Contact Details
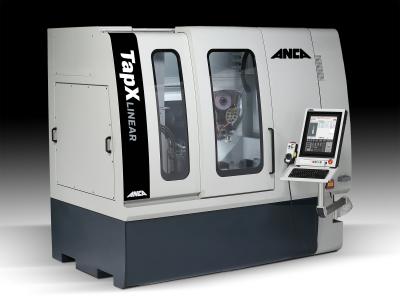
Projected global demand for products such as taps, dies, and thread forming tools is anticipated to rise from 2.75 billion to 3.42 billion over the next five years, with a compound annual growth rate (CAGR) of 5%. The high-tech industries, particularly automotive and aerospace sectors, are expected to sustain a significant portion of this growth, accounting for 16% of the overall market demand. Additionally, there is an expected increase in demand from medical applications, which is projected to contribute another 7% to the total market share within the next five years.
Given the impetus from these high-tech markets, tap producers will need to enhance their designs to meet the escalating market share of specialized materials. Notably, composites (expected CAGR of 8.5%) and super alloys (expected CAGR of 7.5%) are anticipated to experience the most substantial growth, necessitating the development of tailored designs in response.
With the boom of automotive and aerospace applications, ANCA sees great potential for the future of the high-end tap market. ANCA’s years of experience working with tap manufacturers has given the company valuable insights into the industry challenges, making it well-equipped to offer the right solution. The TapX is a machine specifically designed and integrated with automation to ensure high productivity in mass production. As a one-machine solution with single clamping, it guarantees substantial benefits for manufacturing standard and special taps by eliminating the traditional requirement of needing several grinding machines.
Flexible, precise and efficient one-stop tap grinding is simply unimaginable on ordinary grinding machines, as high-speed steel taps, carbide taps, micro taps and non-standard taps require different and detailed solutions. The difference lies in the performance of a single grinding process, a parallel grinding process or a combined grinding process. In addition, several grinding machines are usually required, each performing a specific tap grinding task. TapX integrates the various processes into one machine.
Flexibility is a key feature of the tap grinding process on the TapX. The specially designed machine and powerful ToolRoom software ensure a vast range of tap types and sizes can be designed and manufactured in one set-up. Combine this with the benefits of quick changeover time and it's not hard to see how TapX can increase productivity and reduce lead times.
The production of taps in different materials is an example of how this highly flexible solution can contribute to productivity. Taps are mainly made of HSS and carbide materials, which require high precision, surface finish and reliability for grinding. TapX is suitable for the complete production of HSS or carbide taps. With a single set-up, it can grind various types of standard taps, micro taps and non-standard taps. Its excellent rigidity guarantees repeatable, high-quality results, while its CNC control plus programmable force of the center ensures reliability of high frequency movements.
The TapX uses ANCA’s own LinX motor technology for all linear axes and direct drive technology for all rotary axes. By eliminating all belts, pulleys, and gears, the TapX is not only a more precise machine, but a more reliable one as well.
Although HSS will remain the dominant material of choice, carbide tools are growing in popularity with the increase in thread milling applications and introduction of more exotic materials. Compared with HSS, carbide offers high rigidity, good machining quality and long service life. Consequently, the production of carbide taps presents challenges for machine productivity, accuracy and dressing of special thread grinding wheels.
TapX offers the perfect solution with its single clamping to optimize the grinding process. Combined with greater flexibility in wheel selection and process deployment, this revolutionary solution means more flexibility, reduced costs and increased tap production output. The total set-up time for multiple general machines is reduced from three to four hours to one hour for one TapX machine, which significantly reduces lead time for small to medium batch production, urgent order response and customer changes. In recent years, ANCA continues to innovate and has developed a unique solution for dome carbide taps with a wider application. Its superior performance is unmatched in the industry.
Recognizing the efficiency, accuracy and reusability of TapX, customers have begun to expand their product range to include spiral, straight flute and forming taps, and even micro parts. Micro taps are mostly used in smartphones, glasses, consumer electronics, aviation and military industries. Any miniaturized part may be machined with a small or micro tap.
In recent years, the growing demand for mobile devices and new materials has led to a sharp increase in the consumption of thread tapping tools, which in turn resulted in an unprecedented boom for machines grinding small or micro taps. This means that manufacturers such as ANCA, who have the capability to manufacture these tools, have great potential to meet the ever-growing market demand. To grind small batches of taps, conventional machines simply take too long to set up. With ANCA TapX, customers can integrate the entire process into just one machine, significantly increasing productivity through rapid tap design, set-up and changeover.
The TapX grinding solution is an excellent option to meet the high demand for high-quality tap products or to fulfill the needs of emerging manufacturers in the market. The TapX one-machine grinding concept provides faster tap design, set-up, and changeover to reduce lead times and boost competitiveness. Gone are the high costs, inflexible production and low productivity due to lengthy machine set-ups. ANCA remains committed to offering comprehensive grinding solutions for its customers.
Related Glossary Terms
- alloys
alloys
Substances having metallic properties and being composed of two or more chemical elements of which at least one is a metal.
- composites
composites
Materials composed of different elements, with one element normally embedded in another, held together by a compatible binder.
- computer numerical control ( CNC)
computer numerical control ( CNC)
Microprocessor-based controller dedicated to a machine tool that permits the creation or modification of parts. Programmed numerical control activates the machine’s servos and spindle drives and controls the various machining operations. See DNC, direct numerical control; NC, numerical control.
- dressing
dressing
Removal of undesirable materials from “loaded” grinding wheels using a single- or multi-point diamond or other tool. The process also exposes unused, sharp abrasive points. See loading; truing.
- gang cutting ( milling)
gang cutting ( milling)
Machining with several cutters mounted on a single arbor, generally for simultaneous cutting.
- grinding
grinding
Machining operation in which material is removed from the workpiece by a powered abrasive wheel, stone, belt, paste, sheet, compound, slurry, etc. Takes various forms: surface grinding (creates flat and/or squared surfaces); cylindrical grinding (for external cylindrical and tapered shapes, fillets, undercuts, etc.); centerless grinding; chamfering; thread and form grinding; tool and cutter grinding; offhand grinding; lapping and polishing (grinding with extremely fine grits to create ultrasmooth surfaces); honing; and disc grinding.
- high-speed steels ( HSS)
high-speed steels ( HSS)
Available in two major types: tungsten high-speed steels (designated by letter T having tungsten as the principal alloying element) and molybdenum high-speed steels (designated by letter M having molybdenum as the principal alloying element). The type T high-speed steels containing cobalt have higher wear resistance and greater red (hot) hardness, withstanding cutting temperature up to 1,100º F (590º C). The type T steels are used to fabricate metalcutting tools (milling cutters, drills, reamers and taps), woodworking tools, various types of punches and dies, ball and roller bearings. The type M steels are used for cutting tools and various types of dies.
- milling
milling
Machining operation in which metal or other material is removed by applying power to a rotating cutter. In vertical milling, the cutting tool is mounted vertically on the spindle. In horizontal milling, the cutting tool is mounted horizontally, either directly on the spindle or on an arbor. Horizontal milling is further broken down into conventional milling, where the cutter rotates opposite the direction of feed, or “up” into the workpiece; and climb milling, where the cutter rotates in the direction of feed, or “down” into the workpiece. Milling operations include plane or surface milling, endmilling, facemilling, angle milling, form milling and profiling.
- parallel
parallel
Strip or block of precision-ground stock used to elevate a workpiece, while keeping it parallel to the worktable, to prevent cutter/table contact.
- tap
tap
Cylindrical tool that cuts internal threads and has flutes to remove chips and carry tapping fluid to the point of cut. Normally used on a drill press or tapping machine but also may be operated manually. See tapping.
- tapping
tapping
Machining operation in which a tap, with teeth on its periphery, cuts internal threads in a predrilled hole having a smaller diameter than the tap diameter. Threads are formed by a combined rotary and axial-relative motion between tap and workpiece. See tap.