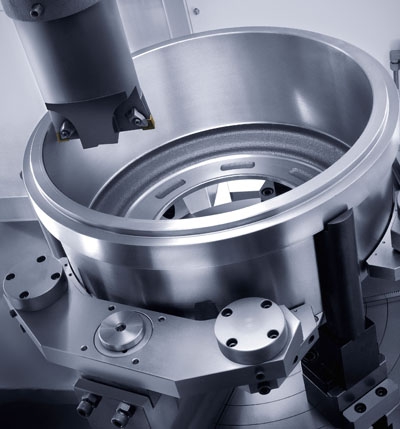
Hwacheon Machinery offers its VT-450/VT-650 single spindle and VT-450/-650-2SP twin-spindle vertical CNC lathes designed for mass production, reducing cutting times for automotive parts such as brake discs, brake drums, hubs and valves. The rigid tool turret offers high speed indexing, providing consistent and stable machining performance, ideal for high-volume cutting of automotive castings and forgings.
These turning centers can be provided with the spindle on the left or the right side or as double machine where the operator can work on two machines with one control, the VT450/-650-2SP. The machines can also be provided with a turnmill option with 3000-rpm spindle to provide even greater machining flexibility for machining more complex large parts complete.
Additionally, Hwacheon's unique Lathe Tool Load Detection System software constantly detects and diagnoses the tool load during machining to reduce tool wear and prevent damage and optimize tool life.
The machines, respectively, provide 24" and 35.3" swing over the bed and handle cutting diameters to 18 and 31.4" with 12 and 18" chuck sizes. The maximum turning diameter zone is designed to provide interference-free operations, providing same maximum diameter at full length even on larger workpieces. A rapid feed (X/Z) of 787 and 630 inch/min. permits quick tool positioning. An 8, 10, or 12-station servo-type tool turret on the VT-450/VT-650 series carries tools up to 2.5" dia. offers indexing time of just 0.2 sec. or less, helping to reduce overall cycle time.
The Hwacheon geared drive system allows for high-torque turning at low speed and also high speed turning. The transmission and the spindle motor are designed separately so that the heat and the vibration generated from the transmission do not affect the spindle motor. For the VT-450, maximum spindle speed is 2500 rpm generated by an 18.5 hp oil-cooled spindle motor. The VT-650 spindle speed is 1500 rpm.
The Hwacheon clean room assembly facility, where the super-precision, super-rigid spindles are manufactured, maintains optimal temperature and humidity, resulting in spindles that meet the toughest quality standard in the industry.
The integrated 45-degree-angle, one-piece machine bed design limits thermal distortion and absorbs vibration effectively and it guarantees high surface quality and precision at high speed. Precision hand-scraped and polished guide ways in all axes and rigid one-piece machine bed design mean the VTLs from Hwacheon are designed to absorb vibration and provide optimum stability in hard turning applications.
The fast and effective chip disposal and the environment friendly oil-water separation design contribute to production efficiency.
Contact Details
Related Glossary Terms
- centers
centers
Cone-shaped pins that support a workpiece by one or two ends during machining. The centers fit into holes drilled in the workpiece ends. Centers that turn with the workpiece are called “live” centers; those that do not are called “dead” centers.
- chuck
chuck
Workholding device that affixes to a mill, lathe or drill-press spindle. It holds a tool or workpiece by one end, allowing it to be rotated. May also be fitted to the machine table to hold a workpiece. Two or more adjustable jaws actually hold the tool or part. May be actuated manually, pneumatically, hydraulically or electrically. See collet.
- computer numerical control ( CNC)
computer numerical control ( CNC)
Microprocessor-based controller dedicated to a machine tool that permits the creation or modification of parts. Programmed numerical control activates the machine’s servos and spindle drives and controls the various machining operations. See DNC, direct numerical control; NC, numerical control.
- feed
feed
Rate of change of position of the tool as a whole, relative to the workpiece while cutting.
- hard turning
hard turning
Single-point cutting of a workpiece that has a hardness value higher than 45 HRC.
- lathe
lathe
Turning machine capable of sawing, milling, grinding, gear-cutting, drilling, reaming, boring, threading, facing, chamfering, grooving, knurling, spinning, parting, necking, taper-cutting, and cam- and eccentric-cutting, as well as step- and straight-turning. Comes in a variety of forms, ranging from manual to semiautomatic to fully automatic, with major types being engine lathes, turning and contouring lathes, turret lathes and numerical-control lathes. The engine lathe consists of a headstock and spindle, tailstock, bed, carriage (complete with apron) and cross slides. Features include gear- (speed) and feed-selector levers, toolpost, compound rest, lead screw and reversing lead screw, threading dial and rapid-traverse lever. Special lathe types include through-the-spindle, camshaft and crankshaft, brake drum and rotor, spinning and gun-barrel machines. Toolroom and bench lathes are used for precision work; the former for tool-and-die work and similar tasks, the latter for small workpieces (instruments, watches), normally without a power feed. Models are typically designated according to their “swing,” or the largest-diameter workpiece that can be rotated; bed length, or the distance between centers; and horsepower generated. See turning machine.
- lathe bit ( lathe tool)
lathe bit ( lathe tool)
Cutting tool for lathes and other turning machines. Normally a single-point cutting tool, square in cross section and ground to a shape suitable for the material and task. Intended for simple metal removal, threading, slotting or other internal or external cutting jobs. Clearance to prevent rubbing is provided by grinding back rake, side rake, end relief and side relief, as well as side- and end-cutting edges.
- turning
turning
Workpiece is held in a chuck, mounted on a face plate or secured between centers and rotated while a cutting tool, normally a single-point tool, is fed into it along its periphery or across its end or face. Takes the form of straight turning (cutting along the periphery of the workpiece); taper turning (creating a taper); step turning (turning different-size diameters on the same work); chamfering (beveling an edge or shoulder); facing (cutting on an end); turning threads (usually external but can be internal); roughing (high-volume metal removal); and finishing (final light cuts). Performed on lathes, turning centers, chucking machines, automatic screw machines and similar machines.