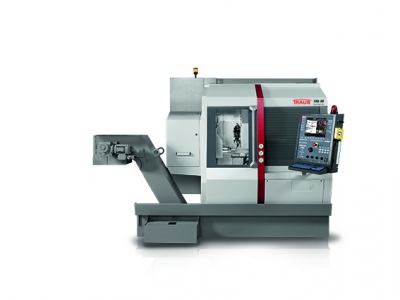
The TRAUB TNL18 series Swiss-style automatic lathes perform even more dynamically with an enhanced CNC, axis amplifier and more dynamic drives, resulting in significantly improved accelerations and top speeds. In extensive tests, the developers made sure that the mechanical conditions of the machine harmonize with the new dynamics.
The new TRAUB TNL18 dynamic includes an optimized drive train which will benefit all machines in the TRAUB sliding/fixed headstock automatic lathe range: the TNL18-7B with its seven linear axes and the B-axis on the upper turret; the TNL18 9 with autonomous counter spindle and nine linear NC axes; the TRAUB TNL18-9P, optimized for series production.
The rugged mechanical construction of the TRAUB TNL18 machines effectively handle the new accelerations, which are up to 25 percent faster than the previous TNL18. Better acceleration and optimized NC programs can reduce machining times by up to 21 percent, while the quality of workpieces remains unchanged.
However, the savings depend also on the complexity of the workpiece. While for a “simple” shaft that is machined mostly at constant cutting speeds and with only a few tool changes, the savings are about 5 percent, it is completely different for a dental implant with numerous different turning, drilling and milling operations. Besides reduced secondary times, the shorter acceleration and deceleration processes allow significantly higher feed rates for these complex cutting contours, resulting in the said 21 percent time savings.
Even if the user does not implement such cycle time-related optimization measures, he still benefits from the new power train. A much higher contour accuracy is possible, and on components with high precision requirements, this can be of great benefit if it reduces the number of measurement processes required.
The new range of machines includes the new control generation TX8i s V7 on the TNL18-7B dynamic and TNL18-9 dynamic. It offers enhanced performance with more powerful hardware. The TX8i-s V7 comes with many convenient features for programming, editing, simulating, setting up and operating. The state-of-the-art 15” multi-touch display allows both conventional menu operation using a keyboard and the use of touch functions.
And with the TX8i-s V7, the user is well prepared for Industry 4.0 and future requirements. The control can also provide a wealth of digital information, process it, and to pass on. It also provides important automation interfaces, such as the industrial M2M communication protocol OPC UA, and allows integrating the machine into the corporate network.
Contact Details
Related Glossary Terms
- computer numerical control ( CNC)
computer numerical control ( CNC)
Microprocessor-based controller dedicated to a machine tool that permits the creation or modification of parts. Programmed numerical control activates the machine’s servos and spindle drives and controls the various machining operations. See DNC, direct numerical control; NC, numerical control.
- feed
feed
Rate of change of position of the tool as a whole, relative to the workpiece while cutting.
- gang cutting ( milling)
gang cutting ( milling)
Machining with several cutters mounted on a single arbor, generally for simultaneous cutting.
- lathe
lathe
Turning machine capable of sawing, milling, grinding, gear-cutting, drilling, reaming, boring, threading, facing, chamfering, grooving, knurling, spinning, parting, necking, taper-cutting, and cam- and eccentric-cutting, as well as step- and straight-turning. Comes in a variety of forms, ranging from manual to semiautomatic to fully automatic, with major types being engine lathes, turning and contouring lathes, turret lathes and numerical-control lathes. The engine lathe consists of a headstock and spindle, tailstock, bed, carriage (complete with apron) and cross slides. Features include gear- (speed) and feed-selector levers, toolpost, compound rest, lead screw and reversing lead screw, threading dial and rapid-traverse lever. Special lathe types include through-the-spindle, camshaft and crankshaft, brake drum and rotor, spinning and gun-barrel machines. Toolroom and bench lathes are used for precision work; the former for tool-and-die work and similar tasks, the latter for small workpieces (instruments, watches), normally without a power feed. Models are typically designated according to their “swing,” or the largest-diameter workpiece that can be rotated; bed length, or the distance between centers; and horsepower generated. See turning machine.
- milling
milling
Machining operation in which metal or other material is removed by applying power to a rotating cutter. In vertical milling, the cutting tool is mounted vertically on the spindle. In horizontal milling, the cutting tool is mounted horizontally, either directly on the spindle or on an arbor. Horizontal milling is further broken down into conventional milling, where the cutter rotates opposite the direction of feed, or “up” into the workpiece; and climb milling, where the cutter rotates in the direction of feed, or “down” into the workpiece. Milling operations include plane or surface milling, endmilling, facemilling, angle milling, form milling and profiling.
- numerical control ( NC)
numerical control ( NC)
Any controlled equipment that allows an operator to program its movement by entering a series of coded numbers and symbols. See CNC, computer numerical control; DNC, direct numerical control.
- turning
turning
Workpiece is held in a chuck, mounted on a face plate or secured between centers and rotated while a cutting tool, normally a single-point tool, is fed into it along its periphery or across its end or face. Takes the form of straight turning (cutting along the periphery of the workpiece); taper turning (creating a taper); step turning (turning different-size diameters on the same work); chamfering (beveling an edge or shoulder); facing (cutting on an end); turning threads (usually external but can be internal); roughing (high-volume metal removal); and finishing (final light cuts). Performed on lathes, turning centers, chucking machines, automatic screw machines and similar machines.