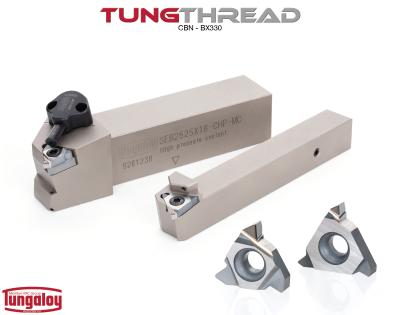
Tungaloy has introduced BX330 CBN grade inserts for its TungThread thread turning tool series.
TungThread series offers a broad range of thread turning inserts and toolholders, covering applications from general threading on CNC lathes and fine threading of precision parts machined on Swiss-type lathes to high-precision premium threads of OCTG pipe connections.
Two new BX330 grade inserts have been added to the series’ 60-degree partial profile threading insert line; namely, 1QP-16ER60-014-SP and 1QP-16ER60-020-SP, both of which feature a brazed CBN tip.
Turning threads on hardened parts can be a challenge when using coated cemented carbide inserts: the cutting edge rapidly wears out before finishing the entire thread profiles, inhibiting greater feed rates and D.O.Cs. to be applied for increased productivity. Of all Tungaloy CBN grades, BX330 provides the cutting edge with the most balanced combination of wear and fracture resistance, making the grade suitable for withstanding continuous and heavy cutting loads inherent in the thread turning method for hardened parts.
Featuring the standard 16ER laydown insert shape, the new CBN threading inserts can be used with existing TungThread toolholders. TungThread now addresses the needs for quick and cost-efficient hard part threading applications with a wide range of standard toolholder sizes available for thread turning. Replace slow thread grinding as the preferred method across industries for producing threads of the hardened parts.
Contact Details
Related Glossary Terms
- computer numerical control ( CNC)
computer numerical control ( CNC)
Microprocessor-based controller dedicated to a machine tool that permits the creation or modification of parts. Programmed numerical control activates the machine’s servos and spindle drives and controls the various machining operations. See DNC, direct numerical control; NC, numerical control.
- cubic boron nitride ( CBN)
cubic boron nitride ( CBN)
Crystal manufactured from boron nitride under high pressure and temperature. Used to cut hard-to-machine ferrous and nickel-base materials up to 70 HRC. Second hardest material after diamond. See superabrasive tools.
- feed
feed
Rate of change of position of the tool as a whole, relative to the workpiece while cutting.
- grinding
grinding
Machining operation in which material is removed from the workpiece by a powered abrasive wheel, stone, belt, paste, sheet, compound, slurry, etc. Takes various forms: surface grinding (creates flat and/or squared surfaces); cylindrical grinding (for external cylindrical and tapered shapes, fillets, undercuts, etc.); centerless grinding; chamfering; thread and form grinding; tool and cutter grinding; offhand grinding; lapping and polishing (grinding with extremely fine grits to create ultrasmooth surfaces); honing; and disc grinding.
- threading
threading
Process of both external (e.g., thread milling) and internal (e.g., tapping, thread milling) cutting, turning and rolling of threads into particular material. Standardized specifications are available to determine the desired results of the threading process. Numerous thread-series designations are written for specific applications. Threading often is performed on a lathe. Specifications such as thread height are critical in determining the strength of the threads. The material used is taken into consideration in determining the expected results of any particular application for that threaded piece. In external threading, a calculated depth is required as well as a particular angle to the cut. To perform internal threading, the exact diameter to bore the hole is critical before threading. The threads are distinguished from one another by the amount of tolerance and/or allowance that is specified. See turning.
- toolholder
toolholder
Secures a cutting tool during a machining operation. Basic types include block, cartridge, chuck, collet, fixed, modular, quick-change and rotating.
- turning
turning
Workpiece is held in a chuck, mounted on a face plate or secured between centers and rotated while a cutting tool, normally a single-point tool, is fed into it along its periphery or across its end or face. Takes the form of straight turning (cutting along the periphery of the workpiece); taper turning (creating a taper); step turning (turning different-size diameters on the same work); chamfering (beveling an edge or shoulder); facing (cutting on an end); turning threads (usually external but can be internal); roughing (high-volume metal removal); and finishing (final light cuts). Performed on lathes, turning centers, chucking machines, automatic screw machines and similar machines.