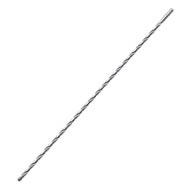
Walter USA LLC has introduced the Walter Titex XD70, a solid carbide drill that employs design and manufacturing innovations that bring new levels of productivity to the drilling of extremely deep holes.
The Walter Titex XD70 (the XD designation stands for "extremely deep") can produce holes up to a remarkable 70xD in one operation, and does not require pecking. Previous XD technology product offerings topped out at 30xD.
Along with its design, manufacturing innovations have contributed to the 70xD's increase in performance. Walter is using a new method of producing solid carbide blanks, making it possible to efficiently manufacture this type of long solid carbide drill. In addition, a special grinding process is also employed.
As is the case with all XD drills, cooling for the XD70 is provided via internal coolant channels. However, despite the great drilling depth, no special coolant equipment, such as an external high-pressure system, is required.
A standard cooling unit, such as those available with any machining center, is sufficient. The XD70 technology is currently being offered as a special tool, in diameters ranging from 5 to 12mm. Two tip coatings are available depending on the workpiece material: TTP for steels and XPL for cast iron.
Contact Details
Related Glossary Terms
- coolant
coolant
Fluid that reduces temperature buildup at the tool/workpiece interface during machining. Normally takes the form of a liquid such as soluble or chemical mixtures (semisynthetic, synthetic) but can be pressurized air or other gas. Because of water’s ability to absorb great quantities of heat, it is widely used as a coolant and vehicle for various cutting compounds, with the water-to-compound ratio varying with the machining task. See cutting fluid; semisynthetic cutting fluid; soluble-oil cutting fluid; synthetic cutting fluid.
- grinding
grinding
Machining operation in which material is removed from the workpiece by a powered abrasive wheel, stone, belt, paste, sheet, compound, slurry, etc. Takes various forms: surface grinding (creates flat and/or squared surfaces); cylindrical grinding (for external cylindrical and tapered shapes, fillets, undercuts, etc.); centerless grinding; chamfering; thread and form grinding; tool and cutter grinding; offhand grinding; lapping and polishing (grinding with extremely fine grits to create ultrasmooth surfaces); honing; and disc grinding.
- machining center
machining center
CNC machine tool capable of drilling, reaming, tapping, milling and boring. Normally comes with an automatic toolchanger. See automatic toolchanger.