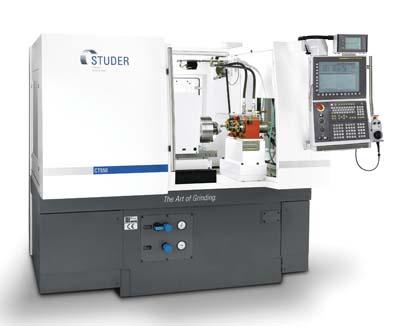
With the recent addition of the Studer CT internal cylindrical grinding machine series, United Grinding has substantially increased their ID grinding capabilities. In the area of internal grinding of chucking components, the Studer CT550 sets new standards. Higher precision, better surface quality, high metal removal rates, in addressing these requirements, UGT has again set the standard with its new CT550 CNC internal/universal cylindrical grinder. It works more quickly and precisely, offers a broader range of applications, with production options that are highly attractive with regard to cost-effectiveness. By saving on auxiliary times, the CT550 considerably shortens the cycle times of the grinding process.
The CT550 is a compact machine for medium-sized workpieces with up to three inline grinding spindles. The modular and flexible arrangement of spindles enables optimal dimensioning of the machine, ranging from the manufacture of individual parts as well as large-scale production. This machine also supports integrated and autonomous loading system
The Granitan S103 machine bed provides a very solid, rigid and thermally stable CT550. The formula of this mineral casting is designed for optimal grinding operation conditions. Thus, the machine bed literally provides the integrated guide system with a stable basis for absorbing the high forces that occur during grinding.
Thanks to its remarkable thermal behavior, the machine bed largely equalizes brief variations in temperature, so that the machine operates with consistently high precision even with changing ambient temperatures. Its high rigidity and excellent damping provide the basic prerequisites for outstanding surface quality of ground parts and long grinding wheel lifetimes.
Studer's CT550 is ideal for small- to medium-sized internal cylindrical grinding applications such as die plates, spring collets, tool holding fixtures, hydraulic components, and thread ring gauges composed of hard materials like tool steel, carbide, ceramics and glass.
Three inline modular spindles provide flexibility and optimal dimensioning to the machine. The diameter of the HF (high frequency) spindle ranges form 80mm to 120mm. The belt-driven spindle diameter is 80mm. External grinding wheel is 305mm. Axes travels are 520mm X and 250mm. The manual B-axis setting angle is +1ÌÜÅÁ/-1ÌÜÅÁ. Workhead speed is 1200 rpm, maximum. Load on the spindle nose, 100 kg. Center height above the table is 1500mm. Maximum part length, 650mm, while the grinding length is 150mm. Control: the intuitive, easy to use Fanuc 310i-A.
Related Glossary Terms
- ceramics
ceramics
Cutting tool materials based on aluminum oxide and silicon nitride. Ceramic tools can withstand higher cutting speeds than cemented carbide tools when machining hardened steels, cast irons and high-temperature alloys.
- computer numerical control ( CNC)
computer numerical control ( CNC)
Microprocessor-based controller dedicated to a machine tool that permits the creation or modification of parts. Programmed numerical control activates the machine’s servos and spindle drives and controls the various machining operations. See DNC, direct numerical control; NC, numerical control.
- cylindrical grinding
cylindrical grinding
Grinding operation in which the workpiece is rotated around a fixed axis while the grinding wheel is fed into the outside surface in controlled relation to the axis of rotation. The workpiece is usually cylindrical, but it may be tapered or curvilinear in profile. See centerless grinding; grinding.
- grinding
grinding
Machining operation in which material is removed from the workpiece by a powered abrasive wheel, stone, belt, paste, sheet, compound, slurry, etc. Takes various forms: surface grinding (creates flat and/or squared surfaces); cylindrical grinding (for external cylindrical and tapered shapes, fillets, undercuts, etc.); centerless grinding; chamfering; thread and form grinding; tool and cutter grinding; offhand grinding; lapping and polishing (grinding with extremely fine grits to create ultrasmooth surfaces); honing; and disc grinding.
- grinding machine
grinding machine
Powers a grinding wheel or other abrasive tool for the purpose of removing metal and finishing workpieces to close tolerances. Provides smooth, square, parallel and accurate workpiece surfaces. When ultrasmooth surfaces and finishes on the order of microns are required, lapping and honing machines (precision grinders that run abrasives with extremely fine, uniform grits) are used. In its “finishing” role, the grinder is perhaps the most widely used machine tool. Various styles are available: bench and pedestal grinders for sharpening lathe bits and drills; surface grinders for producing square, parallel, smooth and accurate parts; cylindrical and centerless grinders; center-hole grinders; form grinders; facemill and endmill grinders; gear-cutting grinders; jig grinders; abrasive belt (backstand, swing-frame, belt-roll) grinders; tool and cutter grinders for sharpening and resharpening cutting tools; carbide grinders; hand-held die grinders; and abrasive cutoff saws.
- grinding wheel
grinding wheel
Wheel formed from abrasive material mixed in a suitable matrix. Takes a variety of shapes but falls into two basic categories: one that cuts on its periphery, as in reciprocating grinding, and one that cuts on its side or face, as in tool and cutter grinding.
- inner diameter ( ID)
inner diameter ( ID)
Dimension that defines the inside diameter of a cavity or hole. See OD, outer diameter.