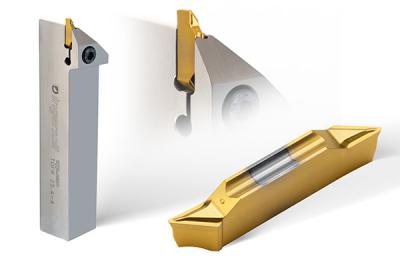
Ingersoll introduces the V-type T-CLAMP insert that maximizes productivity by minimizing tool change through multifunctional machining.
In addition to operating on narrow grooving on typical CNC lathes, the new V-shaped TDMV inserts are suitable with a wide range of applications on Swiss automatic lathes, with a concentration on miniature product machining. The V-shaped TDMV insert line is a multi-purpose option and the optimal tool for innovation in the groove machining segment in order to meet various customers’ needs.
Features & Benefits
-
Versatile chip breaker: forward/backward turning, profiling, end facing and parting
-
Optimized chip breaker design for bi-directional turning enables superior chip control
-
Insert’s 2.8 mm edge width allows for a variety of tasks in tight spaces
-
Roughing and finishing capable with a cutting depth of up to 2.5 mm
-
Available in 4 insert types: R/L-handed, Corner R0.2, R0.4
-
Multi-application machining reduces tool cost and equipment downtime while maximizing productivity gains
-
Compatible with standard TGFR/L holders, maximizing performance when using internal high-pressure feed-type holders
Contact Details
Related Glossary Terms
- computer numerical control ( CNC)
computer numerical control ( CNC)
Microprocessor-based controller dedicated to a machine tool that permits the creation or modification of parts. Programmed numerical control activates the machine’s servos and spindle drives and controls the various machining operations. See DNC, direct numerical control; NC, numerical control.
- grooving
grooving
Machining grooves and shallow channels. Example: grooving ball-bearing raceways. Typically performed by tools that are capable of light cuts at high feed rates. Imparts high-quality finish.
- parting
parting
When used in lathe or screw-machine operations, this process separates a completed part from chuck-held or collet-fed stock by means of a very narrow, flat-end cutting, or parting, tool.
- profiling
profiling
Machining vertical edges of workpieces having irregular contours; normally performed with an endmill in a vertical spindle on a milling machine or with a profiler, following a pattern. See mill, milling machine.
- turning
turning
Workpiece is held in a chuck, mounted on a face plate or secured between centers and rotated while a cutting tool, normally a single-point tool, is fed into it along its periphery or across its end or face. Takes the form of straight turning (cutting along the periphery of the workpiece); taper turning (creating a taper); step turning (turning different-size diameters on the same work); chamfering (beveling an edge or shoulder); facing (cutting on an end); turning threads (usually external but can be internal); roughing (high-volume metal removal); and finishing (final light cuts). Performed on lathes, turning centers, chucking machines, automatic screw machines and similar machines.