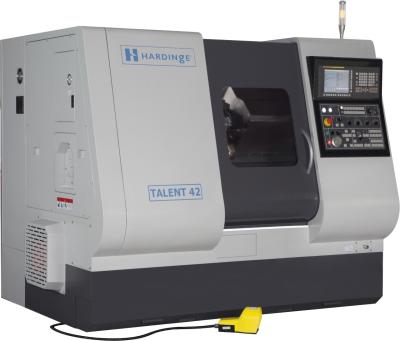
Hardinge Inc. announces the release of their newest family of CNC Turning Centers, the TALENT 42 and 51. The Hardinge TALENT series machines reportedly offer an exceptional combination of features for accuracy, flexibility, and durability in a compact design.
The unique collet-ready main and subspindle design will increase part accuracy and improve surface finish. The TALENT series offer’s two separate base structures (short and standard bed lengths). It features a robust one-piece cast iron base, heavy-duty roller linear guideways and ball screws. The many standard value-added features include through-tool and headwall air/coolant for both main and subspindles, foot switches, chip conveyor interface, bar feed interface, air hose with an air gun. These machines feature the Fanuc OiTF CNC, which includes many value-added features.
The series is available with a variety of options including:
- Live Tooling
- Y-Axis
- Servo Tailstock
- Subspindle
- Parts Catcher
- Chip Conveyor
- Bar Feeds
Contact Details
Related Glossary Terms
- centers
centers
Cone-shaped pins that support a workpiece by one or two ends during machining. The centers fit into holes drilled in the workpiece ends. Centers that turn with the workpiece are called “live” centers; those that do not are called “dead” centers.
- computer numerical control ( CNC)
computer numerical control ( CNC)
Microprocessor-based controller dedicated to a machine tool that permits the creation or modification of parts. Programmed numerical control activates the machine’s servos and spindle drives and controls the various machining operations. See DNC, direct numerical control; NC, numerical control.
- feed
feed
Rate of change of position of the tool as a whole, relative to the workpiece while cutting.
- turning
turning
Workpiece is held in a chuck, mounted on a face plate or secured between centers and rotated while a cutting tool, normally a single-point tool, is fed into it along its periphery or across its end or face. Takes the form of straight turning (cutting along the periphery of the workpiece); taper turning (creating a taper); step turning (turning different-size diameters on the same work); chamfering (beveling an edge or shoulder); facing (cutting on an end); turning threads (usually external but can be internal); roughing (high-volume metal removal); and finishing (final light cuts). Performed on lathes, turning centers, chucking machines, automatic screw machines and similar machines.