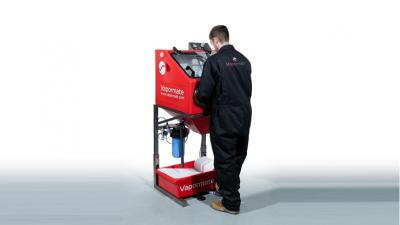
Based in the UK, Vapormatt specialize in wet-blasting systems for several different industries. Having invented the first wet blasting machine back in the 1940’s they remain leaders in the technology thanks to continued investment in R&D.
The company’s Tiger system has firmly established itself as the gold standard for cutting tool insert finishing, with installations in many of the world’s leading cutting tool insert manufacturers.
The system can be configured to process inserts for all essential pre-coating, edge honing or post-coating operations, including:
- Cleaning to a uniform RA and to HF1 level of cleanliness for optimum coating adhesion
- Creation of highly reactive surfaces with high surface energies for optimum coating adhesion
- Cobalt skin removal without the creation of hazardous cobalt dust
- Honing of the cutting edge to a specific radius to prevent ‘chipping’ of the cutting edge, allowing the tool to be run at full speed from new
- Honing to a specific K-Factor ranging from ‘trumpet’ to ‘waterfall’ hones for optimum cutting performance and durability
- Post coating finishing to remove coating imperfections, like coating droplets, to leave a uniform aesthetic surface with an optimum RA for efficient operation in use
- Post coating peening to convert tensile stress in the coating to compressive stress, producing the strain hardening that dramatically improves a coatings durability
- Selective coating removal to reveal the correct coating for the required task, for example one layer might be thermally conductive, whilst another is wear resistant.
Wet blasting is the only surface finishing technology capable of carrying out all these operations repeatedly and to a consistently high standard.
Whilst the Tiger and Tiger + systems cater to the world’s largest insert manufacturers; the company also produces a range of systems to suit medium and small manufacturers too.
Contact Details
Related Glossary Terms
- hardening
hardening
Process of increasing the surface hardness of a part. It is accomplished by heating a piece of steel to a temperature within or above its critical range and then cooling (or quenching) it rapidly. In any heat-treatment operation, the rate of heating is important. Heat flows from the exterior to the interior of steel at a definite rate. If the steel is heated too quickly, the outside becomes hotter than the inside and the desired uniform structure cannot be obtained. If a piece is irregular in shape, a slow heating rate is essential to prevent warping and cracking. The heavier the section, the longer the heating time must be to achieve uniform results. Even after the correct temperature has been reached, the piece should be held at the temperature for a sufficient period of time to permit its thickest section to attain a uniform temperature. See workhardening.
- peening
peening
Mechanical working of a metal by hammer blows or shot impingement.
- strain hardening
strain hardening
Increase in hardness and strength caused by plastic deformation at temperatures below the recrystallization range.