Contact Details
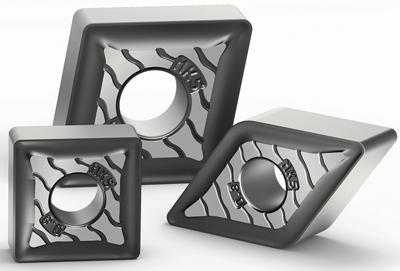
Walter USA LLC has added two new geometries to its line of high-performance Tiger-tec Silver inserts. Tiger-tec Silver, with its advanced CVD coating, is designed to enhance cutting speed, reliability and tool life, and the new RK5 and RK7 geometries bring these advantages to the machining of ISO K (cast iron) materials and join the MK5 universal geometry already available, according to the company.
A key feature of the new geometries is their plateau step between the location face and the cutting edge. This step enables the location face to be ground after coating, something that is not possible to do with standard inserts without a chipbreaker groove. The resulting uneven location face on standard inserts can lead to micro-vibrations and chipping at the cutting edge. By contrast, the evenly ground faces of the new Walter inserts ensures that they can be seated with maximum stability. As a result, cutting-edge wear is reduced, tool life enhanced, and process reliability increased, particularly in cases of high dynamic loads.
The RK5 ("classic") for cast iron roughing operations is a classic flat top insert without chipgroove and delivers the advantages of speed, reliability and longer tool life, particularly in the machining of grey cast iron. RK7 ("robust") is an extremely robust insert for very heavy interrupted cuts, large depth-of-cut variations causing uneven material removal, and hard cast skin. Its geometry is similar to the RK5's, but it also has a protective chamfer on the cutting edge. It is also suitable for the hard/soft machining of hardened steels with hardness from 40-62 HRC, for which CBN inserts are not suitable in many cases. The existing Walter MK5 ("universal") geometry is suitable for medium machining of all cast iron workpieces. It has an open chipbreaker groove for a soft cutting action, and is especially well suited for machining ductile cast iron, unstable components, or internal machining with low cutting pressure.
Enhancing the performance advantages of the new geometries are two Tiger-tec Silver grades, WKK10S and WKK20S, both of which can be used on grey cast iron, ductile cast iron and compacted graphite cast iron (CGI). WKK10S is the harder of the two, with high wear resistance and high cutting speed. It is primarily used for grey cast iron and is suitable for continuous cuts through to light interrupted cuts, and excels in dry machining. WKK20S, a universal cutting grade, is suitable for around 50 percent of all tasks, can be used for both wet and dry machining, and offers high process reliability particularly for workpieces with interrupted cuts, cast skin or cross holes. Ductile cast iron is its primary application.
Related Glossary Terms
- chemical vapor deposition ( CVD)
chemical vapor deposition ( CVD)
High-temperature (1,000° C or higher), atmosphere-controlled process in which a chemical reaction is induced for the purpose of depositing a coating 2µm to 12µm thick on a tool’s surface. See coated tools; PVD, physical vapor deposition.
- chipbreaker
chipbreaker
Groove or other tool geometry that breaks chips into small fragments as they come off the workpiece. Designed to prevent chips from becoming so long that they are difficult to control, catch in turning parts and cause safety problems.
- cubic boron nitride ( CBN)
cubic boron nitride ( CBN)
Crystal manufactured from boron nitride under high pressure and temperature. Used to cut hard-to-machine ferrous and nickel-base materials up to 70 HRC. Second hardest material after diamond. See superabrasive tools.
- cutting speed
cutting speed
Tangential velocity on the surface of the tool or workpiece at the cutting interface. The formula for cutting speed (sfm) is tool diameter 5 0.26 5 spindle speed (rpm). The formula for feed per tooth (fpt) is table feed (ipm)/number of flutes/spindle speed (rpm). The formula for spindle speed (rpm) is cutting speed (sfm) 5 3.82/tool diameter. The formula for table feed (ipm) is feed per tooth (ftp) 5 number of tool flutes 5 spindle speed (rpm).
- flat ( screw flat)
flat ( screw flat)
Flat surface machined into the shank of a cutting tool for enhanced holding of the tool.
- hardness
hardness
Hardness is a measure of the resistance of a material to surface indentation or abrasion. There is no absolute scale for hardness. In order to express hardness quantitatively, each type of test has its own scale, which defines hardness. Indentation hardness obtained through static methods is measured by Brinell, Rockwell, Vickers and Knoop tests. Hardness without indentation is measured by a dynamic method, known as the Scleroscope test.
- wear resistance
wear resistance
Ability of the tool to withstand stresses that cause it to wear during cutting; an attribute linked to alloy composition, base material, thermal conditions, type of tooling and operation and other variables.