Contact Details
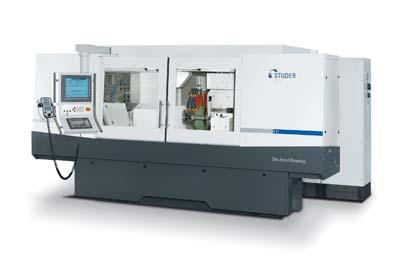
United Grinding Technologies announces the new Studer S41 CNC universal cylindrical grinder, featuring outstanding technology and cost-effectiveness. The machine grinds with superior precision and at extreme metal removal rates. In addition, the longitudinal and cross slide, as well as the swivel axis for the wheelhead, feature electric direct drives, which move to the working position very swiftly and precisely.
Higher precision, better surface quality, higher metal removal rates, these are the constantly increasing requirements made by the market. In addressing these requirements, UGT has again set the standard with its new S41 CNC universal cylindrical grinder. The developers based the new grinder on a predecessor machine proven worldwide over many years, while adding a number of outstanding design features. It works more quickly and precisely, offers a broader range of applications, with production options that are highly attractive with regard to cost-effectiveness. By saving on auxiliary times, the S41 considerably shortens the cycle times of the grinding process.
The Granitan S103 machine bed provides a very solid, rigid and thermally stable S41. The formula of this mineral casting is designed for optimal grinding operation conditions. Thus, the machine bed literally provides the integrated guide system with a stable basis for absorbing the high forces that occur during grinding with high metal removal rates.
Thanks to its remarkable thermal behavior, the machine bed largely equalizes brief variations in temperature, so that the machine operates with consistently high precision even with changing ambient temperatures. Its high rigidity and excellent damping provide the basic prerequisites for outstanding surface quality of ground parts and long grinding wheel lifetimes. The guideways of both the longitudinal slide and the cross slide are molded directly into the machine bed. To ensure that the high forces that occur during grinding with high metal removal rates are optimally absorbed into the machine bed, the guideways have a larger spacing.
The new StuderGuide guideway system ensures high precision of the longitudinal and cross slides when both stationary and during movement. The StuderGuide system uses the advantages of hydrostatic and hydrodynamic guide systems and avoids the slip-stick effect or floating of the slide. Also contributing to the machine's high precision is the fact that the solid gray cast iron longitudinal and cross slides rest completely on the guideways over the entire travel. With this maintenance-free guide system, UGT guarantees a straightness of less than 0.0001" over a measured length of 37.4".
The longitudinal slide (Z-axis) has a ground work table which carries the workhead and tailstock as well as additional accessories and devices. A ground T-slot over the entire length of the guideway enables optimal positioning of dressing tools. The cross slide (X-axis) supports the wheelhead. Longitudinal and cross slides are moved by linear direct drives and, with up to 66 ft per minute, achieve four times higher travel speeds and axis system resolutions of ten nanometers. This enables high-precision and highly efficient grinding, as well as making a huge contribution to reducing auxiliary times.
The swivel movement of the turret wheelhead (B-axis) is also by a direct drive. It swivels the turret wheelhead around three times faster (less than 3 sec) and positions the new grinding wheels in a much shorter time with a positioning resolution of 0.00005 degrees. The positioning is therefore twice as precise as with the predecessor machine. The elimination of the Hirth gear, which fixed the wheelhead in position on the predecessor machine, also contributes to faster positioning. When swiveling in a new grinding wheel it is no longer necessary to lift the turret wheelhead out of the Hirth gear and then to engage it again by lowering it. The time required for fine adjustment after engaging in the Hirth gear is also saved. This new concept makes a considerable contribution to saving on auxiliary times, particularly when the workpiece grinding process requires frequent swiveling-in of different wheels. In addition to the considerable increases in working speed and precision, the S41 also has a number of advantageous characteristics which enable the user to cover an extended workpiece range, and thus a broader market range.
For instance, the height of centers on the standard version has been increased to 8.9". The machine is also optionally available with a height of centers of 10.8"; this is not achieved by means of distance plates, but by making the workheads higher. The maximum distance between centers is 39.4" on the standard machine, but a machine variant with a distance between centers of 63" is also available. Thanks to the greater heights of centers and distances between centers, workpieces with weights of up to 551 lb. can now also be machined. The machine is equipped with a hydraulically clamped tailstock for the heavier workpieces.
Up to four external grinding wheels or three internal grinding spindles enable over 30 grinding head combinations. The grinding wheels are no longer driven by belt drives, but by motor spindles. The machine can also be equipped with motor spindles for high speed grinding (HSG). Internal grinding spindles with speeds from 6000 to 120,000 rpm can be used. Automatic balancing systems and frequency converters for each external grinding spindle allow the grinding process to be specifically matched to the respective conditions of use. Wheelhead variants are also available with a vertical spindle for grinding keyways or with a traverse grinding axis for traverse grinding of internal tapers. Fatigue-free working and straightforward machine operation are important components for consistently high quality. For this reason, optimized ergonomics were one of the developers' priorities. For instance, hoses and cables have largely disappeared from the work area of the machine. Grinding wheel change is performed with a single Allen wrench, and a special small crane is integrated into the machine, so that heavier grinding wheels do not have to be lifted manually.
The Fanuc 31i-A machine control with integrated PC operates with the StuderGRIND software specially developed for the grinding processes, and the StuderWIN operator interface. A 15" touch screen and ergonomically arranged controls are available to the grinder for communication with the control system and for programming. An additional manual control unit facilitates setup of the grinding processes. The convenient electronic cut-in detection facilitates operation and contributes to increasing precision and reducing auxiliary times. The software also contains tools for programming form and contour grinding processes, and enables offline programming of grinding processes as well as the determination of important basic cycle data to give the user a good basis to quote grinding tasks to his customers. A free-standing operating panel with adjustable height is also available.
UGT considers itself a partner for the customer in the design of technically and economically optimized grinding processes. The efficient grinding of workpieces requires process-optimized complete solutions. This includes an integrated quality control system based on continuous measurement, re-measurement, recording and correction. In addition, grinding of workpieces with modular peripheral equipment such as loading/unloading systems can be seamlessly integrated into the complete production process. The automation systems of the peripheral equipment communicate with the S41 by means of standard interfaces, so that even complex handling tasks can be carried out.
Related Glossary Terms
- centers
centers
Cone-shaped pins that support a workpiece by one or two ends during machining. The centers fit into holes drilled in the workpiece ends. Centers that turn with the workpiece are called “live” centers; those that do not are called “dead” centers.
- computer numerical control ( CNC)
computer numerical control ( CNC)
Microprocessor-based controller dedicated to a machine tool that permits the creation or modification of parts. Programmed numerical control activates the machine’s servos and spindle drives and controls the various machining operations. See DNC, direct numerical control; NC, numerical control.
- dressing
dressing
Removal of undesirable materials from “loaded” grinding wheels using a single- or multi-point diamond or other tool. The process also exposes unused, sharp abrasive points. See loading; truing.
- grinding
grinding
Machining operation in which material is removed from the workpiece by a powered abrasive wheel, stone, belt, paste, sheet, compound, slurry, etc. Takes various forms: surface grinding (creates flat and/or squared surfaces); cylindrical grinding (for external cylindrical and tapered shapes, fillets, undercuts, etc.); centerless grinding; chamfering; thread and form grinding; tool and cutter grinding; offhand grinding; lapping and polishing (grinding with extremely fine grits to create ultrasmooth surfaces); honing; and disc grinding.
- grinding wheel
grinding wheel
Wheel formed from abrasive material mixed in a suitable matrix. Takes a variety of shapes but falls into two basic categories: one that cuts on its periphery, as in reciprocating grinding, and one that cuts on its side or face, as in tool and cutter grinding.
- quality assurance ( quality control)
quality assurance ( quality control)
Terms denoting a formal program for monitoring product quality. The denotations are the same, but QC typically connotes a more traditional postmachining inspection system, while QA implies a more comprehensive approach, with emphasis on “total quality,” broad quality principles, statistical process control and other statistical methods.