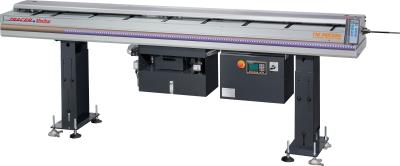
The new TRACER 12' Minibar hydrodynamic magazine bar feeder from CNC Indexing & Feeding Technologies is engineered to feed bar stock diameters from 0.8mm to 12mm and up to 12' in length. The economical and efficient TRACER 12' Minibar feeder provides a solution for manufacturers with fixed headstock and Swiss-type CNC lathes who need to feed large quantities of small-diameter bar stock efficiently.
An operator can quickly adjust the bar feeder for different stock sizes without using tools. Fast changes of guide channel sets increase throughput and minimize changeover and setup times. Torque force and speed are easily adjustable, permitting smaller stock to be fed consistently.
Workhandling products from CNC Indexing & Feeding Technologies include a selection of productivity-boosting TRACER magazine bar feeders and short bar loaders, AUTOLOAD automatic gantry loading systems, and TJR rotary tables.
Jessica Presutto, national sales manager of CNC Indexing & Feeding Technologies, said, “The TRACER 12' Minibar feeder is designed to give Swiss lathe users the ability to feed bar stock smaller than 13mm in diameter at an economical price. We’re excited to be able add a new product to our a wide variety of hydrodynamic magazine bar feeders for the production turning industry.”
Contact Details
Related Glossary Terms
- computer numerical control ( CNC)
computer numerical control ( CNC)
Microprocessor-based controller dedicated to a machine tool that permits the creation or modification of parts. Programmed numerical control activates the machine’s servos and spindle drives and controls the various machining operations. See DNC, direct numerical control; NC, numerical control.
- feed
feed
Rate of change of position of the tool as a whole, relative to the workpiece while cutting.
- lathe
lathe
Turning machine capable of sawing, milling, grinding, gear-cutting, drilling, reaming, boring, threading, facing, chamfering, grooving, knurling, spinning, parting, necking, taper-cutting, and cam- and eccentric-cutting, as well as step- and straight-turning. Comes in a variety of forms, ranging from manual to semiautomatic to fully automatic, with major types being engine lathes, turning and contouring lathes, turret lathes and numerical-control lathes. The engine lathe consists of a headstock and spindle, tailstock, bed, carriage (complete with apron) and cross slides. Features include gear- (speed) and feed-selector levers, toolpost, compound rest, lead screw and reversing lead screw, threading dial and rapid-traverse lever. Special lathe types include through-the-spindle, camshaft and crankshaft, brake drum and rotor, spinning and gun-barrel machines. Toolroom and bench lathes are used for precision work; the former for tool-and-die work and similar tasks, the latter for small workpieces (instruments, watches), normally without a power feed. Models are typically designated according to their “swing,” or the largest-diameter workpiece that can be rotated; bed length, or the distance between centers; and horsepower generated. See turning machine.
- turning
turning
Workpiece is held in a chuck, mounted on a face plate or secured between centers and rotated while a cutting tool, normally a single-point tool, is fed into it along its periphery or across its end or face. Takes the form of straight turning (cutting along the periphery of the workpiece); taper turning (creating a taper); step turning (turning different-size diameters on the same work); chamfering (beveling an edge or shoulder); facing (cutting on an end); turning threads (usually external but can be internal); roughing (high-volume metal removal); and finishing (final light cuts). Performed on lathes, turning centers, chucking machines, automatic screw machines and similar machines.