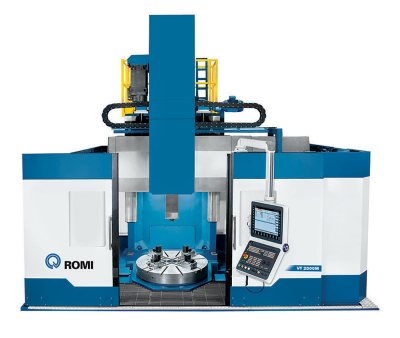
Romi's VT Series Vertical CNC Lathes includes six models ranging from the VT 1400M with a load capacity of 22,000 lbs. to the massive VT 6000 that will handle 198,400 lbs. on chuck. The ability to effectively machine parts this size are made possible in large part to Romi’s cast iron monoblock beds, columns and vertical carriage. The robust mechanical structure provides exceptional rigidity, stability and versatility for machining workpieces found in heavy industry.
The series includes the VT 1400M, VT 2000M, VT 2500M, VT 3000M, VT 5000 and VT 6000 with table sizes from 1,400 (55") to 6,000mm (236) with maximum turning diameter from 1,600mm (63") up to 7,000mm (276”) and maximum height allowed from 1,650 (65") to 4,000mm (157").
All models feature vertical RAM, C axis, 31kW live tooling with spindle taper ISO 50 with either a 10 or 20 tool magazine, and linear scales for machining precision. The VT Series are equipped with a Siemens Sinumerik 840D SL CNC with a large 19” LCD color monitor, USB port and Ethernet interface.
Contact Details
Related Glossary Terms
- chuck
chuck
Workholding device that affixes to a mill, lathe or drill-press spindle. It holds a tool or workpiece by one end, allowing it to be rotated. May also be fitted to the machine table to hold a workpiece. Two or more adjustable jaws actually hold the tool or part. May be actuated manually, pneumatically, hydraulically or electrically. See collet.
- computer numerical control ( CNC)
computer numerical control ( CNC)
Microprocessor-based controller dedicated to a machine tool that permits the creation or modification of parts. Programmed numerical control activates the machine’s servos and spindle drives and controls the various machining operations. See DNC, direct numerical control; NC, numerical control.
- turning
turning
Workpiece is held in a chuck, mounted on a face plate or secured between centers and rotated while a cutting tool, normally a single-point tool, is fed into it along its periphery or across its end or face. Takes the form of straight turning (cutting along the periphery of the workpiece); taper turning (creating a taper); step turning (turning different-size diameters on the same work); chamfering (beveling an edge or shoulder); facing (cutting on an end); turning threads (usually external but can be internal); roughing (high-volume metal removal); and finishing (final light cuts). Performed on lathes, turning centers, chucking machines, automatic screw machines and similar machines.