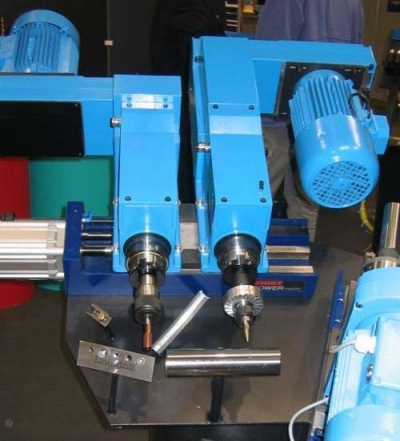
Screw unions on thin walled materials require complex additional operations like e.g. the welding on of a nut. The so called flow drilling process can form the thread directly in the arising passage, thereby making this additional operation unnecessary. Suhner and Flowdrill are collaborating in this field of specialized technology. Thermal flow drilling uses a Flowdrill-tool to produce passages several times the thickness of the thin walled material.
Core drilled holes formed with this method are essentially more precise than threads formed with conventional means. Moreover, this process, by forming the existing workpiece, saves time and material.
Flow drilling is based on a combination of axial force and relatively high speed that generates local heat through friction. This friction heat and high surface pressure cause the material to undergo plastic deformation. The special geometry of the tool and its special hard metal allow it to pass through the material in one operation.
In contrast to other processes, flow drilling induces material hardening for high tightening torques in threads and large load bearing capacities in bearing bushes. Flow drilling tools are available for diameters of 1.5–46.0 mm.
Suhner can offer for this work a range of drilling units with various feeding systems. The classical flow drilling units are the BEM 12 and the BEM 20, each with pneumohydraulic feed, i.e. a pneumatic feed regulated with a hydraulic cushioning cylinder. Pictured is a typical application where after flow drilling with the machining unit BEM 20, the thread is formed with the GEM 20 unit.
The following series of operations are implemented in practice.
1. The spindle moves the rotating flow drill in rapid traverse directly in front of the workpiece.
2. Now under regulated, but still rapid feed, the tool tip contacts the workpiece.
3. Under the action of friction, the material glows and starts to flow.
4. The feed movement, first obstructed by the contact, now continues, i.e. the spindle presses the flow drill through
the material. The characteristic collar is formed.
With this method, the flow process defines the spindle's feed movement.
The alternative to the pneumatic machining unit takes the form of CNC units. In this case, Suhner offers with its BEA 25 CNC, a machining unit with integrated recirculating ball screw and servomotor drive. With this process, CNC programming can optimize the sequences named above to the tool and workpiece.
In contrast to conventional thread cutting, thread forming in connection with flow drilling presents huge advantages.
The preceding warm displacement of material during flow drilling and the subsequent cold rolling during thread forming cause the material to undergo intense hardening. This results in threaded connections with high pullout strengths.
The chipless thread former can work at essentially higher speeds and exhibits an extremely long service life for enhanced productivity.
Owing to the displacement the material is forced to flow. This gives rise to a compressed thread profile.
When the threads are formed, their highest points are pressed into the material. The material is deformed and flows into the gaps between the thread former's teeth.
Advantages of thread forming at a glance:
● No chips
● Thread depths up to 4xD possible
● Essentially lower roughness height in the thread flanks than with thread cutting
● Approx 20 percent greater pullout strength under static load
● More than double the fatigue limit under dynamic load
● Thread formers not liable to break, so maximized machining reliability
● Considerably higher service life than taps, particularly when thread pitches ≤ 1.5 mm
● Approx 65 percent of all industrial machined materials can be formed: steel up to 1200 N/mm², stainless and acid-resistant steel, copper and copper alloys, aluminium and aluminium alloys.
Contact Details
Related Glossary Terms
- alloys
alloys
Substances having metallic properties and being composed of two or more chemical elements of which at least one is a metal.
- axial force
axial force
When drilling, a force that is directed axially—along the direction of machining. The magnitude of an axial force rises with the drill’s diameter and the chisel edge’s width. Axial force is also known as thrust. When turning and boring, the term “feed force” is commonly used instead of “axial force.” See cutting force.
- computer numerical control ( CNC)
computer numerical control ( CNC)
Microprocessor-based controller dedicated to a machine tool that permits the creation or modification of parts. Programmed numerical control activates the machine’s servos and spindle drives and controls the various machining operations. See DNC, direct numerical control; NC, numerical control.
- copper alloys
copper alloys
Copper containing specified quantities of alloying elements added to obtain the necessary mechanical and physical properties. The most common copper alloys are divided into six groups, and each group contains one of the following major alloying elements: brasses—major alloying element is zinc; phosphor bronzes—major alloying element is tin; aluminum bronzes—major alloying element is aluminum; silicon bronzes—major alloying element is silicon; copper-nickels and nickel-silvers—major alloying element is nickel; and dilute-copper or high-copper alloys, which contain small amounts of various elements such as beryllium, cadmium, chromium or iron.
- fatigue
fatigue
Phenomenon leading to fracture under repeated or fluctuating stresses having a maximum value less than the tensile strength of the material. Fatigue fractures are progressive, beginning as minute cracks that grow under the action of the fluctuating stress.
- feed
feed
Rate of change of position of the tool as a whole, relative to the workpiece while cutting.
- hardening
hardening
Process of increasing the surface hardness of a part. It is accomplished by heating a piece of steel to a temperature within or above its critical range and then cooling (or quenching) it rapidly. In any heat-treatment operation, the rate of heating is important. Heat flows from the exterior to the interior of steel at a definite rate. If the steel is heated too quickly, the outside becomes hotter than the inside and the desired uniform structure cannot be obtained. If a piece is irregular in shape, a slow heating rate is essential to prevent warping and cracking. The heavier the section, the longer the heating time must be to achieve uniform results. Even after the correct temperature has been reached, the piece should be held at the temperature for a sufficient period of time to permit its thickest section to attain a uniform temperature. See workhardening.
- plastic deformation
plastic deformation
Permanent (inelastic) distortion of metals under applied stresses that strain the material beyond its elastic limit.
- rapid traverse
rapid traverse
Movement on a CNC mill or lathe that is from point to point at full speed but, usually, without linear interpolation.