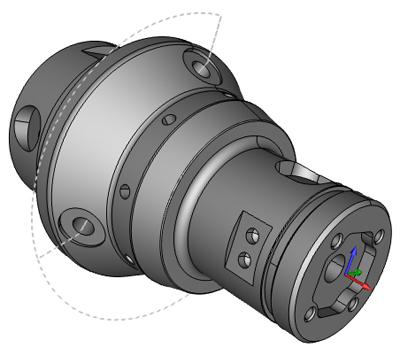
BobCAD-CAM says its new Version 28 CAD/CAM software makes CNC programming faster, easier, and more efficient than ever before. It builds on 30 years of CAD/CAM innovation which includes a powerful 2D & 3D CAD design system, an easy to use wizard driven CAM Programming interface, Dynamic Machining Strategies, advanced 2-5 axis high speed adaptive toolpath capabilities and realistic simulations.
The new v28 CAD/CAM software for CNC programming delivers even more drawing control in CAD, upgrades to the intelligent hole drilling system, the ability to create custom tool shapes for milling tools and enhancements to wrapped toolpath capabilities.
This release was all about expanding high-performance CAD/CAM functionality to enhance machining power, efficiency, and control aspects while maintaining the same ease of use that users depend on to get jobs done faster with superior results, according to the company.
Snap Increments for Dynamic Drawing (Extrude, Rotate, Sketch) – Drawing is now faster and more accurate than ever. All dynamic drawing functions now have snap increment, which acts like a uniform grid in the workspace to which wireframe entities or sketch handles are snapped. Included is a snap increment distance, which is used for most dynamic functions and a snap increment angle for rotation functions. This creates a whole new level of efficiency for dynamic drawing by greatly reducing the number of clicks and data entry modifications. Just set the snap increment and adjust it as needed right from the status bar to create perfectly accurate drawings. This feature can easily be turned on and off with shortcut keys.
Drill Multiple Depths in a Single Feature – All mill hole drilling, tapping, and threading features now use Hole Groups that allow you to define more than one drilling depth within a single machining feature. The software automatically groups all holes that share the same diameter, top of feature, and feature depth, greatly minimizing the number of features needed to get the job done. This makes your drilling features more efficient that ever. You can edit faster and gain greater control of the rapid movements between hole groups using the new Group Retracts.
Advanced Retract Options – The new Group Retracts provide advanced options for defining rapid movements between hole groups. Create planar, cylindrical, or spherical retract areas for all types of drilling scenarios. You can even create the rapid movement to follow the tool orientation or the shortest distance to keep the toolpath clean and efficient.
Standard Drilling – This is the default drilling type that handles 2.5 axis drilling for 3 axis machines, including face drilling for mill turn machines.
Multiaxis Drilling – Multiaxis drilling is a completely new drilling type that handles all drilling for 4 or 5 axis machines with up to 5 axis positioning. This allows you to drill holes of the same diameter in any orientation within a single feature, eliminating the need to create index systems for each orientation.
Cross Drilling – Cross drilling is a completely new drilling type that handles radial drilling for mill turn jobs. Hole Geometry Selection Manager
Hole Geometry Selection Manager – The new selection manager for mill hole features makes it easy to define the drilling type and manage geometry selections. Calculation options are provided to determine how the toolpath is calculated for different geometry types, providing greater efficiency in selection scenarios.
Smart Filtering of Geometry Selections – The software automatically filters geometry selections in two ways: 1. Any duplicates that would result in drilling a hole twice are automatically removed. 2. Geometry selections are filtered based on the drilling type. Once you confirm the selection, all holes that do not have the proper orientation for the selected drilling type are removed.
Use Cylindrical Surfaces to Automatically Set Drilling Parameters – When you select cylindrical surfaces, the software automatically sets the diameter, top feature, and feature depth values for you. Select cylindrical surfaces to speed up your mill hole feature creation.
Custom Tool Shapes for Milling Tools – When creating milling tools, you can now assign geometry to define custom shaped tooling or form tools. You can even define the cutting and non-cutting portions making it easy to create tools that have more than one cutting area. Just create half of the profile to revolve, assign it to the tool, and get accurate programming simulation for all of your custom tooling.
Tabbing for 2 Axis Profiling – The 2 axis wizard now contains a Tabs page, which allows for manual or automatic tab creation for profiling operations. You can allow the software to automatically calculate evenly spaced tabs using a number or distance, or you can manually select the tab location directly from the chains in the workspace. Powerful tab parameters allow you to define tab distance, height, and angle.
Linking Added to 2 Axis Advanced Pocket – The 2 Axis Advanced Pocket now contains a links page giving you more control over the linking parameters of the toolpath. Use a direct, S-link, or retract move between passes or groups with separate controls for each. You can also use the rapid retract for large gaps to speed up the retract moves when there are large gaps along the cut.
Perpendicular Stepover for Advanced Planar – The Advanced Planar operation is further optimized with a new solution for inconsistent finishing in steep areas. The perpendicular stepover option automatically switches the toolpath direction based on a threshold value to create an improved surface finish in steep areas. This efficient toolpath provides a better finish result and reduces cycle times.
Round Corners for Advanced Planar – You can now smoothen the tool movement at sharp corners created in the Advanced Planar toolpath using round corners. Create a more consistent tool engagement and smoother transition for your semi-finishing material removal.
Side and Bottom Allowance – This allows you to specify the finishing allowance separately for the side (XY) and bottom (Z), giving you more control over the roughing toolpath so you can minimize or even eliminate the semi-finishing process for your 3 axis operations.
Wrapped Toolpath Improvements – The Wrapping Group for 4 axis wrapped toolpaths now allows for the selection of wrapped geometry. Eliminate the need to unwrap the geometry first, just select it right from the solid model. You can also use the current stock to set the wrapping diameter. New unwrap controls provide a tolerance value and an arc fit option for the background calculations. You can even select whether to show the toolpath as wrapped or flat, giving you more accurate representation of wrapped toolpaths.
Trim to Stock for 4 Axis Rotary – Trim your rotary toolpath to the stock or a custom STL file to eliminate air cutting and fully optimize your rotary machining.
Revolve Stock Type – Previously only available for lathe jobs, Revolve stock type is now available for all CAM jobs in the Stock Wizard to allow you to define stock geometry by revolving a wireframe chain.
Workpiece Selection for Simulation – Assign workpiece geometry to determine exactly what geometry displays in the simulation window, regardless of how much geometry is visible in the workspace. You can assign workpiece geometry during the job setup or by using the workpiece in the CAM Tree. This works to streamline your simulation and simply the process of comparing cut stock to the workpiece for files with more than one model.
Set Default Stock Transparency – This allows you to set a default stock transparency for CAM jobs. Just open the Stock Transparency dialog box, set the preferred level of transparency, and click Set Default.
New Simulation Interface – The new interface contains a ribbon style toolbar for a more modern CAD/CAM software look and feel.
Related Glossary Terms
- computer numerical control ( CNC)
computer numerical control ( CNC)
Microprocessor-based controller dedicated to a machine tool that permits the creation or modification of parts. Programmed numerical control activates the machine’s servos and spindle drives and controls the various machining operations. See DNC, direct numerical control; NC, numerical control.
- computer-aided design ( CAD)
computer-aided design ( CAD)
Product-design functions performed with the help of computers and special software.
- computer-aided manufacturing ( CAM)
computer-aided manufacturing ( CAM)
Use of computers to control machining and manufacturing processes.
- flat ( screw flat)
flat ( screw flat)
Flat surface machined into the shank of a cutting tool for enhanced holding of the tool.
- gang cutting ( milling)
gang cutting ( milling)
Machining with several cutters mounted on a single arbor, generally for simultaneous cutting.
- lathe
lathe
Turning machine capable of sawing, milling, grinding, gear-cutting, drilling, reaming, boring, threading, facing, chamfering, grooving, knurling, spinning, parting, necking, taper-cutting, and cam- and eccentric-cutting, as well as step- and straight-turning. Comes in a variety of forms, ranging from manual to semiautomatic to fully automatic, with major types being engine lathes, turning and contouring lathes, turret lathes and numerical-control lathes. The engine lathe consists of a headstock and spindle, tailstock, bed, carriage (complete with apron) and cross slides. Features include gear- (speed) and feed-selector levers, toolpost, compound rest, lead screw and reversing lead screw, threading dial and rapid-traverse lever. Special lathe types include through-the-spindle, camshaft and crankshaft, brake drum and rotor, spinning and gun-barrel machines. Toolroom and bench lathes are used for precision work; the former for tool-and-die work and similar tasks, the latter for small workpieces (instruments, watches), normally without a power feed. Models are typically designated according to their “swing,” or the largest-diameter workpiece that can be rotated; bed length, or the distance between centers; and horsepower generated. See turning machine.
- milling
milling
Machining operation in which metal or other material is removed by applying power to a rotating cutter. In vertical milling, the cutting tool is mounted vertically on the spindle. In horizontal milling, the cutting tool is mounted horizontally, either directly on the spindle or on an arbor. Horizontal milling is further broken down into conventional milling, where the cutter rotates opposite the direction of feed, or “up” into the workpiece; and climb milling, where the cutter rotates in the direction of feed, or “down” into the workpiece. Milling operations include plane or surface milling, endmilling, facemilling, angle milling, form milling and profiling.
- milling machine ( mill)
milling machine ( mill)
Runs endmills and arbor-mounted milling cutters. Features include a head with a spindle that drives the cutters; a column, knee and table that provide motion in the three Cartesian axes; and a base that supports the components and houses the cutting-fluid pump and reservoir. The work is mounted on the table and fed into the rotating cutter or endmill to accomplish the milling steps; vertical milling machines also feed endmills into the work by means of a spindle-mounted quill. Models range from small manual machines to big bed-type and duplex mills. All take one of three basic forms: vertical, horizontal or convertible horizontal/vertical. Vertical machines may be knee-type (the table is mounted on a knee that can be elevated) or bed-type (the table is securely supported and only moves horizontally). In general, horizontal machines are bigger and more powerful, while vertical machines are lighter but more versatile and easier to set up and operate.
- profiling
profiling
Machining vertical edges of workpieces having irregular contours; normally performed with an endmill in a vertical spindle on a milling machine or with a profiler, following a pattern. See mill, milling machine.
- solid model
solid model
3-D model created using “building blocks.” This is the most accurate way of representing real-world objects in CAD.
- tapping
tapping
Machining operation in which a tap, with teeth on its periphery, cuts internal threads in a predrilled hole having a smaller diameter than the tap diameter. Threads are formed by a combined rotary and axial-relative motion between tap and workpiece. See tap.
- threading
threading
Process of both external (e.g., thread milling) and internal (e.g., tapping, thread milling) cutting, turning and rolling of threads into particular material. Standardized specifications are available to determine the desired results of the threading process. Numerous thread-series designations are written for specific applications. Threading often is performed on a lathe. Specifications such as thread height are critical in determining the strength of the threads. The material used is taken into consideration in determining the expected results of any particular application for that threaded piece. In external threading, a calculated depth is required as well as a particular angle to the cut. To perform internal threading, the exact diameter to bore the hole is critical before threading. The threads are distinguished from one another by the amount of tolerance and/or allowance that is specified. See turning.
- tolerance
tolerance
Minimum and maximum amount a workpiece dimension is allowed to vary from a set standard and still be acceptable.
- toolpath( cutter path)
toolpath( cutter path)
2-D or 3-D path generated by program code or a CAM system and followed by tool when machining a part.